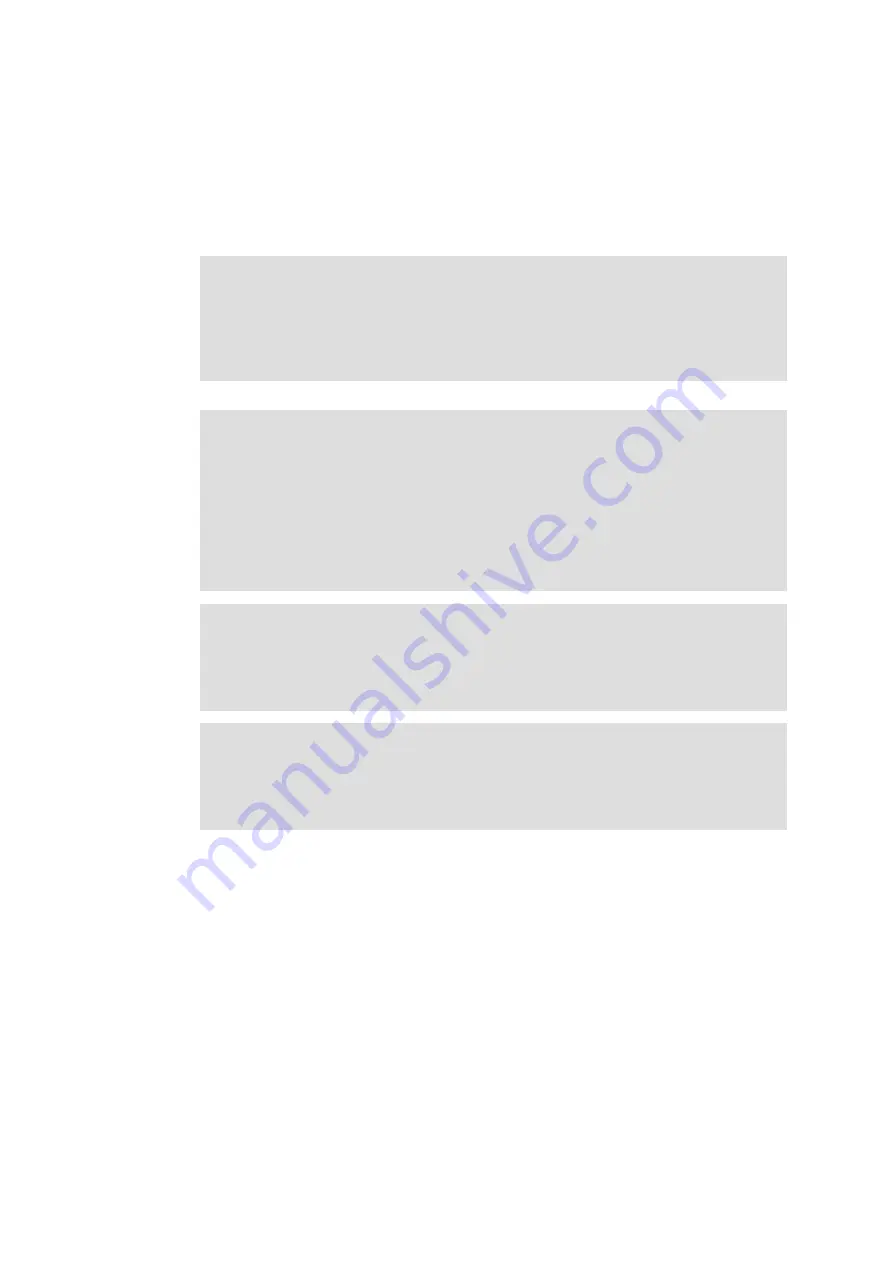
Electrical installation
5
i
j
| BA 14.0197 | 11/2010
31
5
Electrical installation
5.1
Electrical connection
5.1.1
Important notes
Danger!
| Perform electrical connection only when no voltage is applied.
| If an "emergency stop" is carried out without the protective circuit provided,
the control device may be destroyed. Observe the correct polarity of the
protective circuit!
Stop!
| For checking the individual braking circuits, it must be possible to switch off
the power supply separately for each braking circuit. For a new overexcitation
during switch−on, switches K1/K3 must be opened, too.
| The suppressor circuit included in INTORQ switchgear BEG−561−255−130
(terminals 3 and 4) may not be used in lift or hoist applications. In this case,
the suppressor circuit must be connected in parallel to the brake coil (see
Fig. 14).
Danger!
| Electrical connection must only be carried out by skilled personnel!
| Connections must only be made when the equipment is de−energised! Danger
through unintended starts or electric shocks.
Stop!
| It must be ensured that the supply voltage corresponds to the nameplate
data.
| Voltages must be adapted to the local environment!