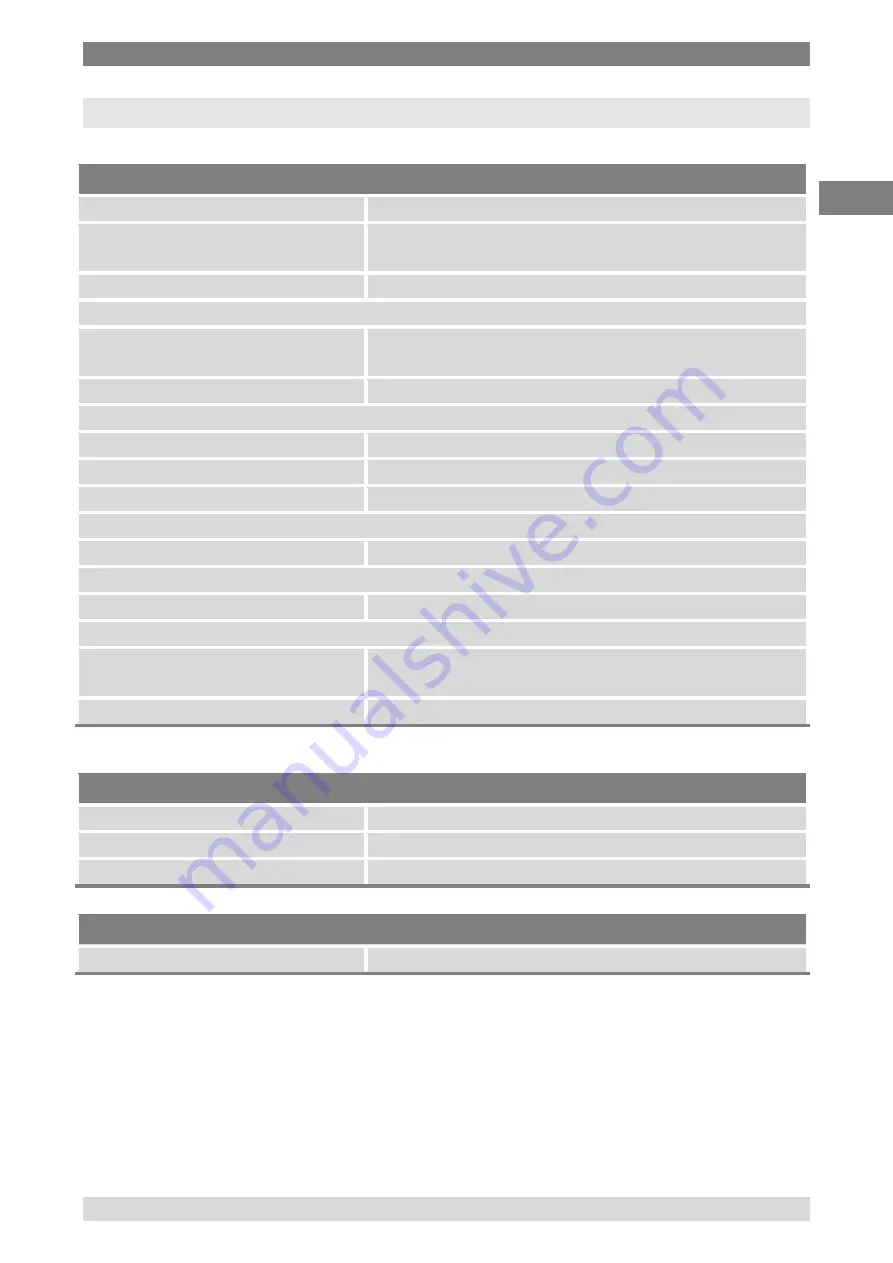
10. Specifications
WIKA Operating Instruction, CPP4000-X
29
EN
14
15
54
60
.0
08
/20
16
GB
9.
Specifications
Specifications
Model CPP4000-X
Pressure range
0 ... 4,000 bar
Pressure transmission medium
Hydraulic fluid based on VG22 mineral oil or Sebacate oil
(optional)
Reservoir
170 cm³
Pressure connections
Test connection
2 x G ½ B female thread union nut with metal cone;
equipped with two thread adapters M16 x 1.5 as standard
Distance between test connections
290 mm
Piston of spindle pump
Piston diameter, low-pressure piston 31.2 mm
Piston diameter, high-pressure piston 6.35 mm
Displacement
approx. 5 cm³
Material
Wetted parts
Austenitic stainless steel, high-tensile brass, nitrile rubber
Permissible ambient conditions
Operating temperature
0 ... 40 °C
Instrument base
Dimensions
401 x 397 x 155 mm (W x D x H), for details, see technical
drawings
Weight
13.5 kg
1) Other pressure transmission media on request.
Storage case (option)
Material
Wood
Dimensions
664 x 614 x 380 mm (W x D x H)
Weight
8.5 kg
CE conformity
Pressure equipment directive
97/23/EC (PS > 1,000 bar; module A, pressure accessory)
Approvals and certificates, see website
For further specifications see WIKA data sheet CT 91.09 and the order documentation.