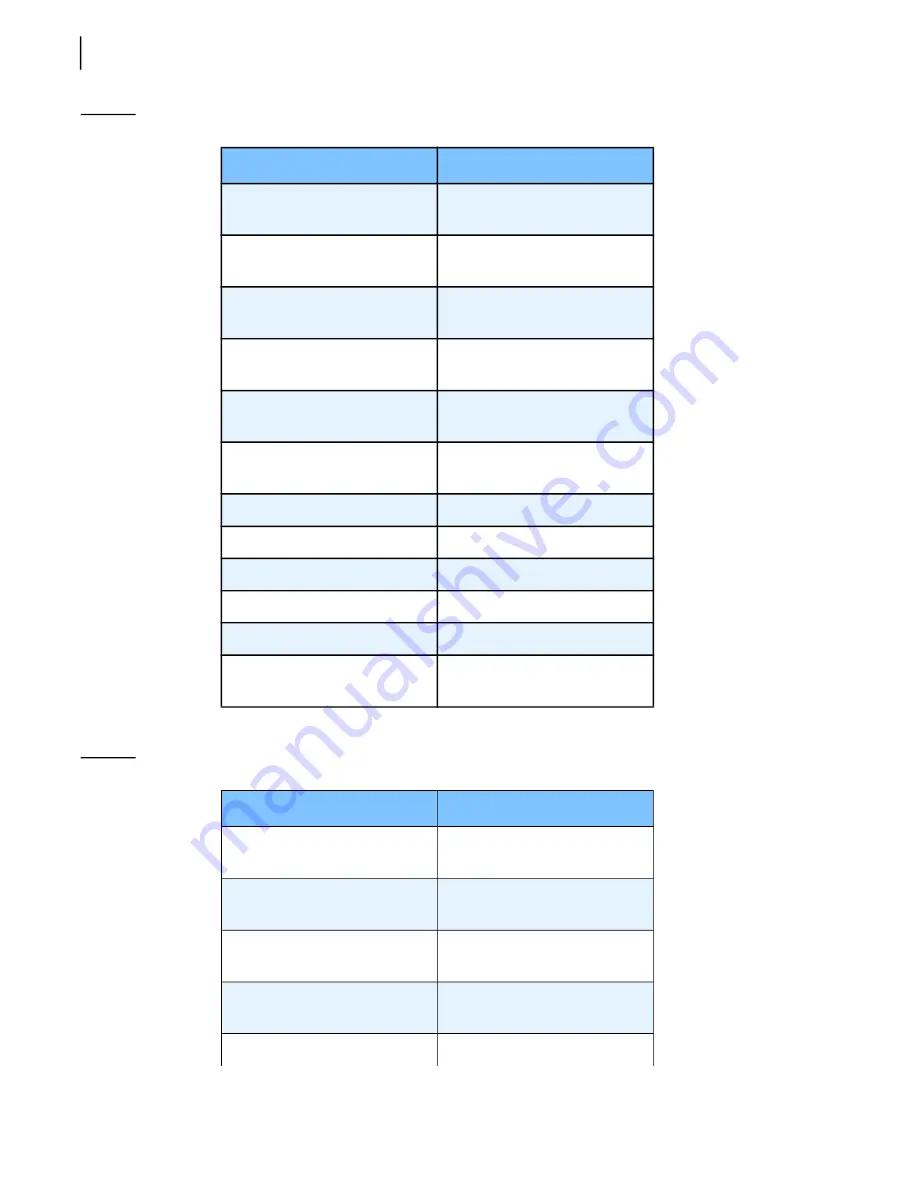
140
Multiplexing
Pump:SpeedUpON Switch ON Switch Must be OFF to Engage
Pump
Pump:TagAxle Down Switch
ON
Switch Must be OFF to Engage
Pump
Pump:TagAxle Up Switch ON Switch Must be OFF to Engage
Pump
Pump:TailGate Down Switch
ON
Switch Must be OFF to Engage
Pump
Pump:TailGate Up Switch ON Switch Must be OFF to Engage
Pump
Pump:Trans. Not OK
Refer to Maintenance
Personnel or Labrie
Plus
Roof:Pump NOT Started
Engage Pump
Service Oil Filter #1
Replace Oil Filter #1
Service Oil Filter #2
Replace Oil Filter #2
TailGate:Packer Not Retracted Retract Packer
TailGate:Pump NOT Started
Engage Pump
Wrong Driver Position
Move Driver Position Switch to
Opposite Position
Table 2
Error messages (cont’d)
Error Messages
Solution
Button Pack 12 is disconnected Refer to Maintenance
Personnel or Labrie
Plus
Button Pack 13 is disconnected Refer to Maintenance
Personnel or Labrie
Plus
Button Pack 14 is disconnected Refer to Maintenance
Personnel or Labrie
Plus
Button Pack 15 is disconnected Refer to Maintenance
Personnel or Labrie
Plus
CAN Error Level 1
Refer to Labrie
Plus
Table 1
Warning messages (cont’d)
Warning and Caution Messages
Solutions
Summary of Contents for FEATHERWEIGHT
Page 1: ...STARLIGHT SUPERDUTY MAINTENANCE MANUAL FEATHERWEIGHT ...
Page 2: ......
Page 3: ...STARLIGHT SUPERDUTY FEATHERWEIGHT MAINTENANCE MANUAL ...
Page 5: ......
Page 6: ......
Page 10: ...viii Table of Contents ...
Page 18: ...8 Introduction ...
Page 40: ...30 Safety ...
Page 46: ...36 Lubrication ...
Page 74: ...64 Electrical System ...
Page 90: ...80 Pneumatic System ...
Page 170: ...160 Multiplexing ...