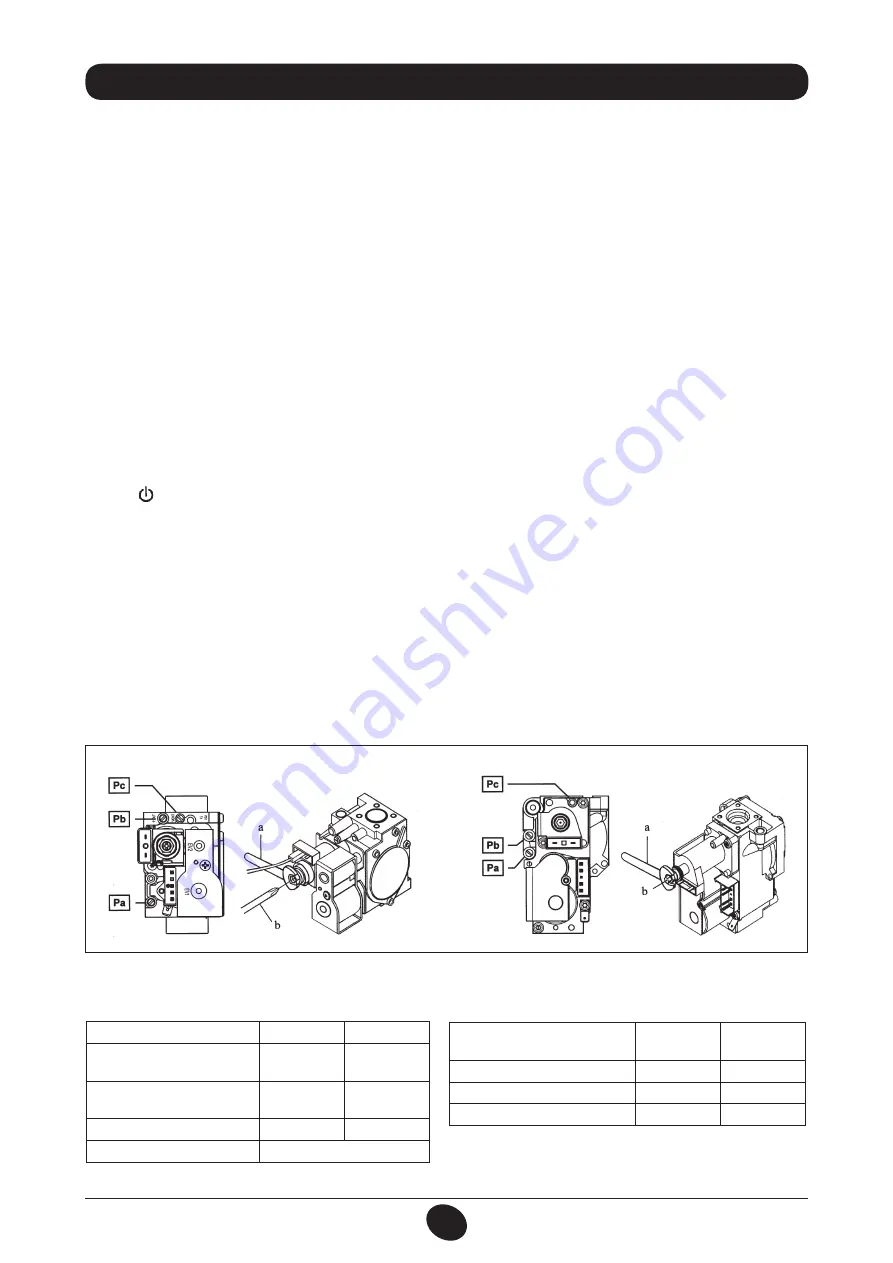
44
925.476.4 - EN
INSTRUCTIONS PERTAINING TO THE INSTALLER
A Qualified Service Engineer may adapt this boiler to operate with natural gas (
G. 20
) or with liquid gas (
G. 31
).
The procedure for calibrating the pressure regulator may vary according to the type of gas valve fitted (HONEY WELL or
SIT; see figure 11). Carry out the following ope rations in the given sequence:
A) Substitute the main burner injectors
• carefully pull the main burner off its seat;
• substitute the main burner injectors and make sure you tighten them to avoid leakage. The injectors diameters are
specified in table 1.
B) Change the modulator voltage
• setting
F02
parameter according to the gas used as described in section 20.
C) Pressure adjusting device setting
• connect the positive pressure test point of a differential (possibly water-operated) manometer to the gas valve pressure
test point (
Pb
) (Figure 11); connect, for sealed chamber models only, the negative pressure test point of the manometer
to a
“T”
fitting in order to join the boiler adjusting outlet, the gas valve adjusting outlet (
Pc
) and the manometer. (The
same measurement can be carried out by connecting the manometer to the pressure test point (
Pb
) after removing the
sealed chamber front panel);
If you measure the pressure of burners in a different way you may obtain an altered result in that the low pressure created
in the sealed chamber by the fan would not be taken into account.
Adjustment to nominal heat output
• open the gas tap;
• press
button (figure 1) and set the boiler in winter mode (section 3.2);
• open a hot water tap to reach a minimum 10 l/min flow rate or ensure that maximum heating requirements are set;
• remove the modulator cover;
• adjust the tube brass screw (
a
) Fig. 11 to obtain the pressure settings shown in table 1;
• check that boiler feeding dynamic pressure, as measured at the inlet gas valve pressure test point (Pa) (Figure 11) is
correct (
37 mbar
for propane gas
G.31
,
20 mbar
for natural
gas G20
);
Adjustment to reduced heat output
• disconnect the modulator feeding cable and unscrew the (
b
) Fig. 11 screw to reach the pressure setting corresponding
to reduced heat output (see table 1);
• connect the cable again;
• fit the modulator cover and seal.
Final checks
• apply the additional dataplate, specifying the type of gas and settings applied.
18. GAS CHANGE MODALITIES
Figure 11
SIT valve mod. SIGMA 845
Honeywell valve mod. VK 4105 M
0904_0701
Table of burner pressures - heat output - burner injectors
Gas used
G20
G31
Burner pressure (mbar*)
MINIMUM HEAT OUTPUT
2,0
4,4
Burner pressure (mbar*)
MAXIMUM HEAT OUTPUT
10,2
21,8
Injector diameter (mm)
1,18
0,77
no. of injectors
15
Table 1
Consumption table
Consumption 15 °C -
1013 mbar
G20
G31
Maximum heat output
2,62 m
3
/h
1,92 kg/h
Minimum heat output
1,12 m
3
/h
0,92 kg/h
p.c.i.
34,02 MJ/m
3
46,30 MJ/kg
Table 2
Summary of Contents for star master 240 Fi
Page 83: ...83 925 476 4 RU 3 2 2 1 25 3 4 0801_0201 CG_2015...
Page 84: ...84 925 476 4 RU 4 1 C C ECO COMFORT ECO P eco COMFORT a PM12 0 20 3 2 3 1 0603_1301 2 4 2...
Page 85: ...85 925 476 4 RU 5 OFF OFF 3 2 OFF 6 7 LPG 5 C 30 C 8 3 0 7 1 5 OFF 3 2 3 0503_2405...
Page 91: ...91 925 476 4 RU 9 9 0904_1501 9a 9b 0904_1508 0904_1509...
Page 104: ...104 925 476 4 RU 32 NTC C M N R G V B V CG_1741 0904_1507 26...
Page 106: ...106 925 476 4 RU...
Page 107: ...107 925 476 4 RU...