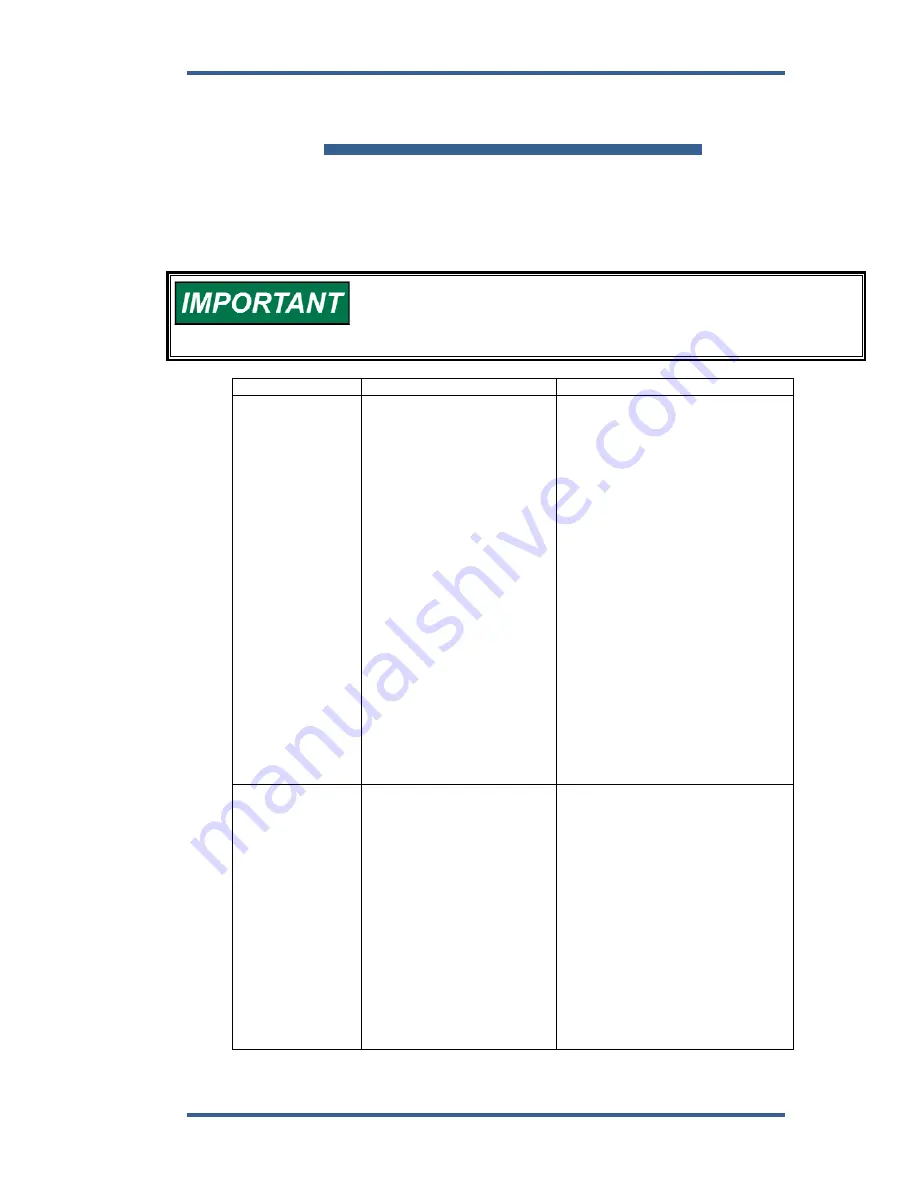
Manual 02029
Load Sharing Module (Analog Output)
Woodward
19
Chapter 5.
Troubleshooting
Introduction
If the Load Sharing Module is determined not to be operating correctly, use the
following troubleshooting chart to find the problem. The causes for each
symptom are given with the most likely cause first.
This troubleshooting section is intended only as a guide. There may
be other causes for a symptom than those given, and there may be
repairs not given which may be more suited to the particular
situation.
Symptoms Cause
Test/Remedy
Undesirable speed
decrease with load
increase.
1. Droop mode switch is open
or auxiliary contract is open.
Load Sensor is in droop
mode.
2. Improper engine operation.
Operate the engine and
observe speed while applying
load. Note the position of the
actuator terminal shaft.
3. Faulty engine or speed
control. Disconnect the load
sensor from the speed
control. Load the engine as a
single, isolated unit.
Jumper Load Sensor terminals 13
and 14.
Observe engine operation. Replace
wiring or switch as required. (The
Load Sharing Module will be in
droop when the circuit breaker
auxiliary contact is open. See Droop
Switch under Electrical Wiring
section of Installation chapter.)
If the droop occurs near the full load
point only, it is possible the engine is
not producing the power called for by
the fuel control, or is being
overloaded. Either is indicated if the
fuel control is at maximum fuel
position.
If speed decreases with load, either
engine operation or the speed
control may be faulty. You may be
exceeding the load rating of the
engine or there may be insufficient
fuel flow.
Erratic Load
Sensor Operation.
1. Open or intermittent wire.
2. EMI (Electromagnetic
Interference).
Check all wiring for continuity and
tight connections. Repair if
necessary.
Remove ground loops. Shield all
wiring, grounding shield at one end
only. Route wiring and controls away
from high current wires and noise
sources. (Equipment containing
SCRs is especially noisy.) Keep wire
lengths to a minimum. Route wiring
through conduit when possible. Use
single point grounds. Take control
power right off battery. (Do not use
distribution points or take off starter.)
Run additional equipment off
separate battery wires.
Summary of Contents for 9907-026
Page 6: ...Load Sharing Module Analog Output Manual 02029 iv Woodward ...
Page 10: ...Load Sharing Module Analog Output Manual 02029 4 Woodward Figure 1 3 Plant Wiring Diagram ...
Page 23: ...Manual 02029 Load Sharing Module Analog Output Woodward 17 Figure 4 1 Block Diagram ...
Page 31: ...Manual 02029 Load Sharing Module Analog Output Woodward 25 ...