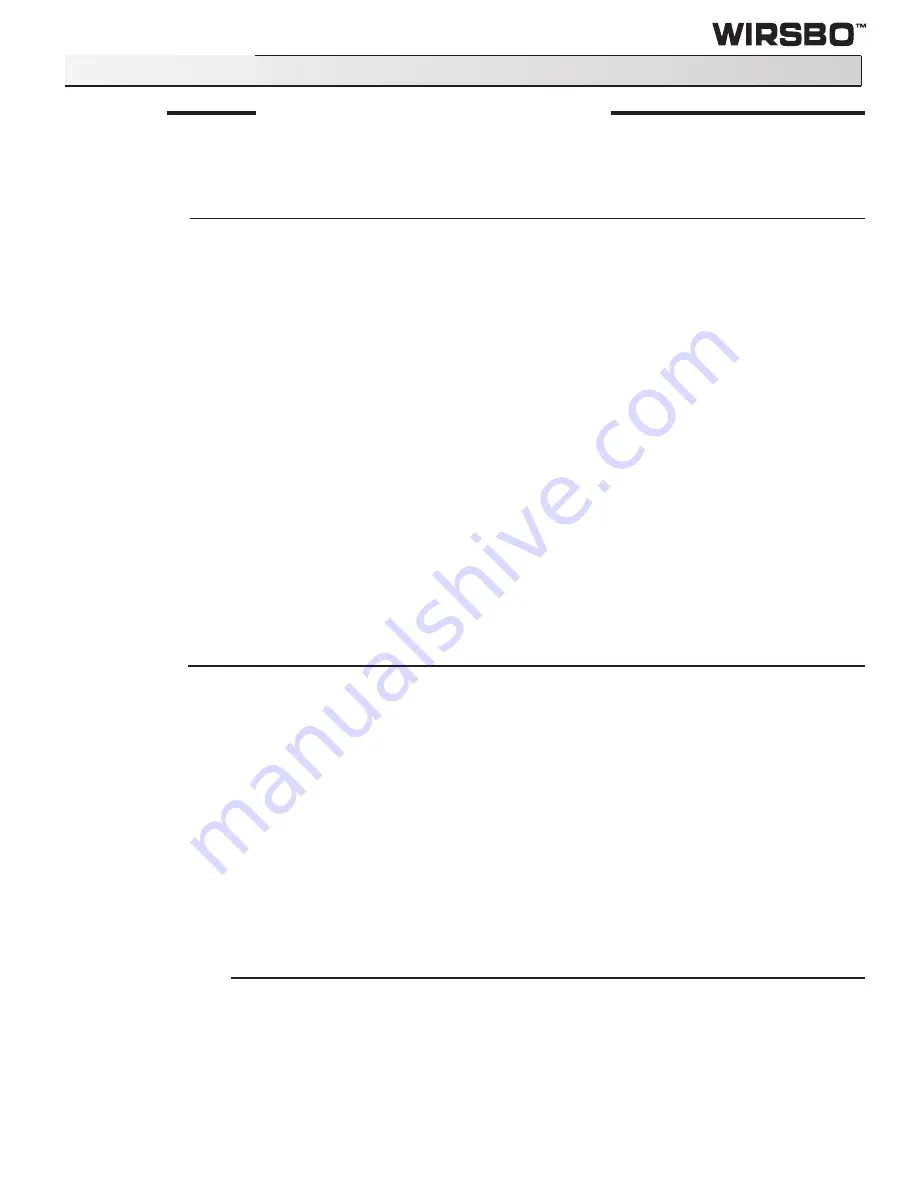
DuoMix Installation Handbook
19
Testing the Control
STEP SEVEN
OPERATIONAL TEST OF CONTROL FUNCTIONS
The Wirsbo DuoMix 201 has a test routine which is used to test the main control functions. The 201 continually checks the sensors and
displays an error message whenever a fault is found. See page 20 for the list of error messages. When the
Test button is pushed, the
WWSD display and the Minimum, Maximum, Melting, Idling, and CWCO pointers are turned off. The individual outputs and relays are
then tested in the following test sequence.
