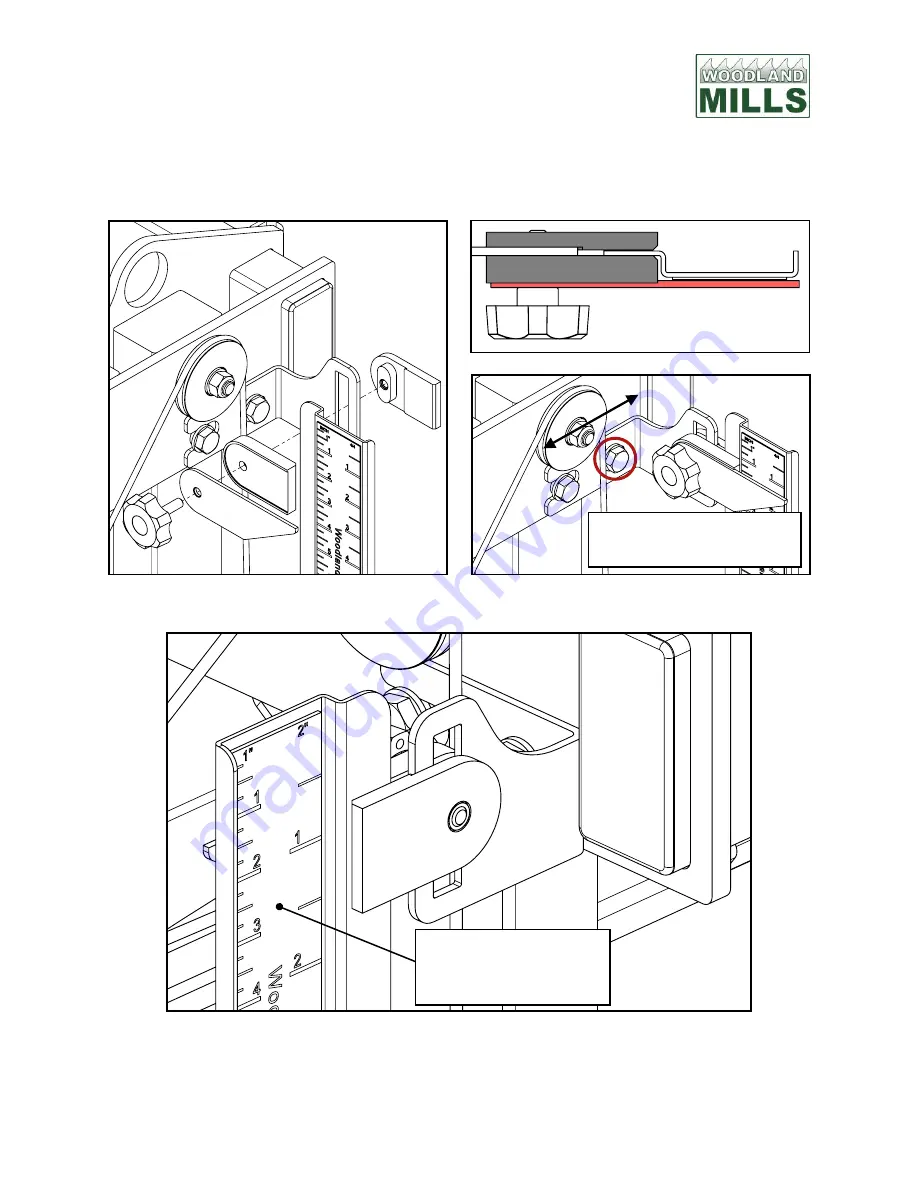
HM130MAX Operator’s Manual
Assemble the guide, locking plate, and indicator arrow to the log scale indicator bracket using
the M8 threaded knob. Adjust the position of the indicator bracket forwards or backwards if the
guide and locking plate bind on the log scale bracket as the sawhead is raised and lowered.
Store the other magnetic scale on the front side of the log scale bracket when not in use.
HM130MAX-MY2020: Rev B
Page
of
40
92
04-Dec-2019
Store unused magnetic
scale on front side of
log scale bracket
Adjust position of indicator
bracket to prevent binding
Summary of Contents for HM130MAX
Page 2: ...This page intentionally left blank...
Page 93: ...HM130MAX Operator s Manual NOTES HM130MAX MY2020 Rev B Page of 91 92 04 Dec 2019...
Page 94: ...HM130MAX Operator s Manual HM130MAX MY2020 Rev B Page of 92 92 04 Dec 2019...
Page 95: ...This page intentionally left blank...
Page 96: ......