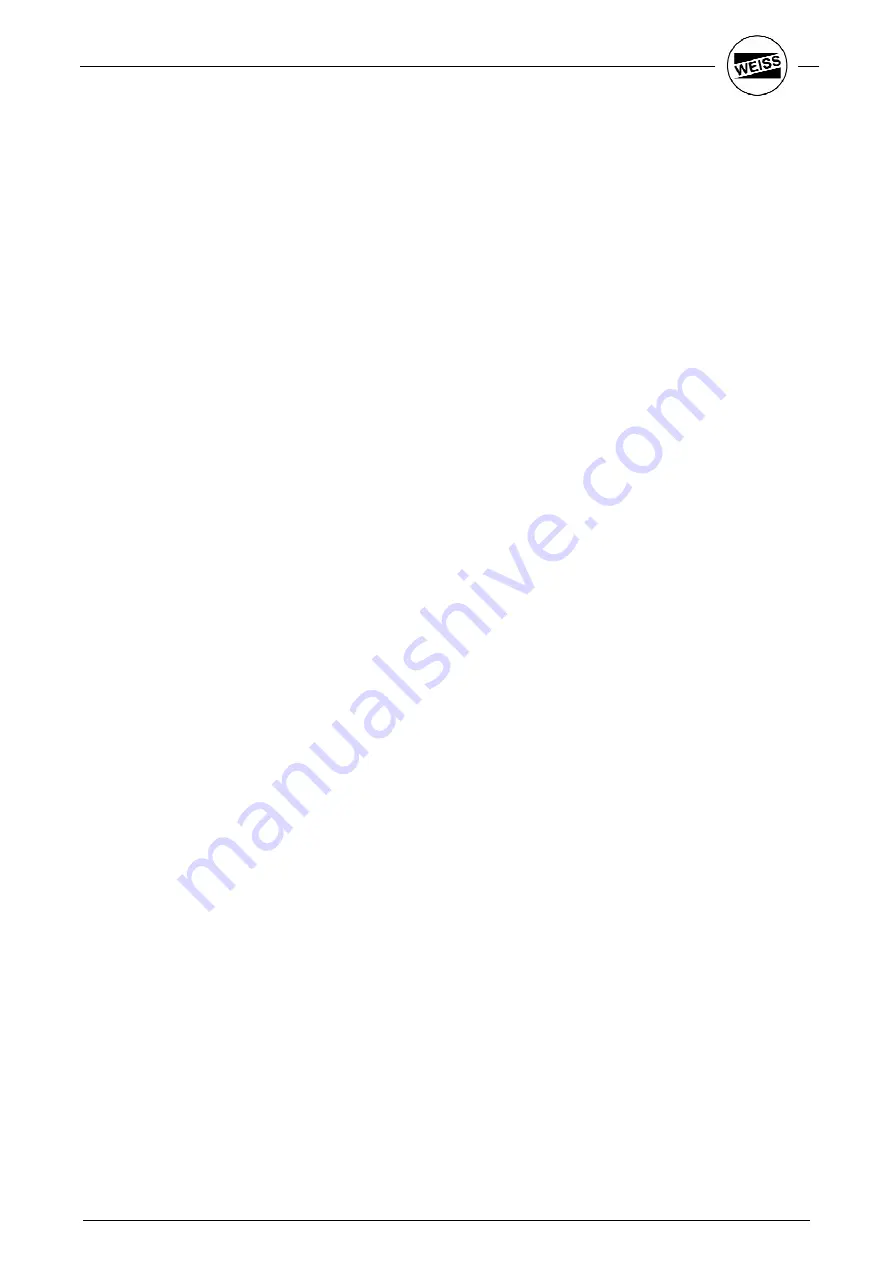
WAS.handling Windows Program
48
6 Quick start
The following brief description will allow you to get the HP140T ready for operation as soon as possible and
drive your first movements.
Note: Input of parameters must be confirmed by pressing ENTER.
b) Connection to the Slot-PLC
•
The connection to the control computer is done via RS232 interface (Ethernet cf. chapter
4.1.1). The cable must be plugged in.
•
Enter the interface of the PC (COM 1..8) using the File - Connection menu.
•
Leave dialog with OK. The connection is established automatically.
In the status bar, “OFFLINE“ is replaced by “…“.
c) Enter load
•
Open the “Y axis” dialog in the
Tools – Y axis
menu.
•
In
Part 1, Load
field enter the load, i.e. the sum of the gripper and work piece weight. Confirm
by pressing ENTER.
•
Accelerations and control parameters are adjusted automatically.
d) Communication with supervisory control
•
You’ll find the dialog for configuring the hardware in the
Tools – HW-Config
… menu.
The HP140TBB device should already be configured.
To communicate via digital inputs and outputs or via Profibus, open the dialog for I/O
configuration by pressing
I/O - Config
.
•
The inputs and outputs can be tested using the I/O Monitor. This can be found on the right
hand side of the tool bar.
e) Manual mode
•
Before the operation of the HP140 can be started, the hardware enable inputs of both drives
and the software enable (input “Enable”) must be present.
•
Open the dialog for manual mode using the
Test – Manual Mode
menu. This way, both axes
can be run in STEP mode and speed override may be entered. First a reference drive is
necessary.
f) Teach positions
•
Open the dialog for setting the positions using the
Program – Positions...
menu.
•
Using the buttons in the upper area, all positions can be reached.
•
The positions can be saved by right-clicking.
•
All values may be changed at will (confirm by pressing ENTER).
•
Subsequently, the positions are transferred to the control by pressing the “PC
PLC“
button.
g) Program drive sequences
•
Open the dialog for entering sequences using the Program – Sequences menu. Alternatively,
open the “Demo sequence” dialog. With this you can cyclically execute a sequence without
process communication.
•
The available commands can be strung together using the editor. For example: “Move to Pos
abs (all axes)” with the option “1” drives to the first position of the positions table.
h) Parameterize quick stop
•
To avoid damage to your system in case of an emergency shut-off, the QuickStop inputs of
both drives (terminal X1/2) should be wired and parameterized in the software.
•
You’ll find the parameter
QuickStop_Input
in the
Tools – Y axis
menu
Part 4
. It can be set to
HIGH active or LOW active. After the parameter has been changed, the slot CPU must be
restarted.
Summary of Contents for WAS.handling
Page 1: ......
Page 52: ...49 WAS handling Windows Program...
Page 58: ...55 WAS handling Windows Program...
Page 59: ......
Page 60: ......