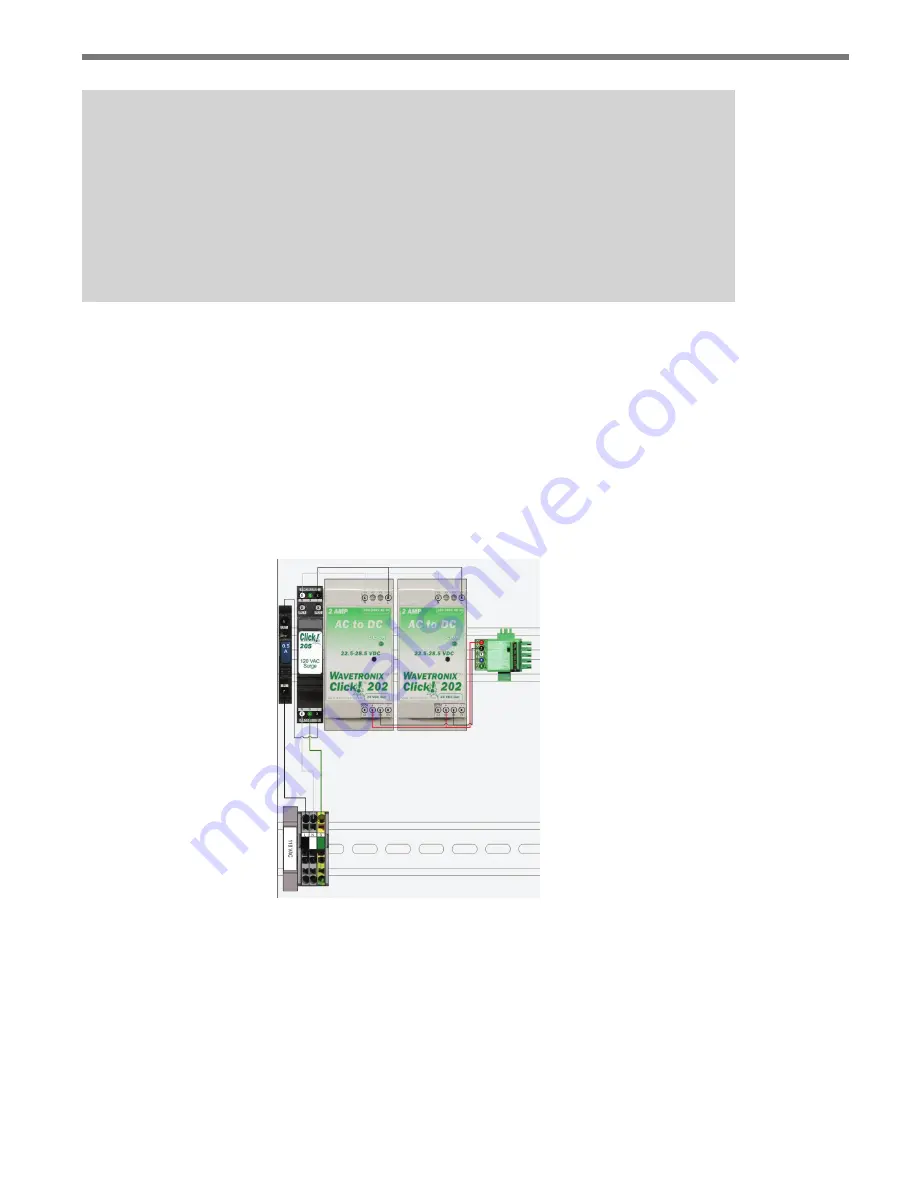
26
CHAPTER 2
•
CONNECTING POWER AND SURGE PROTECTION
Caution
An authorized electrical technician should install the intersection preassembled
backplate. Persons other than authorized and approved electrical technicians should
NOT attempt to connect the backplate to a power supply and/or traffic control cabi-
net, as there is a serious risk of electrical shock through unsafe handling of the power
source. Extreme caution should be used when connecting the backplate to an active
power supply.
The AC power conversion section of the backplate will come pre-wired as shown in Figure
2.3. The three main components of the AC power conversion section include:
˽
Click 201/202/204 AC to DC converter –
A Click 201 provides 1 A of power and is
capable of powering a single sensor; a Click 202 provides 2 A and can power two sen-
sors; a Click 204 provides 4 A and can power four sensors.
˽
Click 210 circuit breaker –
Interrupts power during overload conditions and provides
a convenient way to turn power on and off for the entire system.
˽
Click 230 AC surge protector –
Helps protect equipment from current surges on the
power lines.
Figure 2.3 – AC Power Conversion
Wiring Protective Earth Ground
All connections are surge protected when the protective earth ground is wired to the PE
terminal block on the backplate. Normally, the backplate should be mounted to the chassis
of the cabinet to provide a ground path. It is strongly recommended that you provide a low
impedance protective earth connection.