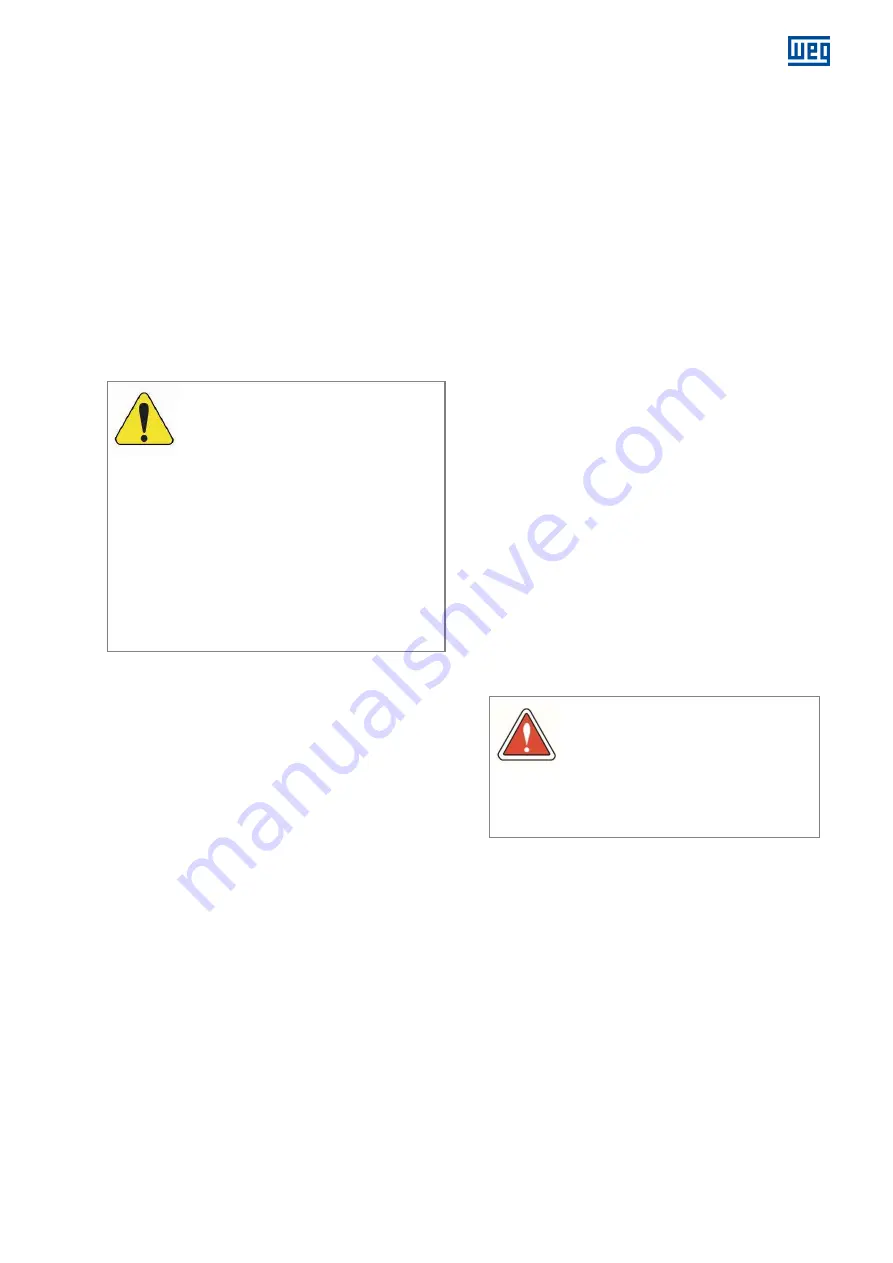
11371757 Installation, operation and maintenance manual – Squirrel cage motor – M line – Vertical
l 37
7
MAINTENANCE
7.1
GENERAL
A proper maintenance program for electric motors
includes the following recommendations:
Keep the motor and the associated equipment clean;
Measure the winding insulation resistance periodically;
Measure the temperature of windings, bearings and
cooling system periodically;
Check the wear, operation of the lubrication system and
useful life of the bearings;
Measure the motor vibration levels;
Inspect the cooling system;
Inspect associated equipment;
Inspect all the motor accessories, protections and
connections, ensuring that they are operating properly;
ATTENTION
Noncompliance with the recommendations
of section 7.1 may cause undesired
stoppages of the equipment.
