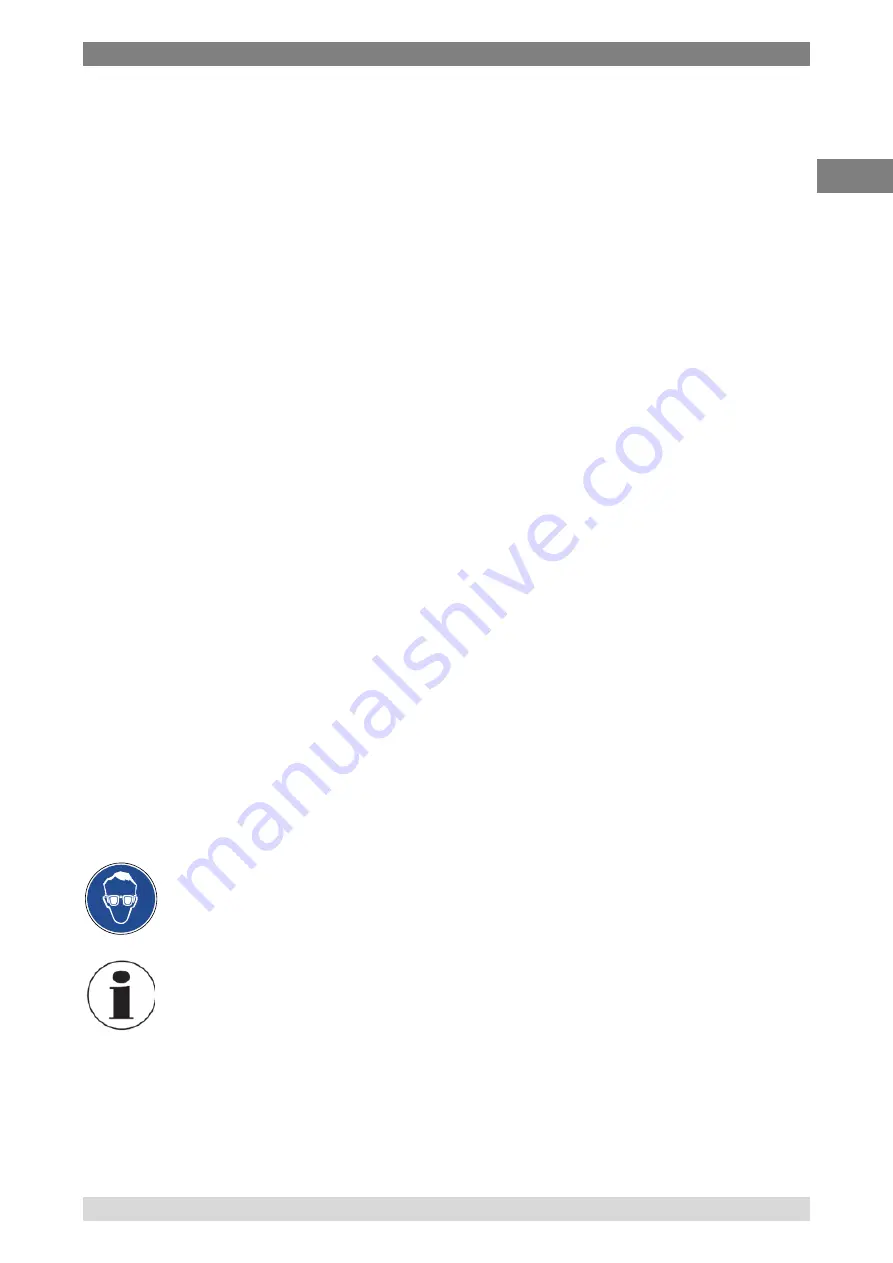
7. Maintenance, cleaning and servicing
WIKA Operating Instruction, CPP4000-X
27
EN
14
15
54
60
.0
08
/20
16
GB
7.2.6
Hub assembly
1.
Unscrew the ram from the spindle. NOTE: left hand thread.
2.
Unscrew the spokes from the hub.
3.
Knock out the spring pin (1), found at the bottom of one of the tapped spoke holes in the hub,
using a punch 6 mm dia. Pull off hub.
4.
The hub locating plate and thrust bearing can now be removed from the spindle.
5.
If the flanged bush (2) is to be renewed, it should be pressed out of the locating plate and a new
one pressed in squarely.
6.
The thrust bearing (3) is renewed as a complete assembly.
7.
The nut, pin and spindle sub-assembly (4) can only be replaced as a matched pair. Unscrew the
nut from the ram, gripping in a soft jaw vice and screw in the new nut.
8.
Assemble the thrust bearing, locating plate and hub on to the spindle, lubricating with
molybdenum disulphide grease.
9.
Clamp these items together to eliminate end play and re-assemble spring pin. If using new
spindle drill through 6.3 mm diameter to fit spring pin (1).
10.
Lubricate the thread with molybdenum disulphide grease and screw into ram nut.
7.3
Cleaning
7.3.1
Cleaning the unit and checking the liquid levels.
Oil operation
Keep the system clean and free from spilt oil. Wipe out the oil cups under the gauge stands as
necessary. Do not use any cleansing solvents as they may damage the seals.
Ensure that the reservoir contains sufficient liquid to carry out any calibrations required. If necessary
top up the reservoir with the same liquid that is already being used. Do not mix various types or
brands of liquid in the pressure balance.
If the oil in the test pump becomes dirty, attach a drain to the test connection and use the spindle
pump to flush through clean oil. (An angle connection is suitable). The spindle pump should be
turned fully clockwise before starting.
Wear safety goggles!
Protect eyes from flying particles and liquid splashes.
For information on returning the instrument see chapter 8.1 “Return”.
.