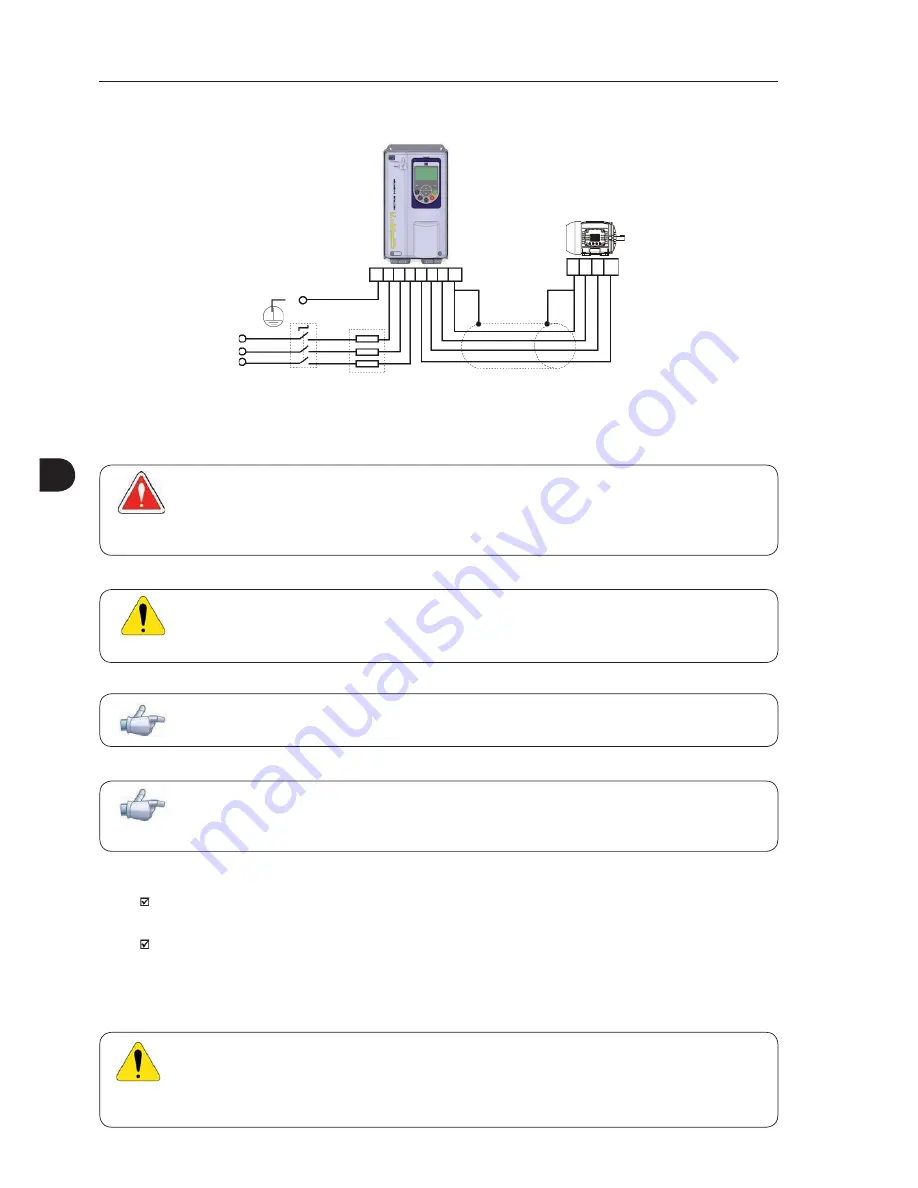
Installation and Connection
3-12
3
3.2.3.1 Input Connections
DANGER!
Provide a disconnect device for the input power supply of the inverter.
This device shall disconnect the input power supply for the inverter when needed (for instance, during
servicing).
ATTENTION!
The power supply that feeds the inverter shall have a grounded neutral. In case of IT networks, follow
the instructions described in item 3.2.3.1.1.
NOTE!
The input power supply voltage shall be compatible with the inverter rated voltage.
NOTE!
Power factor correction capacitors are not needed at the inverter input (R, S, T) and shall not be
installed at the output of the inverter (U, V, W).
AC power supply considerations
The CFW-11 inverters are suitable for use on a circuit capable of deliviering up to a maximum of 100.000
A
rms
symmetrical (240 V / 480 V).
If the CFW-11 inverters are installed in a circuit capable of delivering more than100.000 A
rms
symmetrical,
it is required to install adequate protection devices such as fuses or circuit breakers.
3.2.3.1.1 IT Networks
ATTENTION!
Do not use inverters with internal RFI filters in IT networks (neutral is not grounded or grounding
provided by a high ohm value resistor) or in grounded delta networks (“delta corner earth”), because
these type of networks damage the inverter filter capacitors.
Figure 3.10
3RZHUDQGJURXQGLQJFRQQHFWLRQV
3.2.3 Power Connections
Shielding
PE
Disconnect
Switch
Fuses
R
S
T
Power
Supply
PE W V U
PE R S T U V W PE