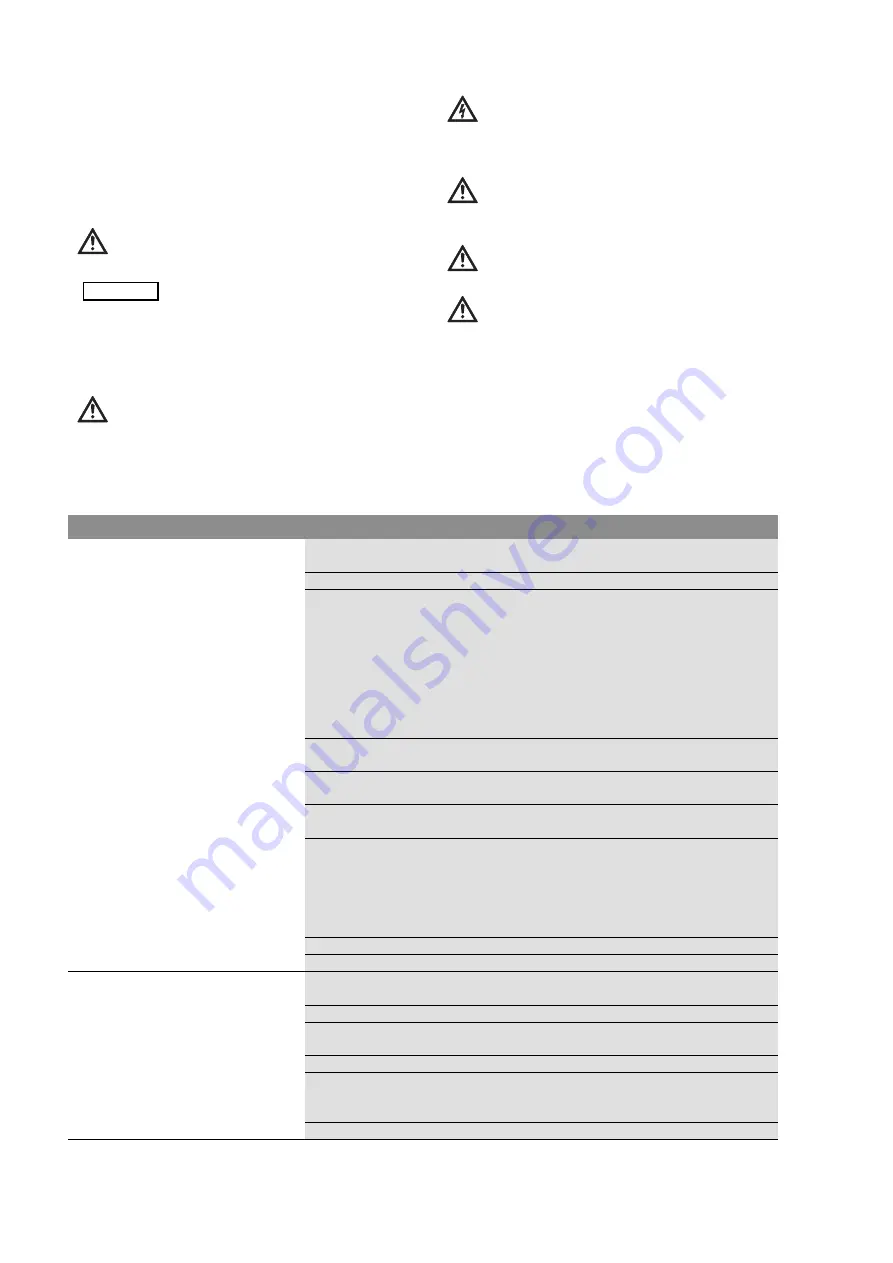
English
22
Wilo AG 09/2005
Destroy all the gaskets after dismantling, replace
them when reassembling.
It is recommended that bearings are not reused
after any removal from the shaft.
After serving during two years, replace the gland
packing
.
6.5
Disassembly
Refer to section 1.6, Safety, and section 6 Main-
tenance, before dismantling the pump.
Repair of the pump
If the pump presents abnormalities or a persis-
tent malfunction, contact immediately the
After-sales Service.
According to the After-sales Service instructions,
disassembly will be limited to the dismantling of
the pump.
Disconnect the unit from power
• Close the inlet valve (if fitted) and outlet valve.
• Wait for the moment when the pump casing is
cooled and at ambient temperature.
Drain pump
Dismantle inlet and outlet pipeworks as well as
all pipeworks.
REMOVE PUMP TAKING INTO ACCOUNT SAFETY
(§ 1) AND HANDLING (§ 2.2) PROCEDURES.
ANY DISASSEMBLY, REPAIR OR REASSEMBLY
WILL BE CARRIED OUT UNDER FLOWSERVE'
RESPONSABILITY, EITHER DIRECTLY BY THE
AFTER-SALES SERVICE OR BY OTHER FLOW-
SERVE-AGENTS WHO WILL GET THE REQUIRED
INSTRUCTIONS AND APPROVALS. THIS IS THE
CASE OF AUTHORIZED REPAIRERS WHOSE
ADDRESSES AND TELEPHONE NUMBERS WILL BE
GIVEN ON REQUEST.
7 Faults, Causes and Remedies
Before dismantling the pump for over-
haul, ensure genuine replacement parts
are available. Refer to sectional dra-
wings for part numbers and identifica-
tion.
CAUTION!
Trouble
Possible Causes
Solutions
Insuffcient flowrate
Pump or suction pipe not completely
filled
Check and complete filling
Air bubbles in pipes
Check and desecrate the pipes
Suction level too low
• Check: the available NPSH > the
required NPSH
• Reduce geometrical suction lift
• Reduce head losses in pipes and in fit-
tings (diameter increase and appropri-
ate fitting positions)
• Check valves and strainers
• Check the immersion head of the suc-
tion valve
Wrong rotation
Reverse 2 phases on motor terminal
boxes
The motor is running on 2 phases only
Check and control the motor electrical
power supply
Motor running too low
Check the connection in the terminal
box according to the voltage
Total manometric head system higher
than pump differential head
• Check the discharge head
• Check the head losses in discharge
pipes (partly closed valve, foreign par-
ticles, back pressure too high)
• Modify the installation or change the
pump set
Pipes (valves, filter...)
Control, dismantle and clean
Worn wear-ring surfaces
Foresee pump mending
Irregular pump running
Pump or suction pipe not completely
filled
Check and complete filling
Air bubbles in pipes
Check and desecrate the pipes
The motor is running on 2 phases only
Check and control the motor electrical
power supply
Seizure, jamming
CONSULT US
Excessive strains on flanges
Check the flange connections and elimi-
nate strains (pipe positioning or elastic
sleeves mounting)
Defective motor bearings
CONSULT US