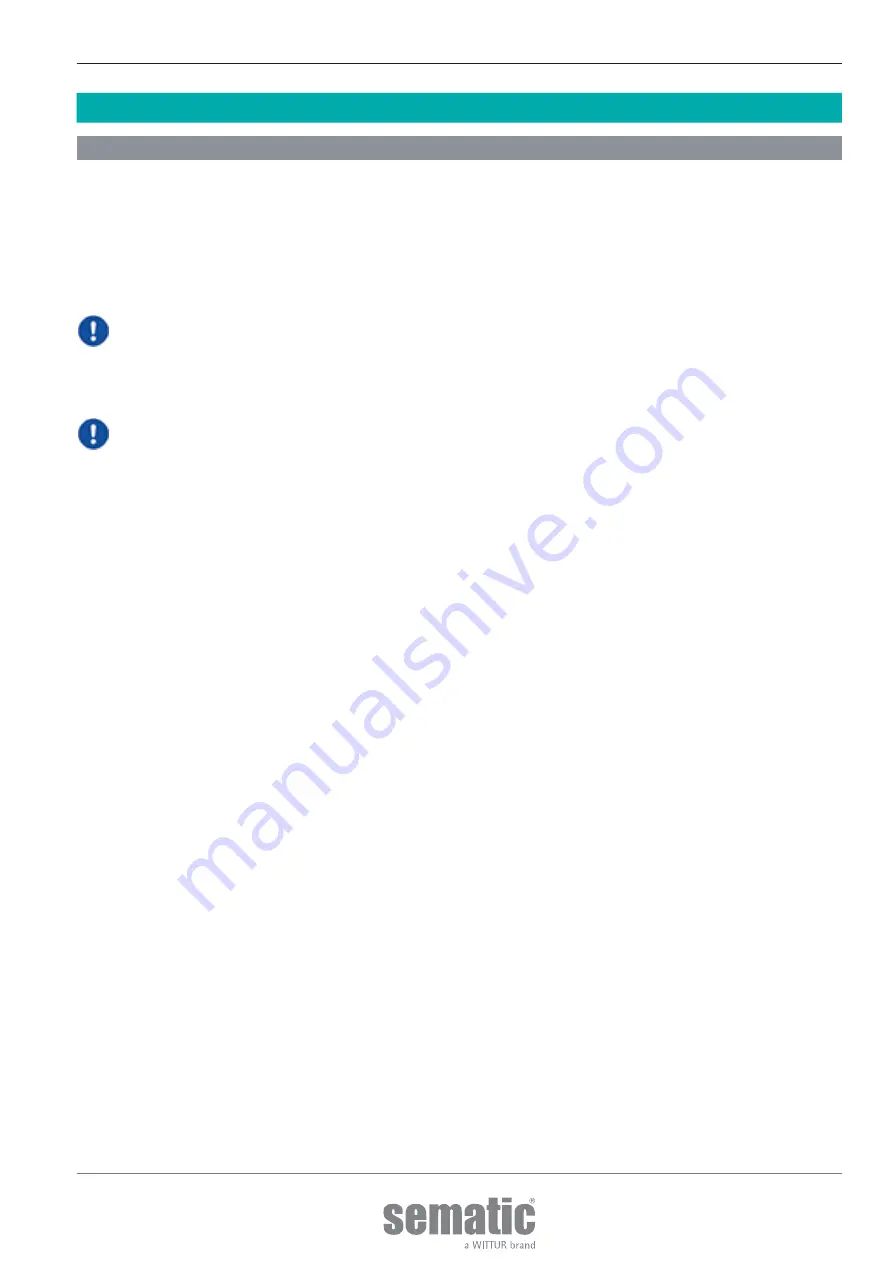
26
www
.wittur
.com
© WI
TTUR • All rights r
eser
ved
PM.2.004921.EN - 808-001-000 SDS
©
rel 3 · Edition 22 July 2020
Drive - Instruction Manual
6 FUNCTIONS AVAILABLE
6.1 REVERSING
Parameter for managing the reversing function during the door closing cycle. This is divided into:
6.1.1 Reversing system force setting (Param. Code 09)
The reverse motion torque parameter sets the sensitivity degree to detect an obstacle during the door closure, thus giving the reopening
command. The parameter’s value can be manually set.
