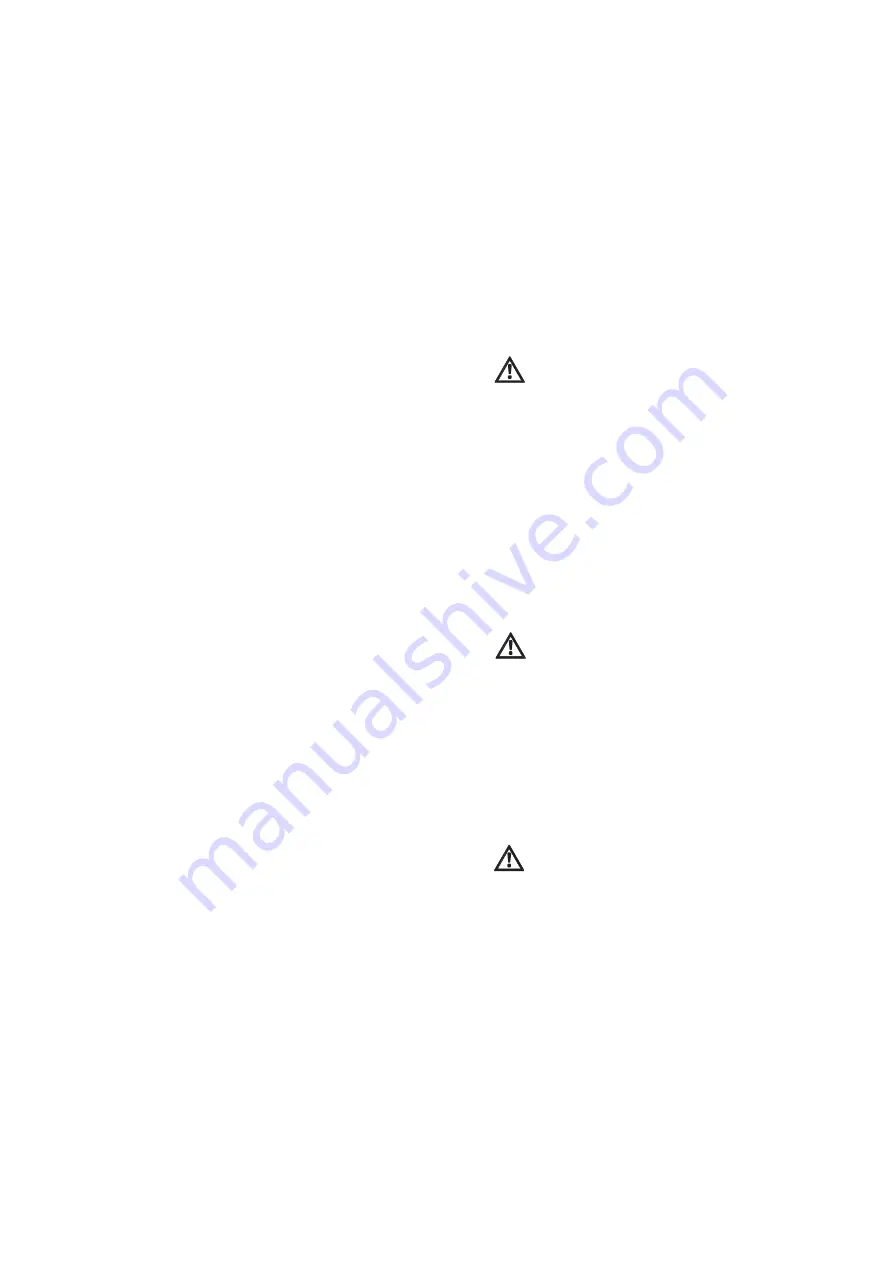
Installation and operating instructions WILO Mather and Platt
–
MISO / PISO Pumps
20
8.3.2 Pre-starting checks (Refer Check List in
Annexture-2)
•
Check that the inlet isolating valve is open, and that the
delivery valve is closed.
•
Check that there is no blockage in the strainer at the end
of the suction line.
•
Check for free rotation of the unit when coupled.
•
Check that suction and delivery pressure gauges are
connected. Test and make available any alarm, signals,
interlock systems and any of the protective devices
incorporated in the auxiliary and main pumping control
system.
