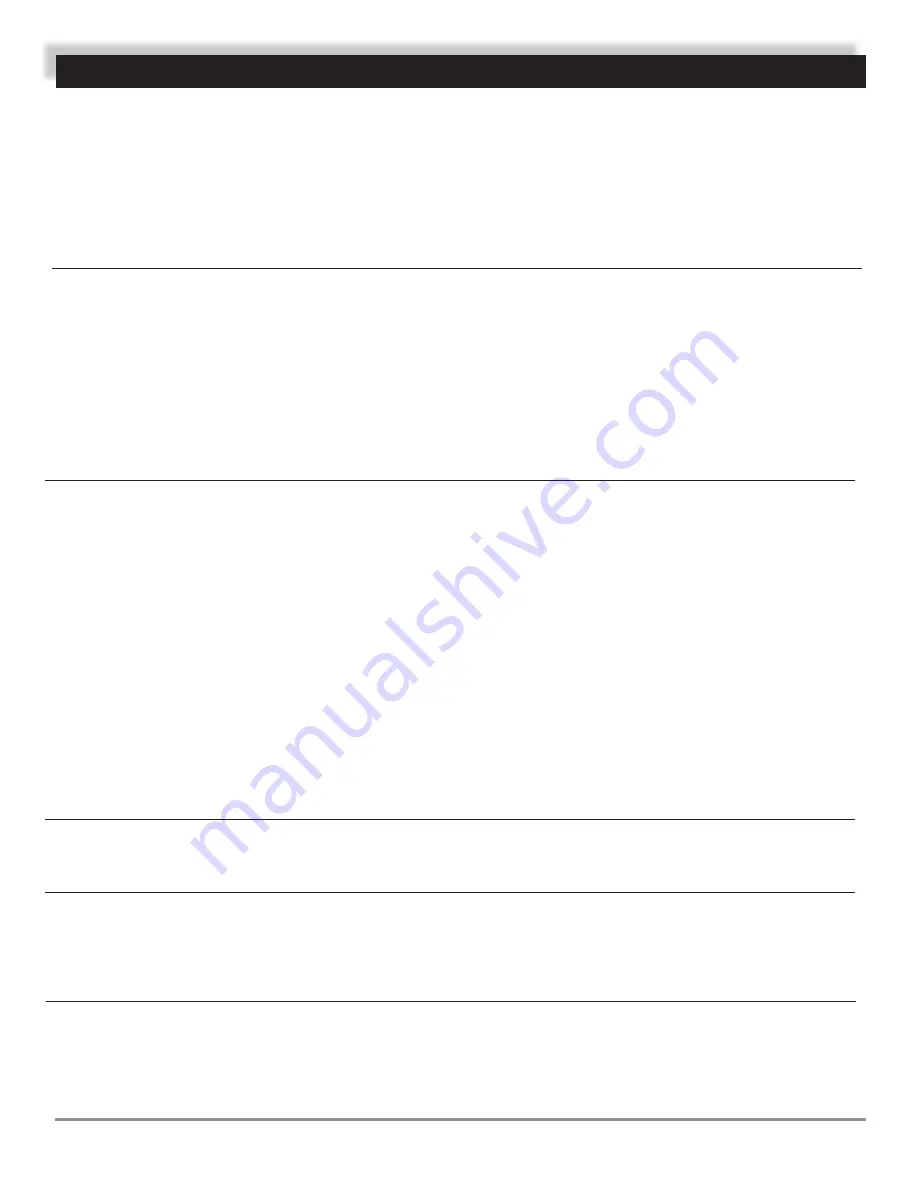
SYMPTOM
POSSIBLE CAUSE
ACTION
1. Spark ignitor will not
light pilot after repeated
triggering of piezo.
2. Pilot will not stay lit
after carefully following
lighting instructions.
A. Wire disconnected.
B. Defective ignitor.
C. No gas or low gas pressure.
D. No Propane/LPG in tank
A. Defective thermocouple
B. Defective valve
A. Open door and check to make sure wire is connected to ignitor.
B. Check for spark at electrode and pilot. If no spark and electrode
wire is properly connected, replace pilot assembly.
C. Check remote/manual shut off valve from fireplace. Low pressure
can be caused by bent lines, restricted lines, low pressure line pres-
sure. Consult with plumber or gas supplier.
D. Check Propane/LPG tank. Refill tank.
A. Check that thermocouple flame impinges on thermocouple. Clean
and/or adjust pilot for maximum flame impingement. Ensure that
the thermocouple connection at the gas valve is fully inserted and
tight.
Disconnect the thermocouple from the valve, place one millivolt
lead wire on the tip of the thermocouple and the other meter lead
wire on the thermocouple copper lead. Start the pilot and hold the
valve knob in. If the millivolt reading is less than 15 mV, replace
pilot assembly.
B. If thermocouple is producing more than 15 mV, replace
faulty valve.
TROUBLESHOOTING
3. Pilot burning, valve
knob turned to “ON”,
switch is turned to
burner will not ignite.
4. Frequent pilot outage
problem.
5. The pilot and main
burner extinguish while
in operation
A. Defective switch, wall switch,
remote control or wire
B. Pilot flame too small
C. Defective or malfunctioning
thermopile
D. Defective valve
A. Pilot flame may be too high or
too low, causing pilot safety to
drop out
A. Inner vent pipe leaking exhaust
gases back into system
B. Horizontal vent improperly
pitched
C. Improper vent cap installation
A. Check switch and wire for proper connection. Place jumper wires
across terminals of switch. If burner comes on, replace defective
switch.If the switch is OK, repeat the same procedure on remote
control If burner comes on, replace remote control.
Place jumper wire across wire at gas valves (terminals marked TH
and TP/TH). If burner comes on, wires are faulty or connections
are bad. Replace wire.
B. If pilot flame is not close enough to the thermopile, adjust
pilot flame.
C. Check thermopile wire connections to make sure all are tight and
that the thermopile is fully inserted into pilot assembly. Check
thermopile with a millivolt meter. Connect leads to TP and TP/
TH terminals on the control valve. If meter reading is below 325
mV, replace pilot assembly.
D. Turn valve knob to “O
N
” and switch to “ON.” Take a reading at
the thermopile leads (TP & TP/TH) on the valve. If the meter
reads greater than 175 mV and the burner does not light, replace
defective valve.
A. Clean and adjust the pilot flame for maximum flame impingement
on thermocouple.
A. Check for flue product leak. Replace defective pipe section.
B. Check horizontal-venting piping is running upward 1/4" per foot.
Do not run the pipe level or downward.
C. Check for proper installation and freedom from debris or blockage.
6
. Flame burn blue and
lifts off burner (ghost-
ing)
A. Insufficient oxygen being supplied
A. Ensure that the vent cap is installed properly and free of debris. Ensure that
the vent system joints are tight and have no leaks. Ensure that no debris has
been blocking the inner air intake at the bottom back of the combustion
chamber. Ensure that the glass is properly secure and latch.
43
B. Check that inlet pressure meets requirements.
“ON”, but
Summary of Contents for MONTEREY-(N
Page 31: ...LOG SET 31...
Page 32: ...Figure 41 Log set placement LOG SETT contunue 32...
Page 44: ...127 6...
Page 45: ...127 6...
Page 46: ...127 6...