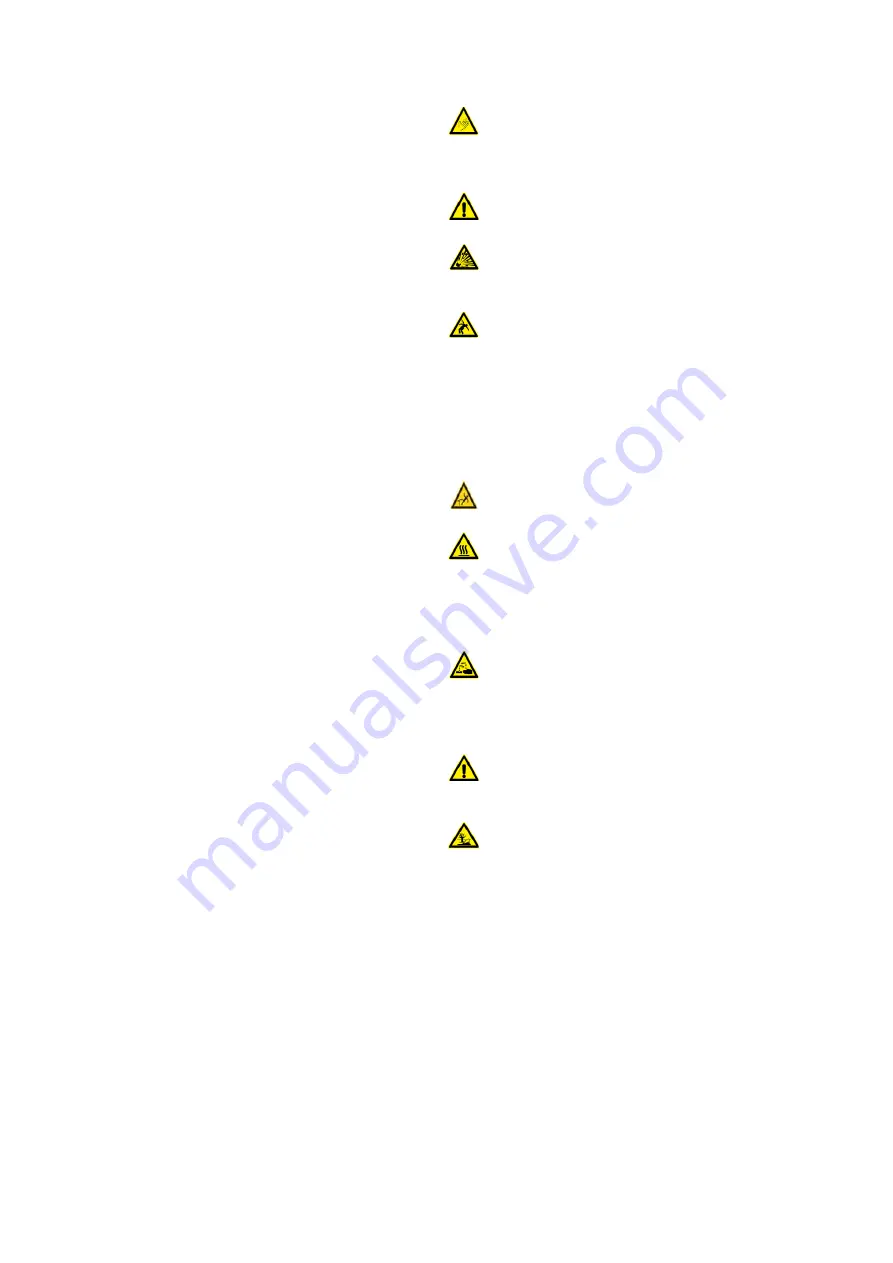
English
Installation and operating instructions Wilo-SiFire System
43
Yearly checks
To perform it maximum every 12 months
Test the efficiency of each pump when fully
loaded (with the connection between the test
pipes to the pump discharge) to control if values
??of pressure/flow correspond with those indi-
cated on the plate of the pump.
