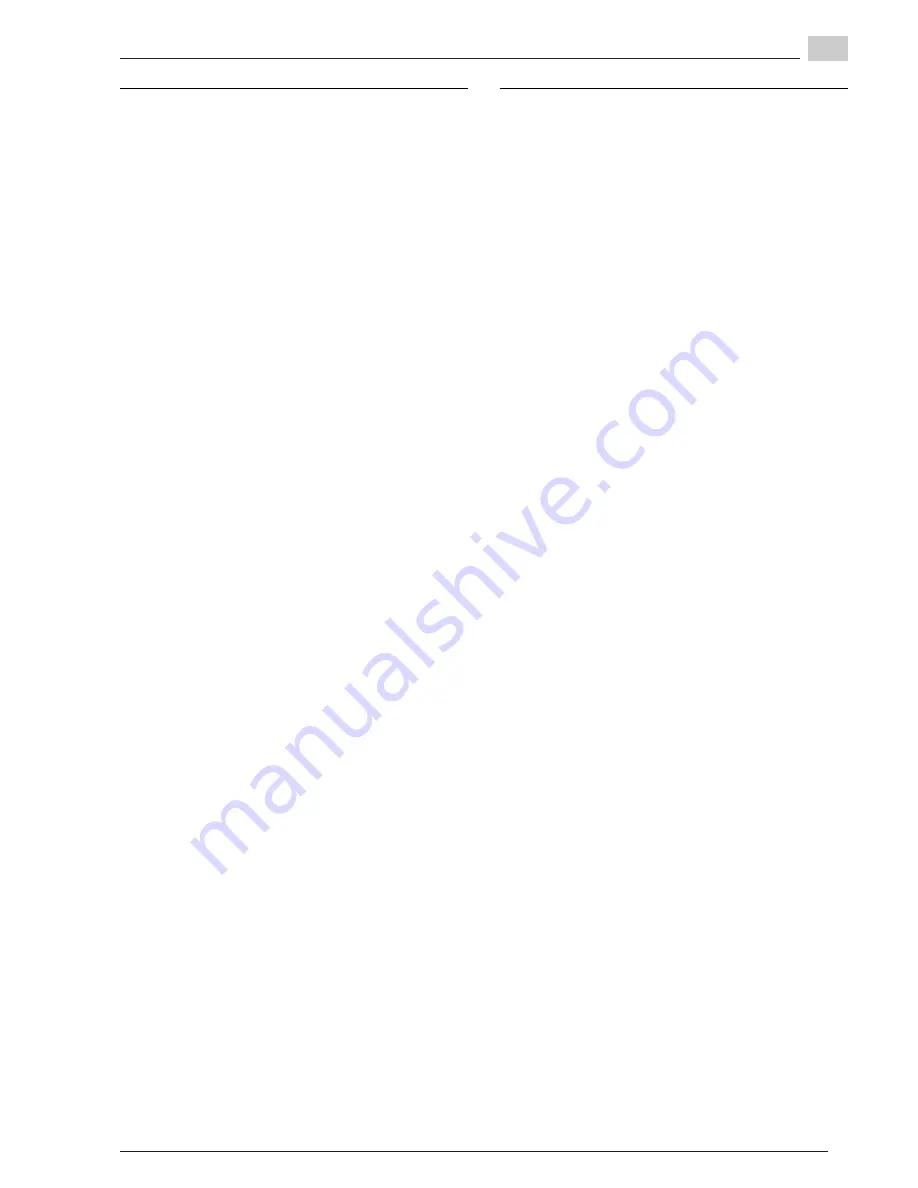
87
A
6.01
Gasket 25 x 38 x 2 (11/4)
481 401 40 05 7
6.02
Conn. pipe flow with sensor connection
WTC 45-A
481 401 40 02 2
WTC 60-A
481 601 40 02 2
6.03
NTC sensor G1/8
481 113 40 10 7
6.04
Screw M 5 X 8 DIN 912
402 223
6.05
Gas pipe fixing plate
481 401 02 13 7
6.06
Gas pipe with union nut
G3/4 WTC 45-A
481 401 30 41 2
G3/4 WTC 60-A
481 601 30 41 2
6.07
Gasket 17 X 24 X 2 DIN 2690
441 076
6.08
Connection pipe return
WTC 45-A vers. H-O
481 401 40 05 2
WTC 60-A vers. H-O
481 601 40 05 2
Pos.
Description
Order No
Pos.
Description
Order No
Summary of Contents for WTC 45-A
Page 75: ...75 A ...
Page 84: ...84 A 5 01 5 02 5 03 5 09 5 14 5 13 5 05 5 04 5 06 5 04 5 10 5 12 5 11 5 09 5 08 5 07 5 09 ...
Page 86: ...86 A 6 01 6 02 6 05 6 04 6 06 6 07 6 01 6 08 6 03 ...
Page 88: ...88 A ...
Page 89: ...89 A ...