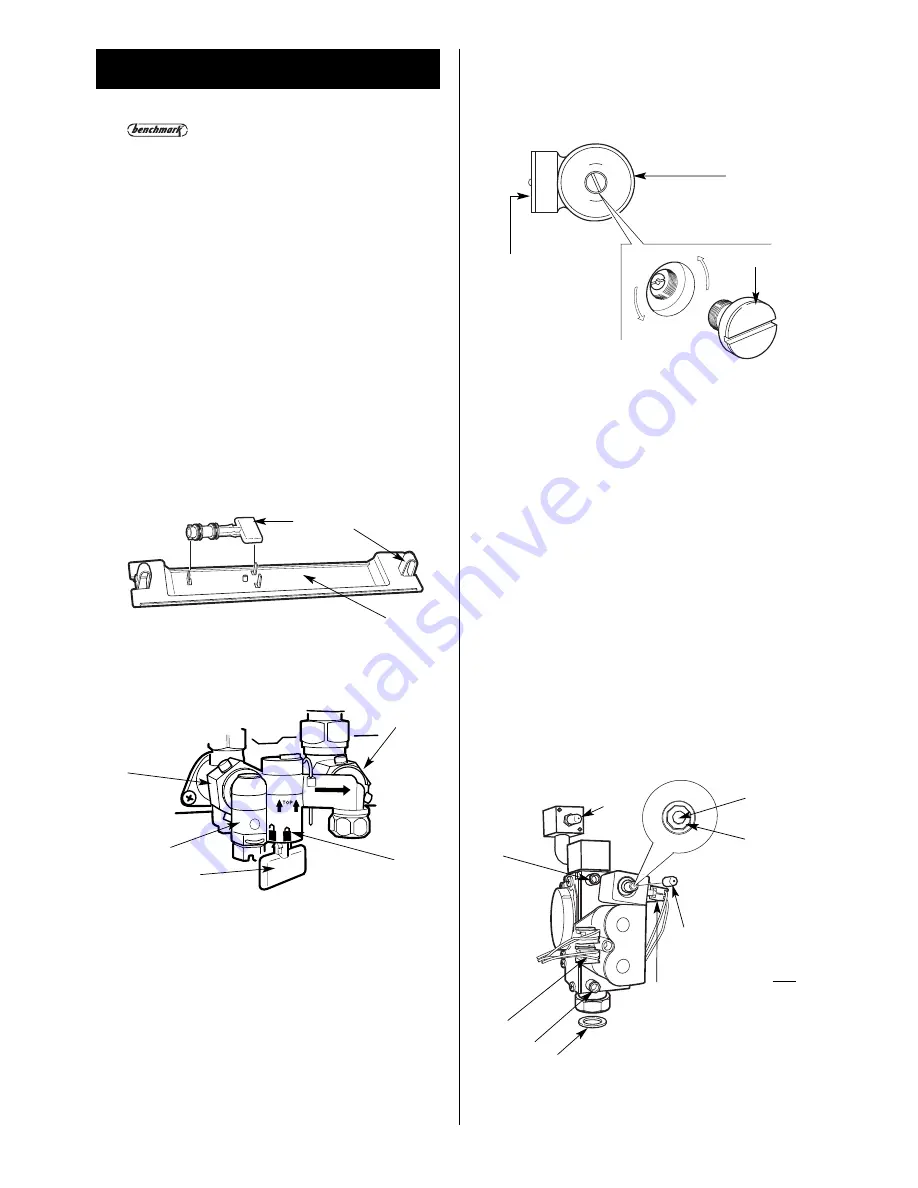
In Eire additional guidance on commissioning is contained in
paragraph 15 of IS 813:2001
13.1
Water Treatment: For optimum performance
after installation, this boiler and its associated central heating
system should be flushed in accordance with the guidelines given
in BS7593 – Treatment of water in domestic hot water heating
systems. Full instructions are supplied with proprietary cleansers
sold for this purpose. If an inhibitor is to be used after flushing, it
should be used in accordance with the manufacturers instructions.
Remove all system cleanser before adding any inhibitor.
Suitable flushing agents and inhibitors are available from Betz
Dearborn on 0151 4209563 or Fernox Tel: 01799 550811.
13.2
This text describes the filling and venting of the appliance and
system when the optional internal filling loop is fitted.
Any external filling loop must be WRAS approved. Refer to Fig. 8 b.
It is very important that the appliance and system are fully vented.
Pull off the clip on bottom panel. Refer to Fig. 32.
Remove the cabinet by pulling off the clip-on facia cover.
Unscrew the two fixing screws, release the sides and lift from the
top location.
Check that the electrical supply and the gas supply to the
appliance are turned off and that all the water connections
throughout the system are tight.
Open the system valves at the appliance. Refer to Fig 13.
Open all the radiator valves.
13.3
Remove the key from the bottom panel and insert into the
filling loop. Refer to Fig. 32 and 33.
Open the mains cold water inlet valve .
Turn the key clockwise to unlock the filling loop.
The system will fill.
Vent each radiator in turn. The automatic air vent will vent the
appliance.
It is very important that the appliance and system are fully
vented and that all air pockets are removed.
Remove the cap from the pump and turn the shaft about half a
turn. Replace the cap. Refer to Fig. 34.
Check that the pressure relief valve operates by turning the knob
anti-clockwise until it releases. Refer to Fig. 17. Water should be
expelled from the discharge pipe.
13.4 Set the Expansion Vessel Pressure
The charge pressure of the expansion vessel as dispatched is
0.5bar, which is equivalent to a static head of 5m. The charge
pressure must not be less than the static head at the point of
connection. A Schraeder type valve is fitted to the top of the
expansion vessel to allow the charge pressure to be increased if
necessary. Refer to Fig. 15.
The expansion vessel must be charged to 0.35bar less than the
initial system design pressure.
Note: 1bar = 10.2m of water.
13.5 Set the System Pressure
Fill the system until the pressure gauge is at 2.5bar and check for
leaks. Turn the filling key anti-clockwise to shut the filling loop.
Replace the key in the bottom panel. Release water from the
system drain point until the required system pressure is
obtained, upto a maximum of 1.5bar. Set the pointer on the
pressure gauge to record the set system pressure.
If the pressure indicated on the gauge is greater than 2.65bar when
operating at the maximum central heating temperature then an
extra expansion vessel must be fitted to the system as close as
possible to the appliance central heating return connection.
13.6 Clock/Programmer
The controls fitted to the appliance should be set up at this
stage. Refer to the instructions sent with the control.
13. Commissioning The Appliance
20
Fig. 32. Bottom Panel
Fig. 34. Pump venting.
Pump
Pump
cap
Electrical
connections
cover
Fig. 35. Gas valve.
Maximum
2mm
Allen key
Minimum
3mm
Allen key
1
Clockwise to
increase
Anti-clockwise
to decrease
Slight
movement
only is
required
2
1
3
1. Bottom panel
2. Filling key
3. Fixing clips
Fig. 33. Filling Loop (optional)
1
5
4
4
2
1. Filling loop
4. CH Return
2. Filling key
5. Mains water inlet
3. Lock/unlock Fill position
2
3
4
5
1. Burner pressure test point
2. Main gas valve connections
3. Inlet pressure test point
4. Electrical connections modulator
(Blue:Blue)
5. Gas valve sealing cap
6. Fibre washer
7. Injector
6
7