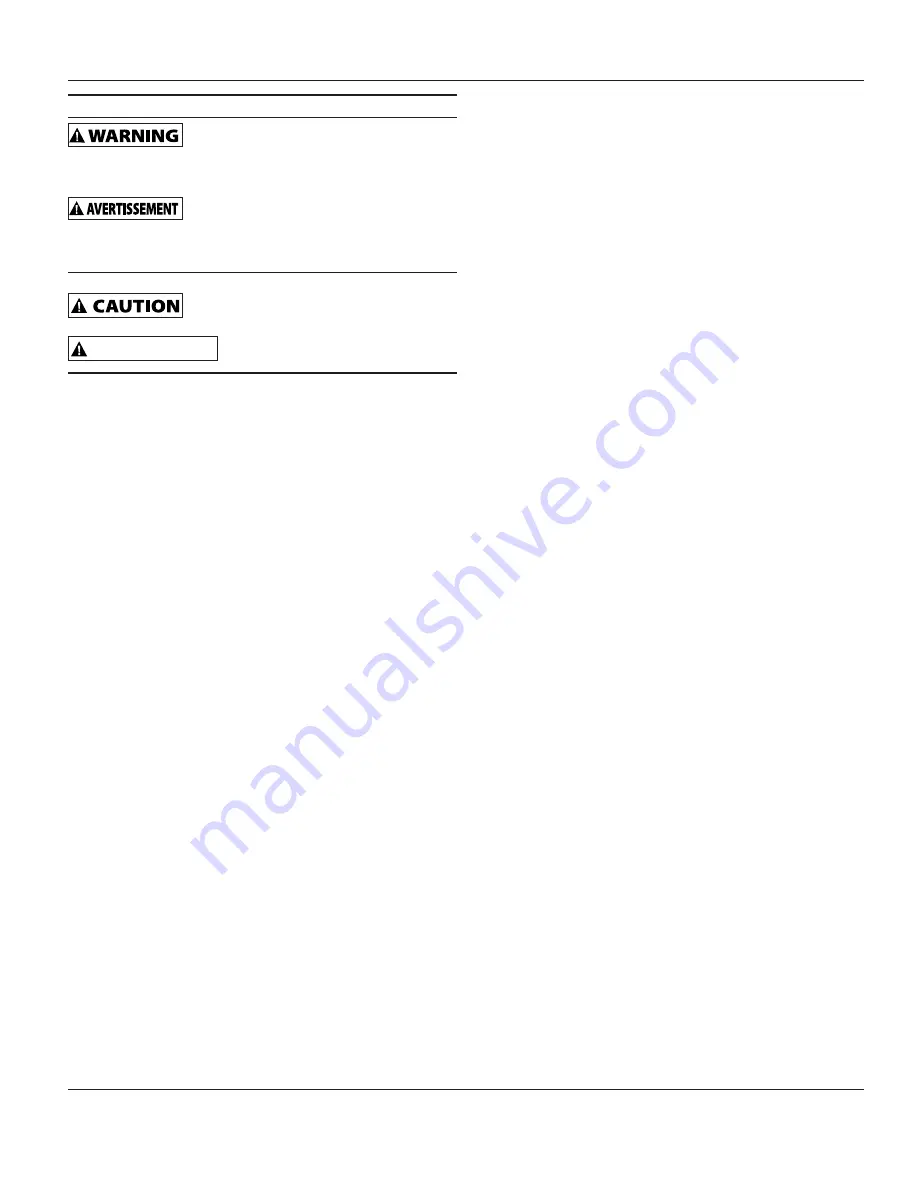
11
www.waynepumps.com
CWS Series
MAINTENANCE
Disconnect power and release all pressure from
the system before attempting to install, service,
relocate or perform any maintenance. Lock the power disconnect in the
open (off) position. Tag out the power disconnect to prevent unexpected
application of power.
Débrancher de la source d’alimentation puis
dissiper toute la pression du système avant
d’essayer d’installer, de réparer, de déplacer ou de procéder à l’entretien.
Verrouiller le sectionneur de courant en position ouverte (OFF). Étiqueter le
sectionneur de courant pour éviter toute mise sous tension imprévue.
Protect the pump from freezing during winter
conditions.
MISE EN GARDE
Protéger la pompe du gel pendant l’hiver.
DRAINING THE PUMP
Drain openings are provided on all models. To drain the pump:
1. Remove drain plug and prime plug to vent the system.
2. Drain all piping to a point below the freeze line.
DRAINING THE TANK
Conventional tanks can be drained by opening an outlet at the lowest
point in the system. Remove plug or the air volume control to vent the
tank.
Pre-charged tanks force virtually all the water from the tank when system
pressure is released. No draining is necessary.
RESTARTING PUMP
If the pump has been serviced, drained or has not been used for some
time, be sure there is water in the pump housing (volute) and the piping
to the well. There must be water in the pump housing (volute) at all times
when the pump is running to avoid internal damage of seal members
(See Priming the Shallow Well or Priming the Deep Well Sections).
WATERLOGGED TANKS: CONVENTIONAL
When a tank system has an inadequate ratio of air and water, the pump
will start and stop often and erratically.
1. Disconnect the power to the pump.
2. Open the lowest faucet in the system to release all pressurized water
in the system.
3. Prime the pump (See Priming the Shallow Well or Priming the Deep
Well Sections).
4. Reconnect the power to the pump.
NOTE:
As the pump refills the tank with water, the air volume control
supplies the tank with the correct air to water ratio for the system to
operate. If the air volume control is good, the pump will shut off at the
desired cut-off and will be adjusted correctly.
WATERLOGGED TANKS: PRE-CHARGED
If a pre-charged tank becomes waterlogged, the bladder is normally
leaking or broken.
1. Test the tank by depressing the air valve. The air valve will expel
water if the bladder is broken.
2. Replace the tank.
NOTE:
Once an internal bladder is leaking or broken, the bladder cannot
be repaired. The tank must be replaced.
PRE-CHARGED TANK
Some air is lost through the internal bladder in any tank. To prevent tank
failure, check the tank pre-charge on a yearly basis.
1. Disconnect power to the pump
2. Open a faucet nearest the tank and allow all water to drain from the
tank.
3. Measure the tank pre-charge at the valve stem using a tire gauge.
4. If necessary, adjust the pre-charge with an air pump 28 - 30 psi on
1/2, 3/4 and 1 HP pumps.
LUBRICATION
The bearing used in the pumps are lifetime lubricated at the factory and
require no additional lubrication.
CWS REPAIR KIT
1. Disconnect power from the pump.
2. Open faucet nearest the tank and allow all of the water to drain from
the tank and pump.
3. Remove 4 cap screws holding pump housing, do not disconnect
pressure switch (Figure 12).
4. Remove pump housing from pump assembly, move it out of the
way.
5. Using a 5/16” socket or flat blade screw drive remove the 2 screws
from the diffuser on the pump assembly.
6. Remove the diffuser.
7. Remove the black plastic cap from the back of the motor, exposing
the motor shaft end.
8. Using a large flat bladed screw driver hold the motor shaft while
unscrewing the impeller.
9. Remove the seal plate. Pay attention to how the original shaft seal is
installed before disassembly.