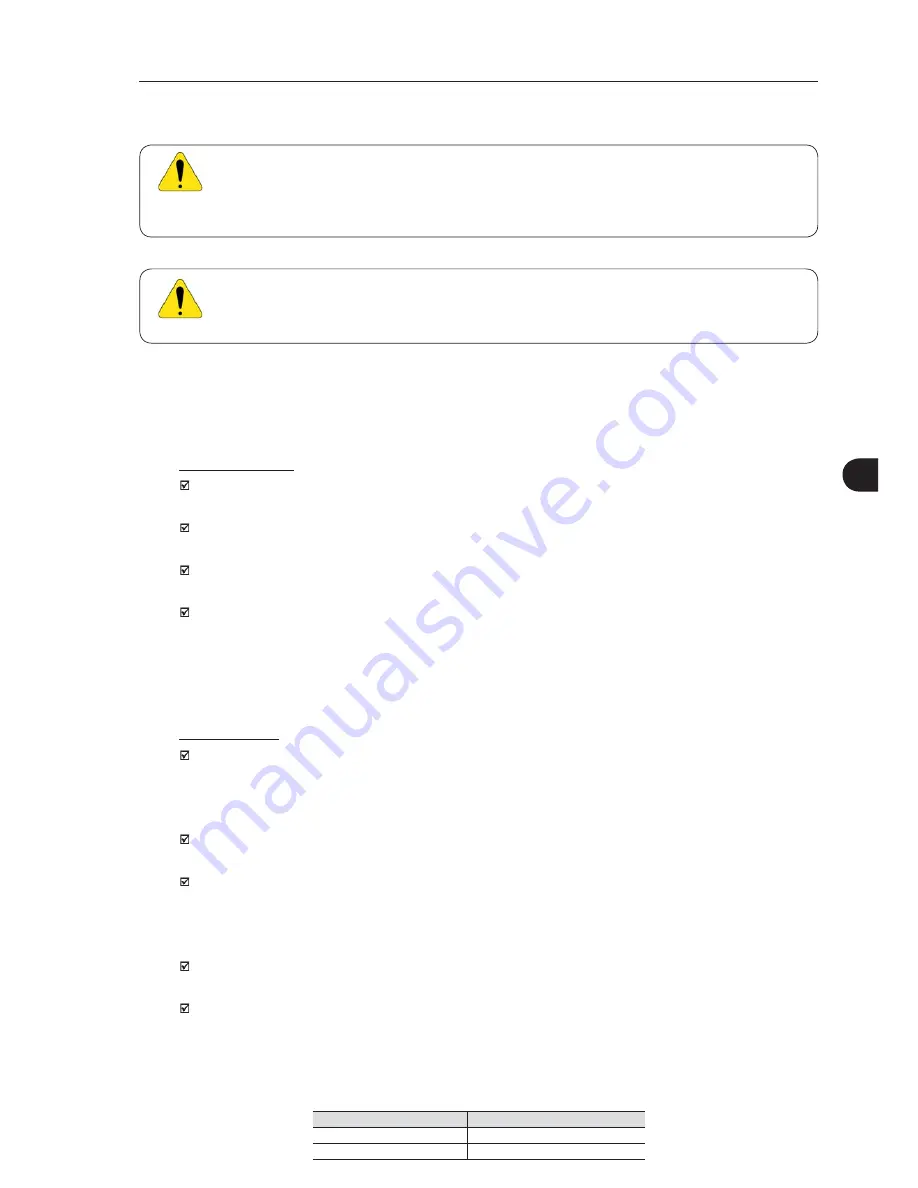
Installation and Connection
3-17
3
3.2.3.3 Output Connections
ATTENTION!
The inverter has an electronic motor overload protection that shall be adjusted according to the
driven motor. When several motors are connected to the same inverter, install individual overload
relays for each motor.
ATTENTION!
If a disconnect switch or a contactor is installed between the inverter and the motor, never operate
them with a spinning motor or with voltage at the inverter output.
The characteristics of the cable used for the inverter and motor interconnection, as well as the physical location
are extremely important to avoid electromagnetic interference in other equipment and to not affect the life cycle
of motor windings and motor bearings controlled by inverters.
Recommendations for the motor cables:
Unshielded Cables:
Can be used when it is not necessary to meet the European directive of electromagnetic compatibility
(89/336/EEC), unless the RFI filters be used as presented in the table 3.9 and section 3.3.1.
Keep motor cables away from other cables (signal cables, sensor cables, control cables, etc.), according to
table 3.4.
The emission of the cables may be reduced by installing them inside a metal conduit, which shall be grounded
at both ends.
Connect a fourth cable between the motor ground and the inverter ground.
Note:
The magnetic field created by the current circulation in these cables may induce current in close metal
pieces, heat them, and cause additional electrical losses. Therefore, keep the 3 (three) cables (U, V, W)
always together.
Shielded Cables:
Are mandatory when the electromagnetic compatibility directive (89/336/EEC) shall be met, as defined by
the standard EN 61800-3 “Adjustable Speed Electrical Power Drive Systems”, unless the RFI filters be used
as presented in the table 3.9 and section 3.3.1. These cables act mainly by reducing the irradiated emission
in the radio-frequency range.
Are mandatory when RFI filters, internally or externally mounted, are installed at the inverter input, unless
the RFI filters be used as presented in the table 3.9 and section 3.3.1.
In reference to the type and details of installation, follow the recommendations of IEC 60034-25 “Guide
for Design and Performance of Cage Induction Motors Specifically Designed for Converter Supply” – refer
to a summary in figure 3.13. Refer to the standard for further details and eventual modifications related to
new revisions.
Keep motor cables away from other cables (signal cables, sensor cables, control cables, etc.), according to
table 3.4.
The grounding system shall be well interconnected among the several installation locations such as the
grounding points of the motor and the inverter. Voltage difference or impedance between the several points
may cause the circulation of leakage currents among the equipment connected to the ground, resulting in
electromagnetic interference problems.
Table 3.4
0LQLPXPVHSDUDWLRQGLVWDQFHEHWZHHQPRWRUFDEOHVDQGDOORWKHUFDEOHV
Cable length
Minimum separation distance
PIW
FPLQ
> 30 m (100 ft)
FPLQ