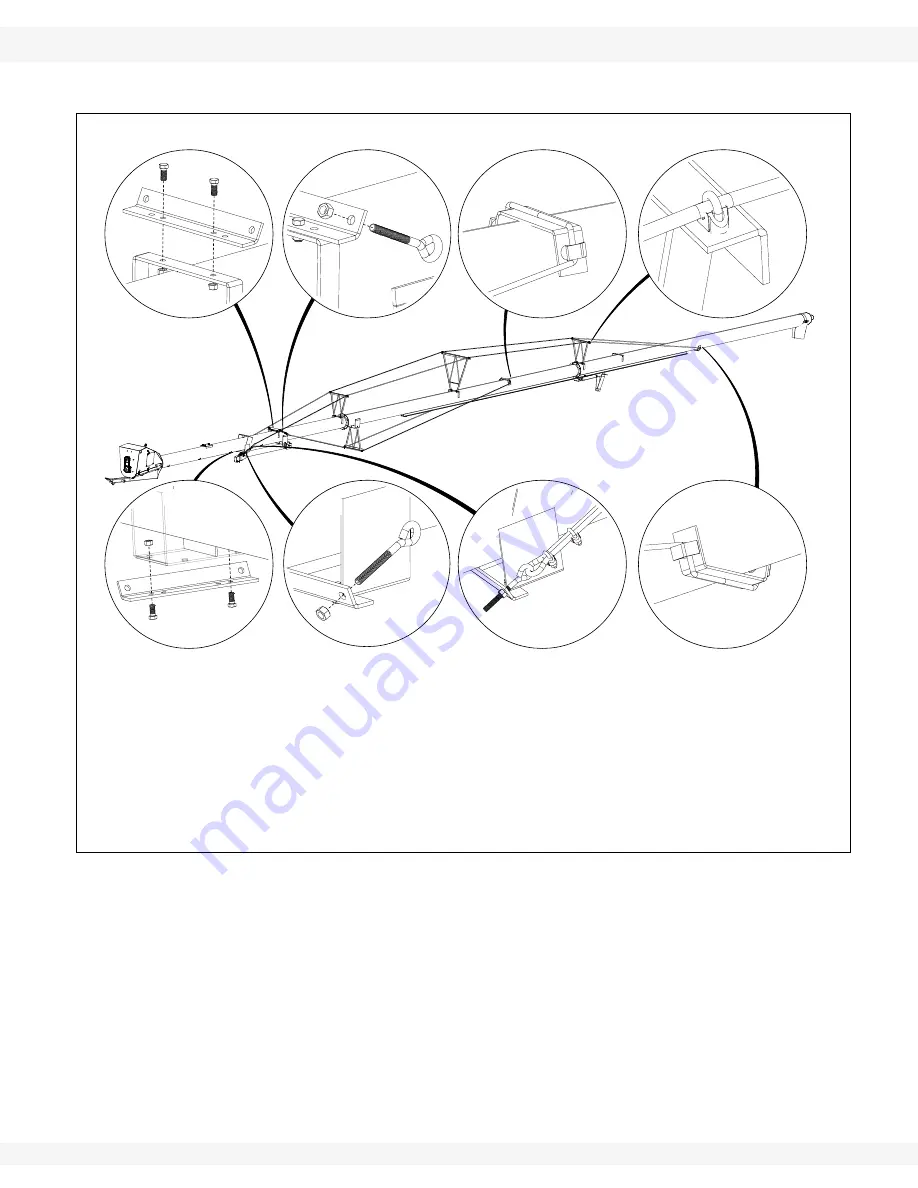
3. A
SSEMBLY
W
ESTFIELD
- MKX100-S
ERIES
G
RAIN
A
UGERS
MKX100-53/63/73/83
38
30908 R3
Figure 3.24 Installing Truss Cables
1: 7/16” X 1” BOLT [19542]
2: 7/16” LOCKNUT [19598]
3: TRUSS CABLE BRACKET [18032]
4: CABLE CLAMP (5/16” FOR MKX100-53/63/73 [19333], 3/8” FOR MKX100-83 [18990])
5: 1/2” EYEBOLT[19331]
6: TOP CABLE
7: BOTTOM CABLE
NOTE: THE CONFIGURATION SHOWN HERE (TRUSSING ABOVE AND BENEATH THE TUBE)
APPLIES ONLY TO MKX100-73/83, BUT ALL OTHER DETAILS ARE THE SAME ACROSS ALL MODELS.
Summary of Contents for MKX100 SERIES
Page 2: ......
Page 4: ...WESTFIELD MKX100 SERIES GRAIN AUGERS MKX100 53 63 73 83 4 30908 R3 ...
Page 6: ...1 INTRODUCTION WESTFIELD MKX100 SERIES GRAIN AUGERS MKX100 53 63 73 83 6 30908 R3 ...
Page 16: ...2 SAFETY WESTFIELD MKX100 SERIES GRAIN AUGERS MKX100 53 63 73 83 16 30908 R3 ...
Page 62: ...3 ASSEMBLY WESTFIELD MKX100 SERIES GRAIN AUGERS MKX100 53 63 73 83 62 30908 R3 ...