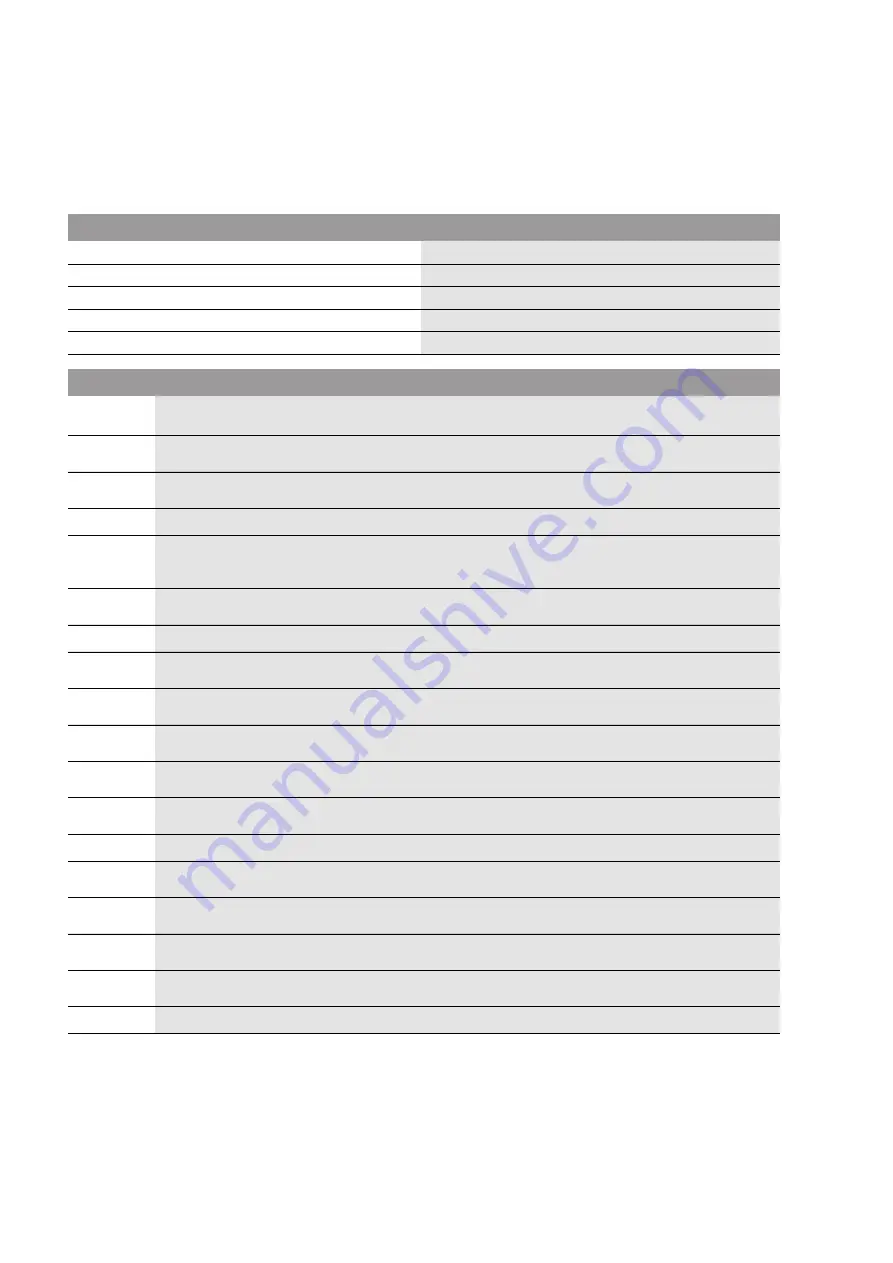
English
20
WILO SE 10/2010
10 Faults, causes and remedies
Have faults remedied only by qualified personnel.
Observe the safety instructions in 9 Maintenance.
• Observe the installation and operating instructions for the unit, switchgear and accesso-
ries!
• If the operating fault is unable to be remedied, please consult a specialist technician, Wilo
service or the closest Wilo representative.
1)
To remedy faults on parts under pressure, depressurise them first (vent the non-return valve and drain the tank,
if necessary with diaphragm hand pump).
2)
Further enquiry required
Faults
Code: cause and remedy
Pump is not pumping
1, 3, 5, 6, 7, 8, 9, 10, 11, 12, 15, 16, 17, 18
Volume flow too low
1, 2, 3, 4, 5, 7, 8, 11, 12, 13
Current consumption too high
1, 2, 3, 4, 5, 7, 13
Delivery head too small
1, 2, 3, 4, 5, 8, 11, 12, 13, 16, 18
Pump running roughly/loud noise
1, 2, 3, 9, 12, 13, 14, 16
Cause
Remedy
1)
1
Pump inlet or impeller clogged
• Remove deposits from the pump and/or tank
2
Incorrect direction of rotation
• Swap two phases of the current feed
3
Wear to inner parts (impeller, bearing)
• Replace worn parts
4
Operating voltage too low
5
Running on two phases (only with 3~ version)
• Replace defective fuse
• Check line connections
6
Motor not running, since no voltage available
• Check electrical installation
7
Motor winding or electrical line defective
2)
8
Non-return valve clogged
• Clean non-return valve
9
Excess water level drop in the tank
• Check level sensor with switching level
10
Level sensor faulty
• Check level sensor
11
Slide valve in pressure pipe not or insufficiently open
• Open slide valve completely
12
Impermissible amount of air or gas in fluid
• Check inlet for air bubbles in tank; check deactivation level.
13
Radial bearing in motor defective
2)
14
Unit-related vibrations
• Check piping for flexible connection
15
Temperature monitor for winding monitoring switched off due to excessive winding temperature
• Motor switches on again automatically after cooling down.
16
Pump ventilation clogged
• Clean ventilation line
17
Thermal overcurrent monitor triggered
• Reset overcurrent monitor in switchgear.
18
Geodesic delivery head too high
2)