Please note that a lower sensitivity corresponds to higher values and vice versa.
Fset with Parameter 42 Off (00)
- The value can be set within the Fmax and Fmin range
- The value will remain stable during time
- Always perform a measure of closing force with a suitable equipment in case of Fset value set out of the limits foreseen by regulation.
Fset with Parameter 42 On (01)
- The value can be set within the Fmax and Fmin range
- Fset valuewill adjust automatically during time to reach the maximum sensibility
Note 1: Back to "Reversing force setting" menu you can notice that the set value is changed
Note 2: If necessary you can decrease the sensibility increasing Fmin value parameter (only with handset)
- Always perform a measure of closing force with a suitable equipment in case of Fset value set out of the limits foreseen by regulation.
6.1.2 Reversing system offset
The set value represents the size of the space (expressed as a percentage) for disabling the “Reversing” function. By decreasing the
percentage (values < 100%) the controller is able to improve the reactivity of the system in reversing situations even with obstacles with
small dimensions.
6.2 REVERSING SYSTEM CHOICE: INTERNAL OR EXTERNAL (PARAM. CODE 00)
If the reversing system is internal, the reopening of the doors due to obstacle detection is solely controlled by the Door Controller and
door reopening is signalled to the main lift controller through the IM contacts (1, 4 contacts normally closed, 2, 4 contacts normally open).
If the reversing system is external-MOVING, the Door Controller signals, through the IM contacts, the presence of an obstacle to the main
lift controller, which in turn must signals the re-opening command using Ka. The IM signal is present up to the complete reopening of the
doors.
If the main lift controller does not give the re-opening signal during the doors movement, the Door Controller commands a low-speed
closure.
If the doors are completely open and an obstacle is present, the door controller does not allow the door to close until a Kb (forced closing)
is given from the main lift controller.
If the reversing system is external- PARKING, the Door Controller signals, through the IM contacts, the presence of an obstacle
to the main lift controller, which in turn must signals the re-opening command using Ka. The IM signal is present up to the complete
reopening of the doors.
If the main lift controller does not give the re-opening signal, the Door Controller commands a low-speed closure.
If the doors are completely open and an obstacle is present, the door controller allows to close the door if a Kb (forced closing) is given
from the main lift controller. If a Kc closing signal is given from the main lift controller, the door controller commands a low-speed
closure and shows a “Reversing system fault”
6.3 MAIN LIFT CONTROLLER TEST (PARAM. CODE 01)
When set to “OFF” selection (no Main Lift Controller Test), a simple impulse of signal Ka or Kc from the Main Lift Controller is sufficient
to produce door movement; the signal is stored by the Door Controller which will complete the required movement even if the main lift
controller signal fails. The impulse width must be at least 400ms in duration.
When the Main Lift Controller Test is set to “When Moving” (default setting) or set to “ Parking”, the operation is as described in
the next two sections.
6.3.1 Main Lift Controller Test (when moving) [default setting]
When this parameter is set to “WHEN MOVING”, the Door Controller checks for the Ka or Kc signal coming from the main lift controller
only during the door movement (Ka signal during the opening cycle, Kc signal during the closing cycle). At the end of the movement,
which can be detected through the La and Lc signals, respectively Door Open and Door Closed, it is possible to remove the signal that has
controlled the movement, without the Door Controller detecting this as failure.
For this setting, the main lift controller must be equipped with 2 relays: 1 for the opening command, and 1 for the closing command.
The Door Controller checks for continuous presence of the Ka and Kc signals coming from the main lift controller.
The Door Controller detects signal drops exceeding 200ms; this is interpreted as NO MLC Signal alarm if the relevant parameter MAIN
LIFT CONTROLLER TEST is set on “WHEN MOVING”.
In case of signal failure, the Door Controller acts as described in the parameter setting NO MLC SIGNAL.
6.3.2 Main Lift Controller Test (when parking)
If the main lift controller test is set to PARKING, the Door Controller checks for the Ka or Kc signals coming from the main lift