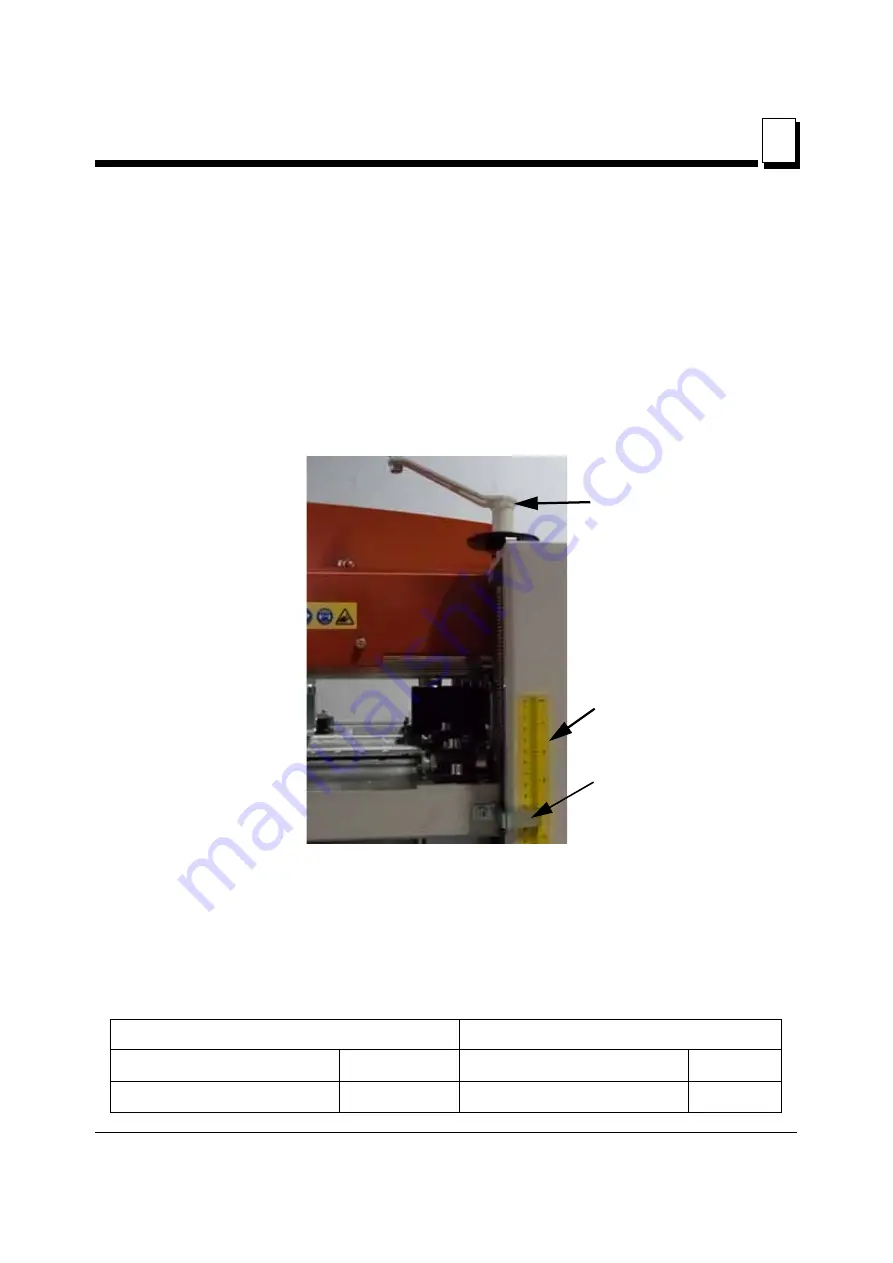
Setup
Adjusting upper cutter depth
Setup
doc081920
3-16
3
Adjusting upper cutter depth
The cutting depth of the upper cutter is adjusted by turning the adjustment crank handle
that raises and lowers the cast iron table in the planer. Each turn of the crank raises or
lowers the machine table 5/32” (4 mm).The scale on the front of the machine indicates the
thickness of the finished material. The scale shows both metric and Imperial measure-
ments.
By loosening the indicator screw and moving the indicator upwards or downwards, the
scale can be calibrated to match the takeoff of the upper cutter.
See Figure 3-9.
The depth of cut is determined by the thickness of the rough board before it enters the
planer, less the amount of takeoff from the lower cutter, less the amount of the thickness
of the finished board.
Examples:
FIG. 3-9
Imperial
Metric
Rough lumber thickness
1-1/16 "
Rough lumber thickness
26 mm
Takeoff of lower cutter
1/16"
Takeoff of lower cutter
2 mm
Scale
Adjustment
handle
Scale Indicator