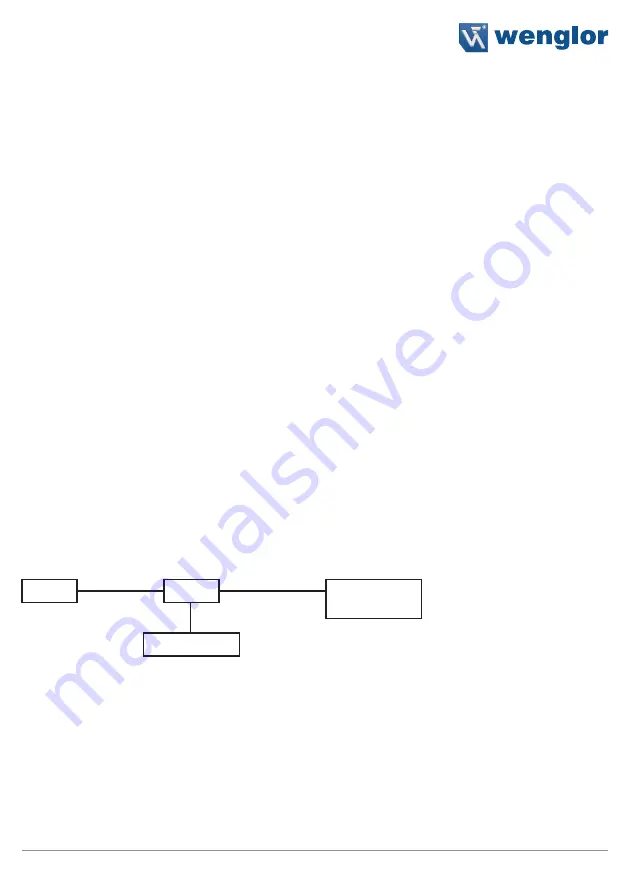
High-Performance Distance Sensor
13
7.3. Settings and Queries via the RS-232 interface
The interface utilises a software handshake procedure (see protocol specification below). All sensor settings
can be selected digitally with a PC, and all values generated by the sensor can be read out at a PC.
The RS-232 interface connections RxD (connection 5, grey) and TxD (connection 4, yellow) correspond to mi-
nus (connection 3, green) and can be connected to the appropriate connections of the communication partner.
Software Tools:
Software for the interface of the CP08 is available. Download address:
www.wenglor.com
Interface configuration:
Baud rate: 38.400 baud, 8 data bits, no parity, 1 stop bit
Plug connectors of the wenglor
®
Plug Adapter S232W3:
• 8-pin M12 plug connector for connecting the power supply and the outputs
• 8-pin M12 socket connector for direct sensor connection
• 9-pin M12 sub-miniature socket connector for direct connection to the RS-232 interface at the PC, or the
utilised controller
1) Connect the sensor over the wenglor
®
Plug Adapter S232W3 with PC, controller etc.
Installing the wenglor
®
Plug Adapter S232W3:
• Set the rotary selector switch
Ý
to
RUN
• Disconnect the 8-conductor connector cable (S80-xx) from the sensor
• Connect the S232W3 plug adapter directly to the sensor
• Connect the 8-conductor connector cable (S80-xx) to the plug adapter
• Connect the 9-pin sub-miniature socket connector to the serial interface at the PC
• Switch the power supply on
Sensor
Power Supply
Outputs
S232W3
PC, Controller
RS-232
Connecting the wenglor
®
sensor
to a PC or a controller
2) Procedure of the interface operation:
• Set the rotary selector switch
Ý
to
RUN
• To enter or query the sensor settings use the interface commands according to the protocol. Every interface
command and every answer of the sensor starts with “/” (ASCII 47) and ends with “.”. (ASCII 46) In case of
an incorrect communication, the sensor emits a Negative Acknowledge character (ASCII 21). If a command
is not closed with “.”, the sensor remains in wait state and does not give an answer or error message.
• Even with continuous query it should be adhered to a pause of 10 ms between two interface commands.
• Because of the protocol a maximum of 100 measurement values per second can be emitted. In the case
of faster applications use the analog output.