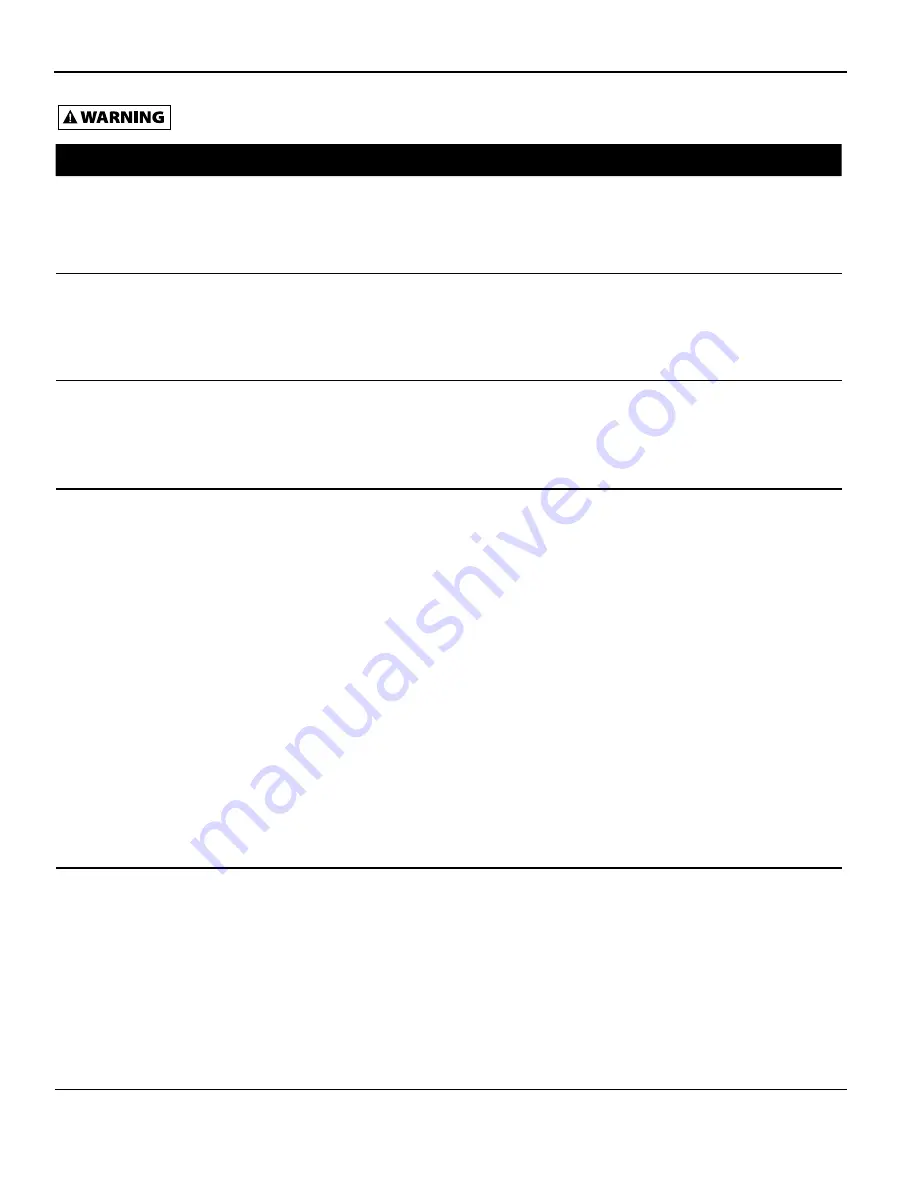
8
SWS Systems
Operating Instructions and Parts Manual
Symptom
Possible Cause(s)
Corrective Action(s)
Pump will not run
1. Power off
1. Turn power on or call power company
2. Blown fuse or tripped breaker
2. Replace fuse or reset circuit breaker
3. Faulty pressure switch
3. Replace switch
4. Motor overload tripped
4. Let cool. Overload will automatically reset
5. Low line voltage
5. Contact an electrician
Motor hums but
will not run
1. Line voltage does not match selector switch 1. Check line voltage and voltage selector switch (see
Figure 6 on page 4)
2. Inadequate wiring
2. Rewire
3. Damage or misalignment causing rotating
parts to bind
3. Replace or take to service shop for repair
4. Low line voltage
4. Contact an electrician
Overload trips
1. Low line voltage
1. Contact an electrician
2. Damage or misalignment causing rotating
parts to bind
2. Take to motor repair shop or locate and repair
mechanical binding
3. High surrounding temperature
3. Provide a shaded, well-ventilated area for pump
4. Rapid cycling
4. See Pump starts and stops too often section below
5. Inadequate wiring
5. Rewire
Pump runs but
delivers little or
no water
NOTE:
Check
prime before
looking for other
causes. Unscrew
priming plug and
see if water is in
priming hole.
1. Water level below pump intake
1. Lower suction pipe further into well
2. Discharge not vented while priming
2. Open faucet to allow air to vent while priming pump
3. Leak in suction piping
3. Repair or replace to fix leak
4. Well screen or inlet strainer clogged
4. Clean or replace to remove obstructions
5. Clogged nozzle
5. Clear obstruction from nozzle
6. Air volume control diaphragm ruptured
6. Replace air volume control
7. Foot valve may be clogged or stuck closed
7. Clean or replace as needed
8. Pump not fully primed
8. Continue priming, paus ing ev ery 5 minutes to cool
pump body. Refill pump as needed
9. Water level below maximum lift spec i fi ca
tion
9. Select applicable pump and/or jet as sem bly
10. Undersized piping
10. Replace as needed
11. Gaseous well
11. Install baffle on pump intake to prevent gas from
entering system
12. Distorted venturi
12. Inspect and replace
13. Incorrect jet for application
13. Purchase a jet matched to your sys tem
14. Undersized pump
14. Increase horsepower of pump
15. Pump cavitates, sounds like pumping gravel 15. Increase suction plumbing diameter or decrease
pipe friction
16. Low line voltage
16. Contact an electrician
Pump starts and
stops too often
1. Water-logged tank (Conventional tank)
1. Replace tank or air volume control
2. Air volume control tubing kinked or clogged
2. Clean or replace as needed
3. Air volume control tubing connected to wrong
opening on pump
3. Move to correct pump opening
4. Incorrect tank pre-charge (pre-charged tank) 4. Add or release air as needed
5. Ruptured diaphragm/bladder (pre-charged
tank)
5. Replace tank
6. Leak in house piping
6. Locate and repair leak
7. Foot valve or check valve stuck open
7. Remove and replace
8. Motor overload tripping
8. See overload trips section
9. Improperly adjusted or damaged pressure
switch
9. Adjust or replace switch
ELECTRICAL PRECAUTIONS - Before servicing a pump, ALWAYS shut off the main power breaker and then unplug the pump. Make sure you
are NOT standing in water and are wearing insulated protective sole shoes. Under fl ooded conditions, contact your local electric company
or qualifi ed licensed electrician for disconnecting electrical service prior to pump removal.
Troubleshooting Chart
www.waynepumps.com