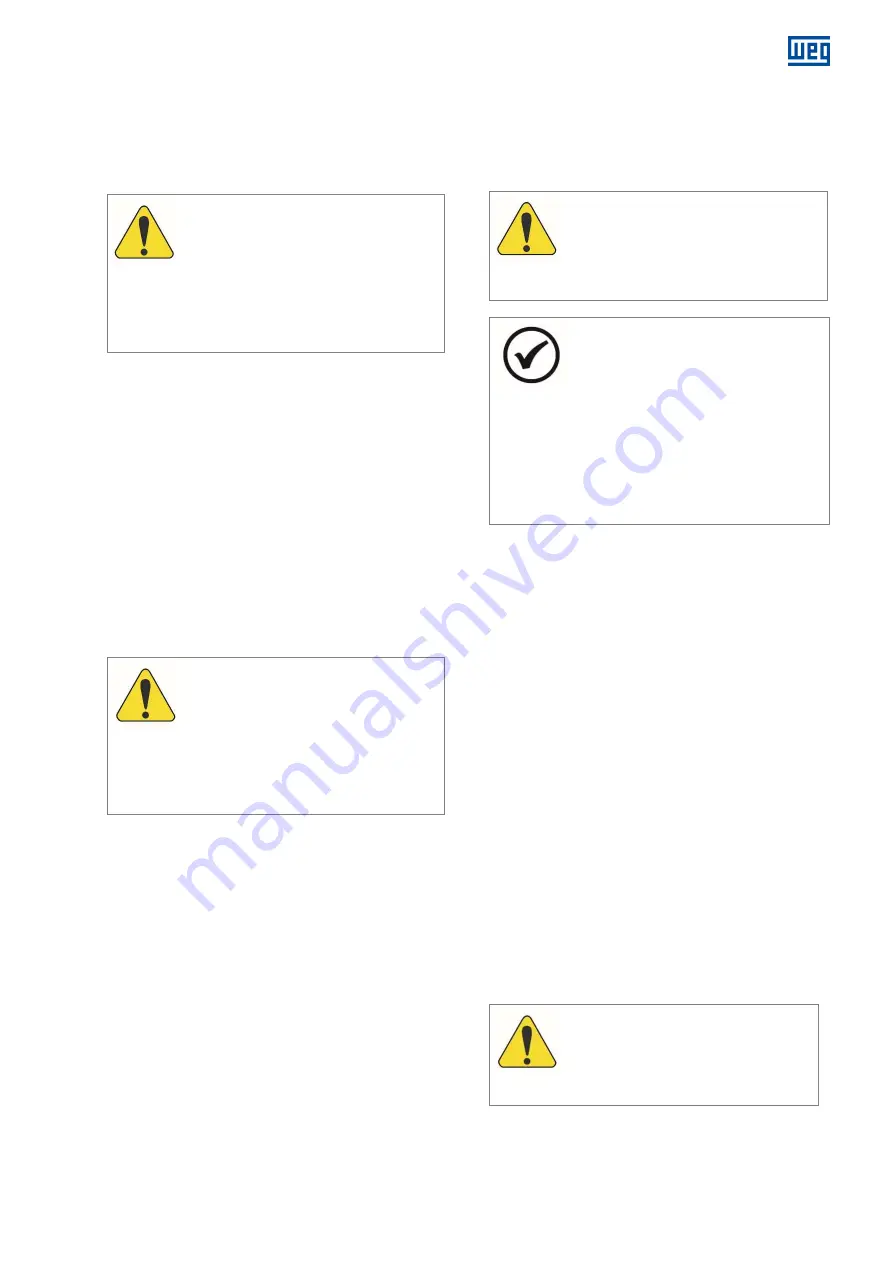
11371757 Installation, operation and maintenance manual – Squirrel cage motor – M line – Vertical
l 17
3.3.3.5
Bearings
3.3.3.5.1
Grease-lubricated rolling bearing
The rolling bearings are lubricated at the factory for the
motor tests.
ATTENTION
In order to keep the bearings in good
condition during the storage period, the
shaft locking device must be removed
every two months, and the motor rotor
must be rotated at least 10 complete turns
at 30 rpm to circulate the grease and
preserve the internal parts of the bearings.
Before putting the motor into operation, the
rolling bearings must be lubricated;
If the motor remains stored for a period
exceeding two years, the rolling bearings must
be disassembled, washed, inspected and
relubricated.
3.3.3.5.2
Oil-lubricated rolling bearing
Depending on the motor mounting position and on the
lubrication type, the motor can be transported with or
without oil in the bearings;
The motor storage must be done in its original
operating position and with oil in the bearings, when
specified;
The oil level must be respected, remaining in the
middle of the sight glass.
ATTENTION
In order to keep the bearings in good
condition during the storage period, the
shaft-locking device must be removed
every two months, and the motor rotor
must be rotated at least 10 complete turns
at 30 rpm to circulate the oil and preserve
the internal parts of the bearings.
Before putting the motor into operation, the rolling
bearings must be relubricated.
If the motor remains stored for a period exceeding 2
years, the rolling bearings must be disassembled,
washed, inspected and relubricated.
3.3.3.5.3
Sleeve bearing
Depending on the machine mounting position and the
lubrication type, the machine can be transported with or
without oil in the bearings.
The machine storage must be done in its original
operating position and with oil in the bearings, when so
specified.
The oil level must be respected, remaining in the middle of
the sight glass.
In order to keep the bearings in good conditions during
the storage period, the following preservation procedures
must be performed:
Close all the threaded holes with plugs;
Check if all the flanges (e.g., oil inlet and outlet) are
closed. If not, they must be closed with blind covers;
The oil level must be respected, remaining in the middle
of the oil sight glass;
Every two months, the shaft-locking device must be
removed, and the motor rotor must be rotated at least 10
complete turns at 30 rpm to circulate the oil and preserve
the internal parts of the bearings.
ATTENTION
If the motor has a radial locking device, used
for transport, it must be replaced according
to item 4.2.3, so that the motor shaft tuning
can be performed.
NOTES
For bearings that have a high-pressure oil
injection system (jacking), this system must
be activated before rotating the machine
rotor.
For bearings without oil tank (dry crankcase),
the oil circulation system must be activated
before rotating the machine shaft.
The shaft rotation must always be done in the
machine rotation direction.
After six months of storage, the following procedure must
be used for protecting both the bearing internally and the
contact surfaces against corrosion:
Close all the threaded holes with plugs;
Seal the gaps between the shaft and the bearing seal
on the shaft by applying water-proof adhesive tape;
Check if all the flanges (e.g., oil inlet and outlet) are
closed. If not, they must be closed with blind covers;
Remove the upper sight glass from the bearing and
apply the corrosion inhibitor spray (TECTYL 511 or
equivalent) inside the bearing;
Close the bearing with the upper sight glass.
Each six months of storage, repeat the procedure
described above.
If the storage period exceeds two years, the bearing oil
must be replaced.
3.3.3.6
Terminal boxes
When the insulation resistance of the motor windings is
measured, the main terminal box and the other terminal
boxes must also be inspected, observing the following
aspects:
The inside must be dry, clean and free of any dust
accumulation;
The contact elements cannot present corrosion;
The seals must be in proper condition;
The cable inlets must be correctly sealed.
ATTENTION
If any of these items are not in proper
condition, proceeds the adequate
maintenance and, if necessary, replace
damaged parts.