Test Sequence
Each step in the test sequence lasts 10 seconds. During the test routine, given a Mix demand is present, the test sequence can be
paused by pressing the
Test button. Once the test sequence is paused, the Test button can be pressed again to skip to the next step.
This can also be used to rapidly skip through the test sequence. To reach the desired step, repeatedly press and release the
Test
button until the appropriate device and indicator light turn on.
STEP 1 - The variable speed injection pump 1 (Var 1 Pmp) is ramped up to 100% over 10 seconds. If the mixing 1 section is not used
(i.e.
MODES 1 set to OFF) N/A is displayed and the pump is not operated.
STEP 2 - The variable speed injection pump 1 (Var 1 Pmp) is ramped down to 0% over 10 seconds. If the mixing 1 section is not used
(i.e.
MODES 1 set to OFF) N/A is displayed and the pump is not operated.
STEP 3 - The mixing 1 pump (Mix1 Pmp) is turned on for 10 seconds. If the mixing 1 section is not used (i.e.. MODES 1 set to OFF)
N/A is displayed and the pump is not operated.
STEP 4 - The variable speed injection pump 2 (Var 2 Pmp) is ramped up to 100% over 10 seconds. If the mixing 2 section is not used
(i.e.
MODES 2 set to OFF) N/A is displayed and the pump is not operated.
STEP 5 - The variable speed injection pump 2 (Var 2 Pmp) is ramped down to 0% over 10 seconds. If the mixing 2 section is not used
(i.e.
MODES 2 set to OFF) N/A is displayed and the pump is not operated.
STEP 6 - The mixing 2 pump (Mix2 Pmp) is turned on for 10 seconds. If the mixing 2 section is not used (i.e. MODES 2 set to OFF)
N/A is displayed and the pump is not operated.
STEP 7 - The Boiler Enable relay is turned on for 10 seconds.
Pointers "On"
Mix 1 Demand
• Mixing 1 section requires heat.
Mix 2 Demand
• Mixing 2 section requires heat.
Minimum
• The return temperature to the boiler is below the
Boil RET setting and the 201 is reducing the load in
order to increase the boiler temperature as fast as possible.
Maximum
• The supply temperature of mixing section 1 or 2 is approaching the
Max Sup setting and the 201 will not
increase the supply temperature any further.
Melting
• The control is in melting mode.
Idling
• The control is in Idling mode.
CWCO
• The control is in Cold Weather Cut Off and heat for snow melting is not provided, unless the slab is
already up to temperature.
MAX HEAT Function
The
MAX HEAT function provides maximum heat to the system by targeting the maximum supply temperature for each mixing section.
This function is useful during system start up, manual override, or testing during the summer. When the control is in
MAX HEAT and
a mixing demand in the mixing section 1 is present, the control turns on the mixing pump relay (
Mix1 Pmp), the variable speed pump
output (
Var1 Pmp) and Boiler Enable relay. The MAX HEAT function overrides the WWSD and the boiler minimum return temperature,
but it will not exceed the maximum supply setting. When a mixing demand in the mixing 2 section is present, the control operates
similarly as explained above. The speed of the injection pump(s) may be adjusted using the arrow keys to limit the amount of injection
desired. Once enabled, the
MAX HEAT function operates for 24 hours or until any of the Test, Menu, or Item buttons are pressed.
See next page for setup instructions.
Summary of Contents for DuoMix 201
Page 17: ......
Page 18: ...Display Menu Cont...
Page 22: ...DuoMix Installation Handbook 22...
Page 23: ...DuoMix Installation Handbook 23...
Page 24: ...DuoMix Installation Handbook 24...
Page 25: ...DuoMix Installation Handbook 25...
Page 30: ...DuoMix Installation Handbook 30...