Consider any pressure losses in the supply pipes
and in the valves between the water source and
each control station.
Test a diesel engine start failure, then check that
an alarm in accordance with standards is working.
After this control, immediately restart the diesel
engine by using the manual startup procedures.
Check that the float valves in the storage tanks are
correctly working.
Check the strainers on the pump suction and
deposit tank of filtration accessories. Clean them
if necessary.
3-yearly checks
To perform it maximum every 3 years
After making drain of all tanks, check the outside
and inside to see if there is corrosion. If necessary,
all tanks must be painted or, protection against
corrosion must be applied again.
Examine all the water supply valves, alarm and
control valves. If necessary, replace them or main-
tain them.
10-yearly checks
To perform it maximum every 10 years
The inside of all water supplies should be cleaned
and examined. Tightness must be controlled.
Concerning the review process or replacement of
damaged parts of the entire system, which no
longer perfectly work, contact the Wilo helpdesk
or a specialised centre.
Refer to the detailed maintenance operations
indicated on manual attached to the unit.
Always replace the equipment with an original or
with identical characteristics certified spare part.
The Wilo denies any liability for damage caused by
an unskilled personnel intervention or when origi-
nal spare parts are replaced by other parts with
different characteristics.
9.5 Residual risks during facility management
WARNING! Risk of cut!
Sharp edges or any not protected threaded parts
entail the risk of getting cut. Take necessary
cautions to avoid injuries and use protective
equipment (wear specific gloves).
WARNING! Risk of impact injury!
Be careful of prominent parts and height. Wear
special protection clothing.
DANGER! Risk of fatal injury!
Do not exceed the nominal pressure limits for
the vessel of the jockey pump in order to avoid
possible explosions.
DANGER! Risk of electric shock!
The people dedicated to the connection of elec-
trical equipment and motors must have
obtained a certificate for this kind of work and
shall make the connection in accordance with
regulations and laws in force. They should
ensure that they have shutdown power before
performing any operation which provides the
possible contact with the electrical parts. Check
earth continuity. Avoid contact with water.
WARNING! Risk of Fall!
Take precautions to protect access to tanks or
wells. Wells must have closing cover.
WARNING! Risk of burn!
Take precautions to avoid contact with high
temperature parts of engine. Use protections
for parts of the engine and the exhaust pipe. Top
up fuel in the tank when the diesel engine is
cold. During refilling, do not drop fuel on hot
parts of diesel engine. Wear special gloves.
WARNING! Risk of irritation!
During refilling and level controls, avoid spillage
of battery acid solution could cause irritations or
material damages. Do not approach refilling area
with eyes. Use special protections to avoid con-
tact.
DANGER! Risk of fatal injury!
Avoid turning on the diesel pumps if exhaust
smoke pipes were not connected towards out-
side the room.
CAUTION! Risk of environmental pollution!
During controls and refilling, avoid dumping of
oil from the engine or diesel fuel. Use appropri-
ate protections and implemented the necessary
precautions.
Summary of Contents for SiFire
Page 2: ...Fig 1 Fig 2a A 2 2 E B C D...
Page 3: ...Fig 2b Fig 3 21 25 26 13 11 12 19 15 22 27 20 24 23 2 1 14 4 16 7 5 6 10 18 17 9 9 10 8 3...
Page 4: ...Fig 4 Fig 5...
Page 5: ...Fig 6a 3 5 D D 4 D 2 3 C min max 1 8 m s Fig 6b min 3 5 D D 4 D max 2 m 2 3 C max 1 8 m s...
Page 6: ...Fig 7 Fig 8 max 3 2 m min A B C D 2 4 5 6 3 8 7 1...
Page 7: ...Fig 9a Fig 9b A B C D 800 800 800...
Page 8: ...Fig 1a Fig 9a variant Fig 9b variant A B C D 800 800 800...
Page 9: ...Fig 10 Fig 11 1 2 1 2 1...
Page 10: ......
Page 34: ......
Page 35: ......