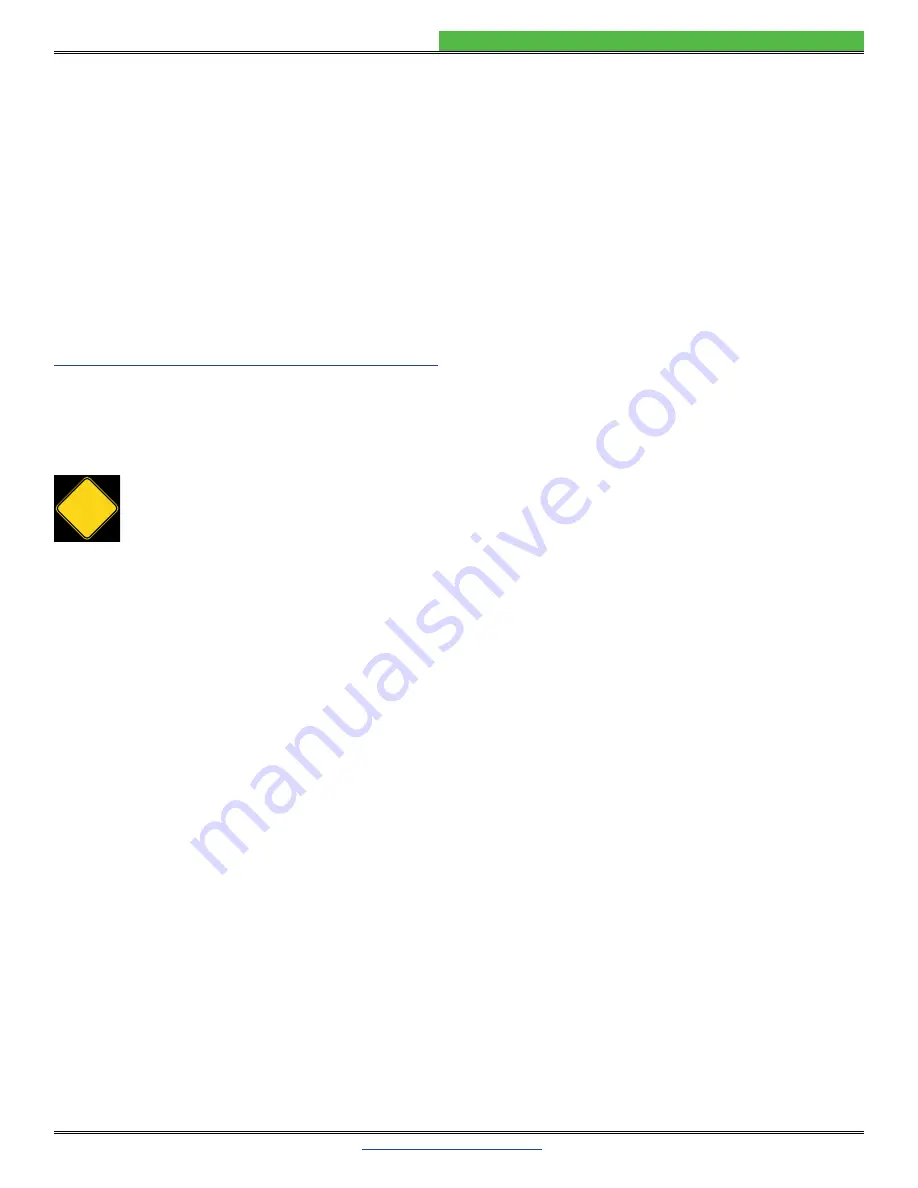
© 2020
6
PLD10000/PLD12500 LASER DIODE DRIVER
SAFETY INFORMATION
SAFE OPERATING AREA — DO NOT EXCEED
INTERNAL POWER DISSIPATION LIMITS
Before attempting to operate the PLD driver, it is imperative
that you first determine that the unit will operate within the
Safe Operating Area
(SOA). Operating outside of the SOA
may damage the PLD and the laser. Operating outside of
the SOA will void the warranty.
To determine if the PLD driver is suitable for your application
and if it will be operating in the safe range, consult the online
instructions for calculating the Safe Operating Area:
https://www.teamwavelength.com/support/design-tools/soa-ld-calculator/
https://www.teamwavelength.com/support/design-tools/soa-ld-calculator/
SOA charts are included in this datasheet for quick reference
(
), but we recommend you use the online tools
instead.
!
T
o
ensure
safe
operaTion
of
The
pLD
Driver
,
iT
is
imperaTive
ThaT
you
DeTermine
if
The
uniT
is
going
To
be
operaTing
wiThin
The
inTernaL
heaT
DissipaTion
s
afe
o
peraTing
a
rea
(soa).
If you have any questions about the Safe Operating Area
calculator call the factory for free and prompt technical
assistance.
THEORY OF OPERATION
The PLD10000 and PLD12500 drivers are controlled
linear-mode current sources: they deliver the current
commanded by the setpoint. The current source continually
monitors the actual output current, compares it to the
setpoint, and adjusts the current if there is a difference
between the two signals.
It may be useful to remember that you do not directly set the
drive current setpoint; instead, you adjust a voltage signal
that represents the output current. The voltage and output
current are related by a transfer function that varies by driver
model number.
The setpoint voltage is adjusted with the onboard trimpot or
by an external input that sums with the onboard setpoint.
The adjustable current limit is set using an onboard trimpot.
As current is driven through the load, there is a voltage drop
across the load because of the impedance. As the current
increases, the voltage drop may increase to the point that it
reaches the Compliance Voltage limit of the current source.
Once that occurs the current source is no longer able to
increase the current driven to the load even if you increase
the setpoint.
The PLD driver includes features that help protect your
laser and make the driver more versatile in a wide array of
applications:
• The user-adjustable latching current limit protects the
laser from over-current situations by switching off the
output when a limit condition is detected. Toggling the
Enable resets the current limit circuit.
• Output current switches on after approximately 1.5
seconds from the time the Enable signal is applied.
• Output slow-start ramps the current to setpoint over
250 msec.