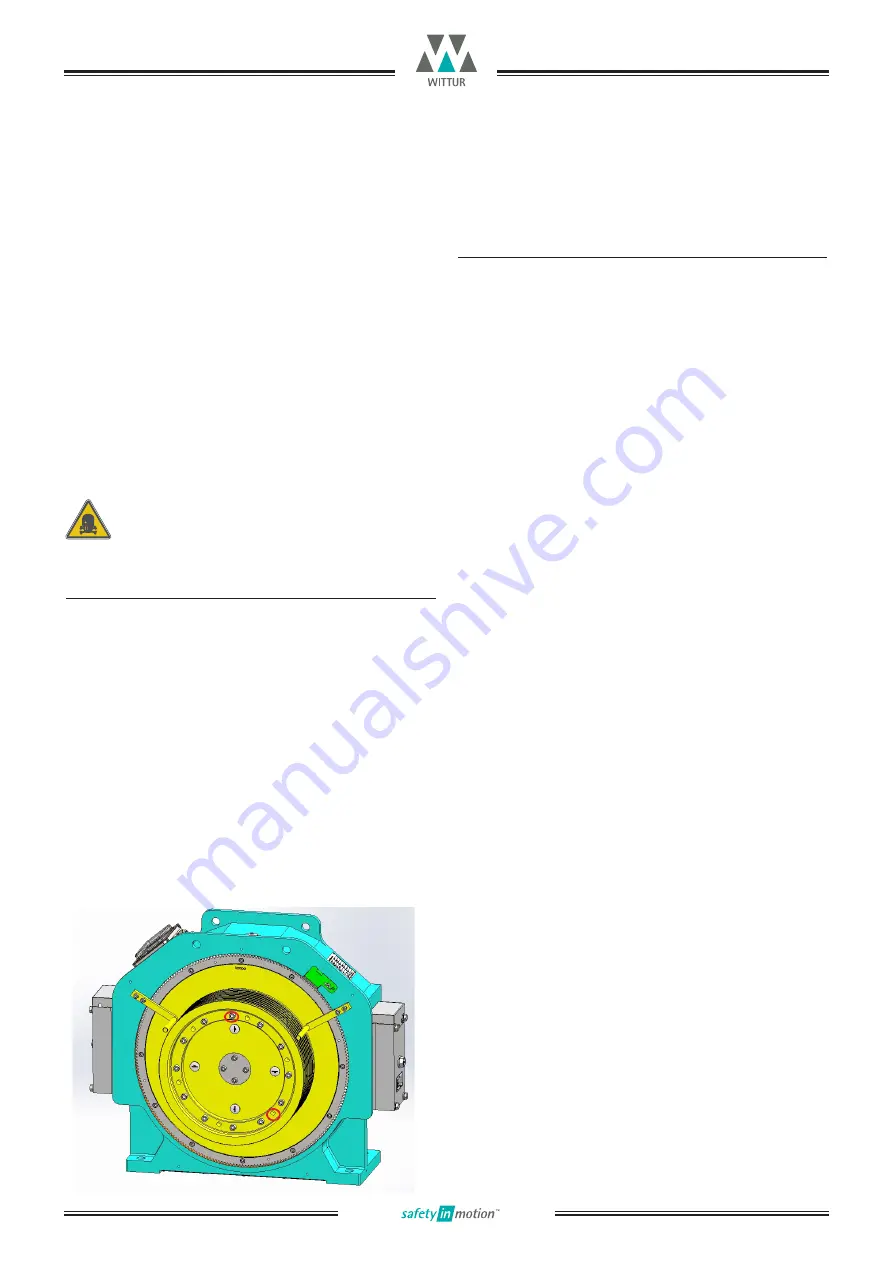
Page 21
Date 11.29.2016
Version A
Code J40069
Subject to changes without notice!
Gearless Synchronous Lift Machines
WSG-10
Operating and Maintenance Manual
12.5 Mechanical evacuation device
12.6 Replacing the traction sheave
When the mechanical evacuation device ordered, a
fixed gear is mounted on the traction sheave. In urgent
case, insert the Hand wheel into the supporting shaft
then turn the traction sheave by engagement to move
the car.
When the mechanical evacuation device ordered, a
xed gear is mounted on the traction sheave. In urgent
case, insert the Hand wheel into the supporting shaft
then turn the traction sheave by engagement to move
the car.
Danger
The traction sheave has to be replaced
when in a limited situation.
Disassembly
• Power off the system and safeguard against un-
intentional reclosing.
• Secure the car and the counter-weight.
• Remove the rope slip-off guards and the rope
guards, if provided.
• Relieve the load on the traction sheave; remove
the ropes.
• Support the traction sheave by means of a
hoisting gear.
• Remove the 12×M12 fastening bolts.(red cycle)
• Insert the M12×80-8.8 (or above) bolts into the two
threaded forcing holes and force off the traction
sheave. (red circle)
Assembly
• Clean the traction sheave and the rotor ange.
• For better assembly heat up traction sheave.
• Slide the traction onto the rotor ange as far as
possible.
• Insert the fastening bolts and tighten diagonally
oppo- site bolts. Use "omni t 100" or a similar
adhesive to secure the bolts. Tighten them along
the bolt hole circle (MA = 79 Nm) with a torque
spanner.
• Replace the ropes and reinstall the rope slip-off
guard.
Summary of Contents for WSG-10
Page 32: ......