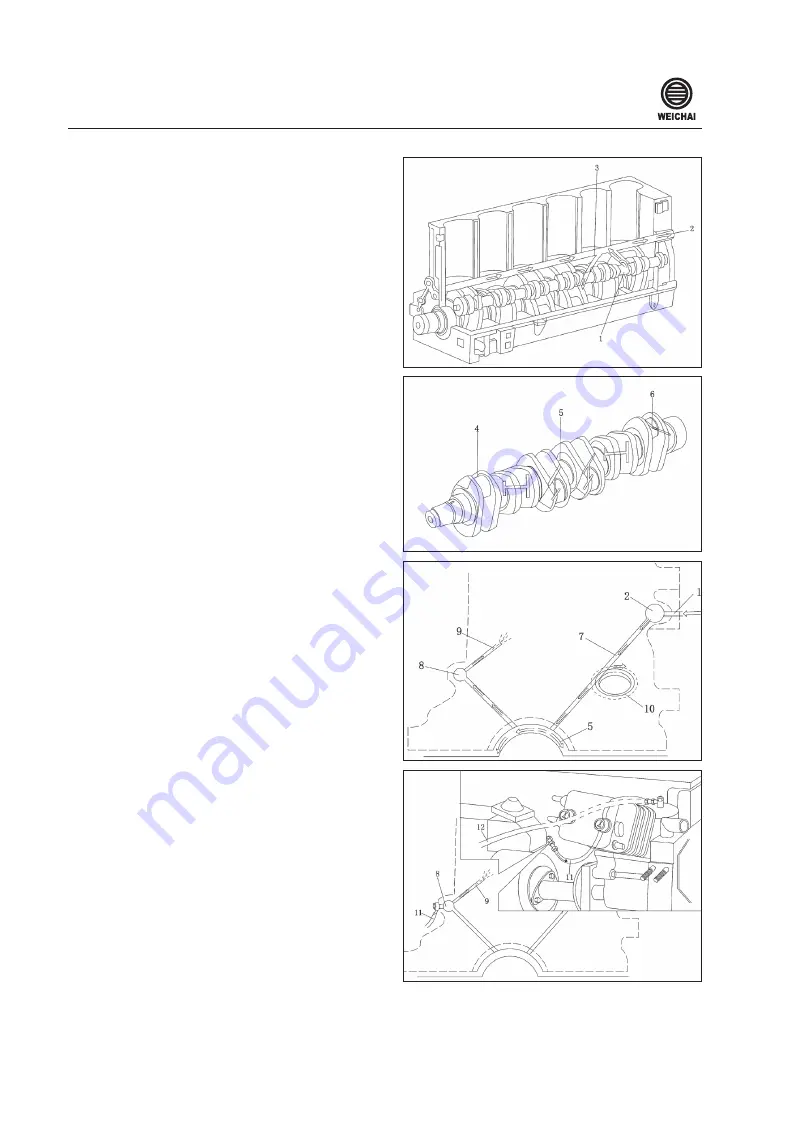
WD615欧Ⅱ系列柴油机维修保养手册
-0-
Maintenance Manual for WD615 Series EuroⅡDiesel Engine
各大运动零件的润滑
Lubricating for main moving parts
1.机油冷却器来油
The oil flowing from the oil
cooler
2.主油道
Main oil passage
3.通往主轴颈
Oil to the main crankshaft joumal
4.连杆轴颈
Connecting rod joumal
5.曲轴主轴颈处
The main journal of crankshaft
6.通往连杆轴承
Oil to connecting rod beating
7.主油道通向主轴承的斜油道
The branch oil passage passing
to main Dearing
8.付油道
Sub-passage of oil
9.冷却活塞喷油
Oil injection nozzle to cool piston
10.凸轮轴轴承
Camshaft beating
11.付油道来油润滑空压机
Lubricating air compressor
through the oil from sub-passage
12.付油道来油润滑喷油泵
Lubricating fuel injection pump
through the oil from sub-passage