The frequency of such inspections depends
on the local application conditions.
Every time that it becomes necessary to
transport the motor, the shaft must be
properly locked to prevent damages to the
bearings. Use the device supplied with the
motor to lock the shaft.
If the motor requires reconditioning or
replacement of any damaged part, consult
WEG.
7.2
GENERAL CLEANING
Keep the frame clean, without external accumulation of
oil or dust, in order to facilitate the heat exchange with
the environment;
The inside of the motor must also be kept clean, free of
dust, debris and oils;
For cleaning, use brushes or clean cotton cloths. If the
dust is not abrasive, the cleaning must be done with an
industrial vacuum cleaner, “aspiring” the dirt from the
fan cover and the dust accumulated on the fan blades
and on the frame;
Debris impregnated with oil or moisture can be
removed with a cloth soaked in appropriate solvents;
Clean the terminal boxes when necessary. Terminals
and connectors must be kept clean, free of rust and in
perfect operating conditions. Avoid the presence of
grease or verdigris in the connection parts.
7.3
WINDING MAINTENANCE
To obtain more satisfactory operation and a longer life of
the motor, the windings should be inspected and cleaned
annually.
7.3.1
Winding inspection
Yearly, the windings must be submitted to a complete
visual inspection, recording and repairing all and every
damage or defect observed.
The winding insulation resistance measurements must be
done at regular intervals, especially during humid weather
and after prolonged motor stoppages.
Low values or sudden variations in the insulation
resistance must be investigated.
The windings must be submitted to complete visual
inspections at frequent intervals, recording and repairing
all and every damage or defect observed.
The winding insulation resistance can be increased up to
an adequate value in the points where it is low (as a result
of excessive dust and moisture) by means of the dust
removal and by drying the winding moisture.
7.3.2
Winding cleaning
In order to obtain a more satisfactory operation and a
longer useful life of the insulated windings, it is
recommended to keep them free of dirt, oil, metal dust,
contaminants, etc.
Therefore, it is necessary to inspect and clean the
windings periodically, according to the recommendations
of the "Maintenance Plan" of this manual. If reimpregnation
is necessary, consult WEG.
The windings may be cleaned with an industrial vacuum
cleaner with a non-metallic crevice tool or just a dry cloth.
For extreme dirt conditions, it may be necessary to use a
proper liquid solvent for cleaning. This cleaning must be
quick to prevent prolonged exposure of the windings to
the solvent effects.
After being cleaned with solvents, the windings must be
completely dried.
Measure the insulation resistance and the polarization
index in order to assess the winding insulation conditions.
Winding drying time after cleaning varies depending on the
weather conditions such as temperature, humidity, etc.
DANGER
Most solvents currently used are highly
toxic and/or flammable.
Solvents must not be used in the straight
parts of the coils of high-voltage motors,
because they may affect the protection
against corona effect.
7.3.3
Inspections
The following inspections must be carried out after the
windings are carefully cleaned:
Check the insulations of the winding and connections;
Check if spacers, bindings, slot wedges, bandages and
supports are properly fixed;
Check for breaks, faulty welds, short-circuit between
turns and against the frame in the coils and
connections. In case any fault is detected, consult
WEG.
Ensure that all cables are properly connected and that
terminal fixation components are duly tightened.
Retighten, if necessary.
7.3.4
Reimpregnation
If any layer of resin on the windings is damaged during
cleaning or inspection, such parts must be corrected with
adequate material (in this case, consult WEG).