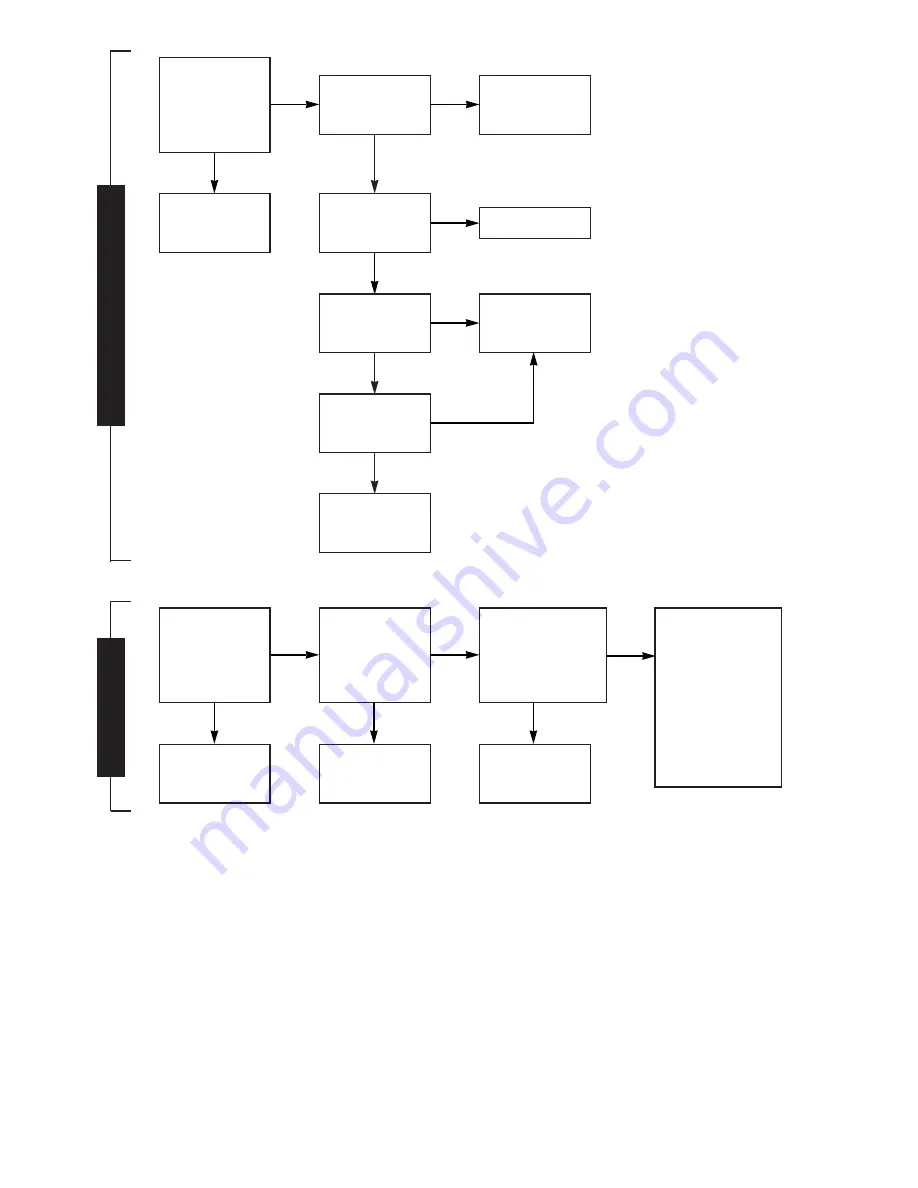
31
Red diode is
damaged. Replace
control board.
(Section 16.4.22)
Is there a link at
terminal
ST13
pins
1
and
2
?
Is there an electronic
programmer at
position
ST5
at right-
hand end of board?
Replace control board.
(Section 16.4.22).
With CH control knob
fully clockwise, does
the boiler ignite and
appear to run
normally in central
heating mode?
Is there 230V AC
across terminal
ST8
pins
LR
and
N
?
There is no heat
demand. Check room
thermostat or mains
programmer (or link).
Insert a link
FAIL POINT D
No
No
No
No
No
Yes
Yes
Remove programmer
connector from board
edge. Does CH lamp
now light?
Yes
Correctly set or
replace electronic
programmer.
Yes
Yes
Red diode is
damaged. Replace
control board.
(Section 16.4.22)
Replace control board.
(Section 16.4.22).
With a hot water tap
fully open, does the
boiler ignite and
appear to run
normally in hot water
mode?
Remove multiway
connector from board
position
ST16
. With
tap still open is there
continuity across
contacts
19
and
20
(2 pink wires)?
Remove the black cover
from the microswitch
assembly. With tap still
open is there continuity
between the two
connected terminals
(
C
and
NO
)?
Visually observe if the
plunger on the diverter
valve assembly is pushing
the microswitch button
(
Note:
May be helpful if
tap is repeatedly turned
on and off). If plunger
moves replace
microswitch (Section
16.4.15). If plunger does
not move replace water
diverting valve.
(Section 16.4.16).
Repair or replace
wiring/harness
FAIL POINT E
No
No
No
Yes
Yes
Yes
Summary of Contents for 24CDi BF
Page 26: ...26 ...