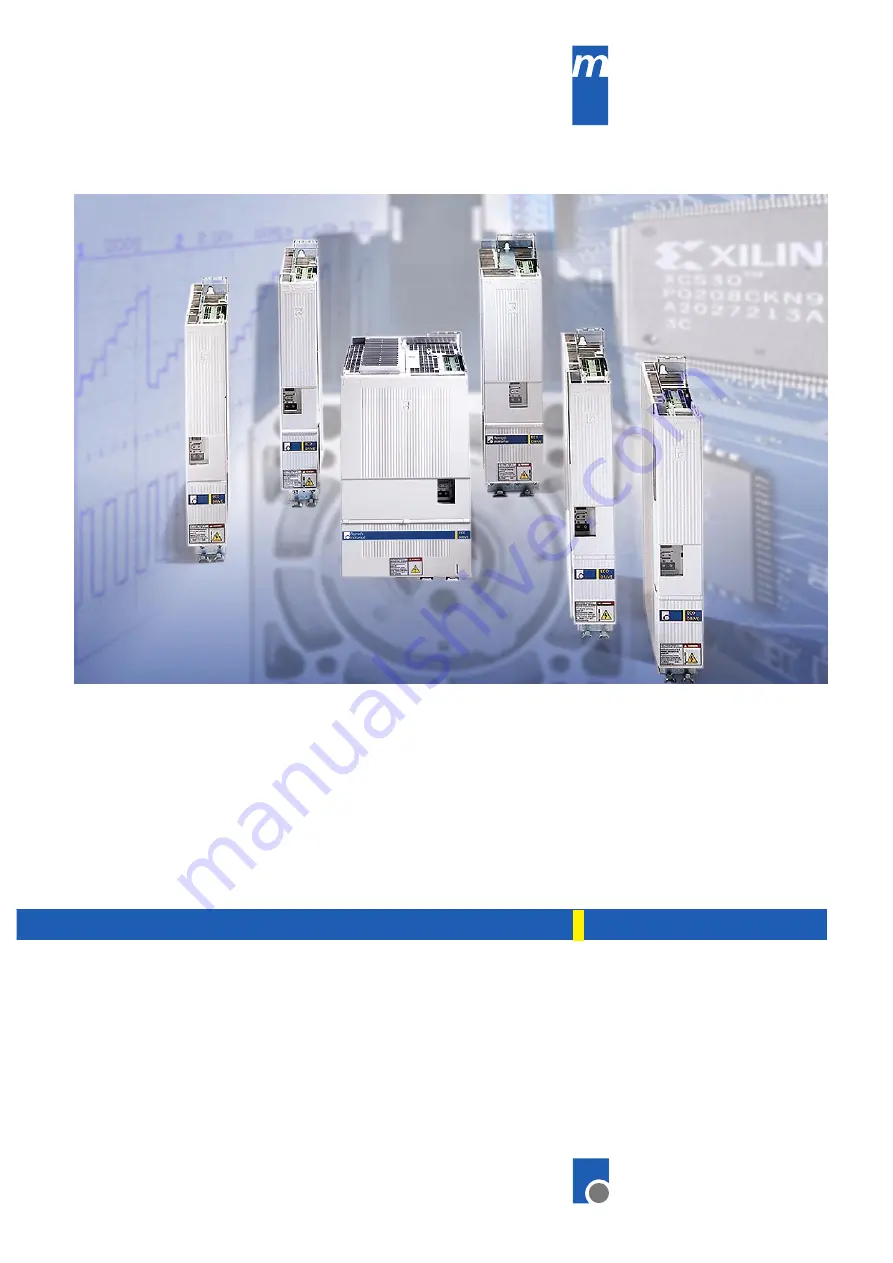
ECODRIVE03
Drive for Machine Tool Applications
With SERCOS-, Analog- and Parallelinterface
Troubleshooting Guide: SMT-02VRS
DOK-ECODR3-SMT-02VRS**-WA01-EN-P
mannesmann
Rexroth
engineering
Indramat
Rexroth
7=78)1
Summary of Contents for ecodrive03
Page 4: ...About this Documentation ECODRIVE03 SMT 02VRS DOK ECODR3 SMT 02VRS WA01 EN P Notes ...
Page 12: ...VIII Contents ECODRIVE03 SMT 02VRS DOK ECODR3 SMT 02VRS WA01 EN P Notes ...
Page 16: ...1 4 Diagnostic Message Descriptions ECODRIVE03 SMT 02VRS DOK ECODR3 SMT 02VRS WA01 EN P Notes ...
Page 122: ...Index ECODRIVE03 SMT 02VRS DOK ECODR3 SMT 02VRS WA01 EN P Notes ...
Page 127: ......