•
Ensure that all electrical checks on motor, relay setting
in panel etc. have been carried out in accordance with
the instructions of motor manufacturer.
•
Ensure that stuffing box sealing water seal connection is
provided as shown in GA Drawing.
8.3.3 Normal starting and running checks
•
When all the foregoing pre-start checks are satisfactory,
start the pump and check the direction of rotation
(indicated by a direction arrow on the pump casing)
otherwise stop the pump immediately for correction of
direction of rotation. Then run the pump at its rated
speed.
•
Check the ammeter reading to ensure that the motor is
not being overloaded.
•
If applicable, ensure that the stuffing box is not
overheating and that there is slight leakage from the
gland (about 1 -2 drop per second). There may be at first
a tendency for the stuffing boxes to run warm because
of the high viscosity lubricant in the packing. During the
first few minutes of running with new packing, a small
quantity of very viscous fluid will be extruded, but the
flow should reduce when the packing has settled down.
•
Check the mechanical seal for leak. In the start phase
(and also after downtimes) slight leakage can be
expected. Visual leakage checks are however required
from time to time. Distinctly visible leakage will require
an exchange of the seal. WILO Mather and Platt offers a
repair set containing all parts required for an exchange.
•
Check that the bearing is not overheating. Bearings will
norm
ally run at a temperature of 30˚C
-
35˚C above
ambient temperature. The ideal running temperature of
bearings is 40˚C to 60˚C for ball bearings and 40˚C to
55˚C for bush bearings. The temperature should never
exceed 82˚C for ball bearings and 75˚C for bush
bearings. If the bearings are overheating its cause should
be investigated immediately.
•
If the foregoing checks are satisfactory, open the
delivery valve slowly and bring the pump gradually up to
its rated parameters indicated in the data sheet/name
plate and based on pressure gauge and ammeter
readings. Unless the pump is fitted with a special leak-
off device, it should not be run for a long period against
a closed delivery valve. Check that the driving unit is not
being overloaded during valve opening. Overloading
may occur if the pump is discharging into an empty
system. If the pumping unit fails to generate at least its
rated delivery pressure it must be stopped immediately,
the cause ascertained,
•
Check vibration of pump set and ensure that vibration
level is within limits specified. Check that noise level is
within stipulated limits.
•
The pumps may be run for 8 hours trial operation and all the
parameters like delivery pressure, current, bearing
temperature, etc. Be recorded periodically.
•
Make the following checks at regular intervals. It is
recommended that they be made at every change of shift.
•
Check the suction and discharge pressure gauge for normal
operating pressure, if there is significant drop in the suction
or discharge pressure the pump may have lost its supply. In
the event of this fault occurring, the pump must be stopped
immediately, and the cause of liquid loss eliminated.
•
Check the mechanical seal or stuffing box assembly for
overheating.
8.3.4 Sealing system
Gland packing
CAUTION! Risk of damaging the pump!
If the gland plate is too tight, the packing stuff will be
immediately damage.
At the beginning of the operation, the leak at the gland
packing should be important. It should reduce progressively
after several hours by a balanced and reasonable tightening
the gland plate. The gland packing must operate without
excessive temperature. The correct setting of the gland
packing let a permanent leak around 1 or 2 drops per
seconds.
If this leak is too much and cannot be adjusted with the
gland plate, the packing stuffing’s are worn and must be
replaced.
Mechanical seal
CAUTION! Risk of damaging the pump!
A mechanical seal must never operate without fluid and
lubrication even for a short period of time.
ensure that the pump is completely full of water and vented
before starting the pump. Small leakages can occur during
the period of running-in, they should disappear after several
hours of operation. If the leakages don’t stop, shut down the
pump disassemble the mechanical seal and control their
condition.
8.3.5 Normal shutdown
WARNING! Risk of Burns!
If the fluid temperature and system pressure is high, close
the isolation valves upstream and downstream of the
pump. Initially let the pump cool.
•
Close the delivery valve to reduce the load on the driving
unit.
•
Stop the driver of the pump.
•
When the pump has come to rest, close the suction-
isolating valve.
•
Isolate any ancillary supplies.
8.3.6 Emergency Shutdown
In the event of any malfunction of the equipment, switch off
the pump set. When the pump has come to rest, close the
suction & discharge valves, isolate the driving unit power
supply & rectify the fault.