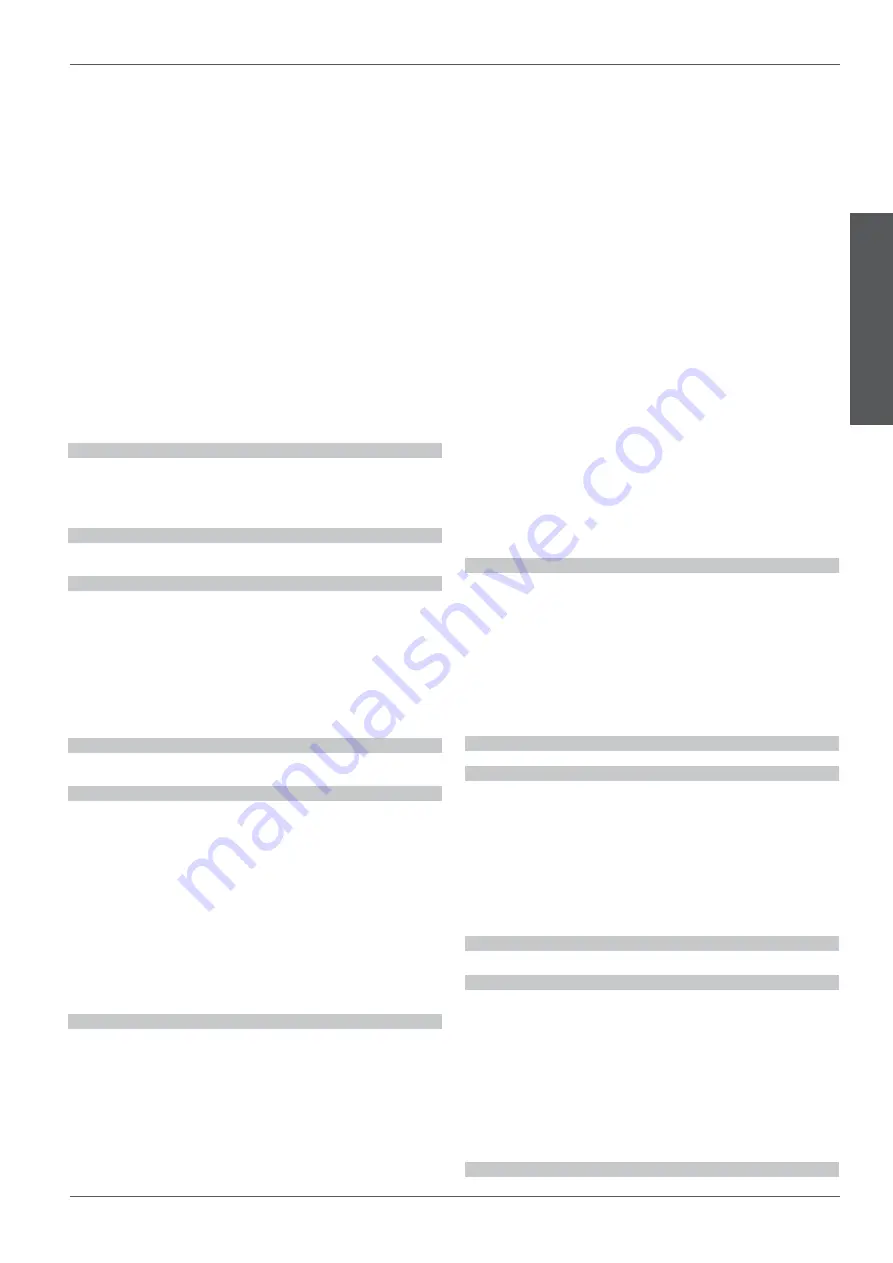
ENGLISH
Remove any rubber plugs which may be inserted in
the tap fixtures of the softener;
) using the provided flexible hose;
connect the outlet of the motor pump (
connect the drain pad of the machine (
) using the special hose provided, avoid-
) to the water supply so as to stop water
if there is no softener, connect the water supply (
directly to the inlet of the external motor pump (
if there is an internal motor pump, connect the outlet
of the softener (
) (if there is one) or the water supply
Summary of Contents for Wegaconcept
Page 1: ...ESPRESSO COFFEE MACHINE Use and maintenance manual for the TECHNICIAN ENGLISH Wegaconcept...
Page 3: ...English...
Page 7: ...7 Wegaconcept Technical manual ENGLISH Section I Operation...
Page 58: ...58 Wegaconcept Technical manual 33 Electric diagrams 33 1 Electronic control unit diagram...
Page 60: ...60 Wegaconcept Technical manual 33 2 Electronic control unit Diagram Rev 01...
Page 69: ...69 Wegaconcept Technical manual ENGLISH Section IV Interfaces...
Page 75: ......