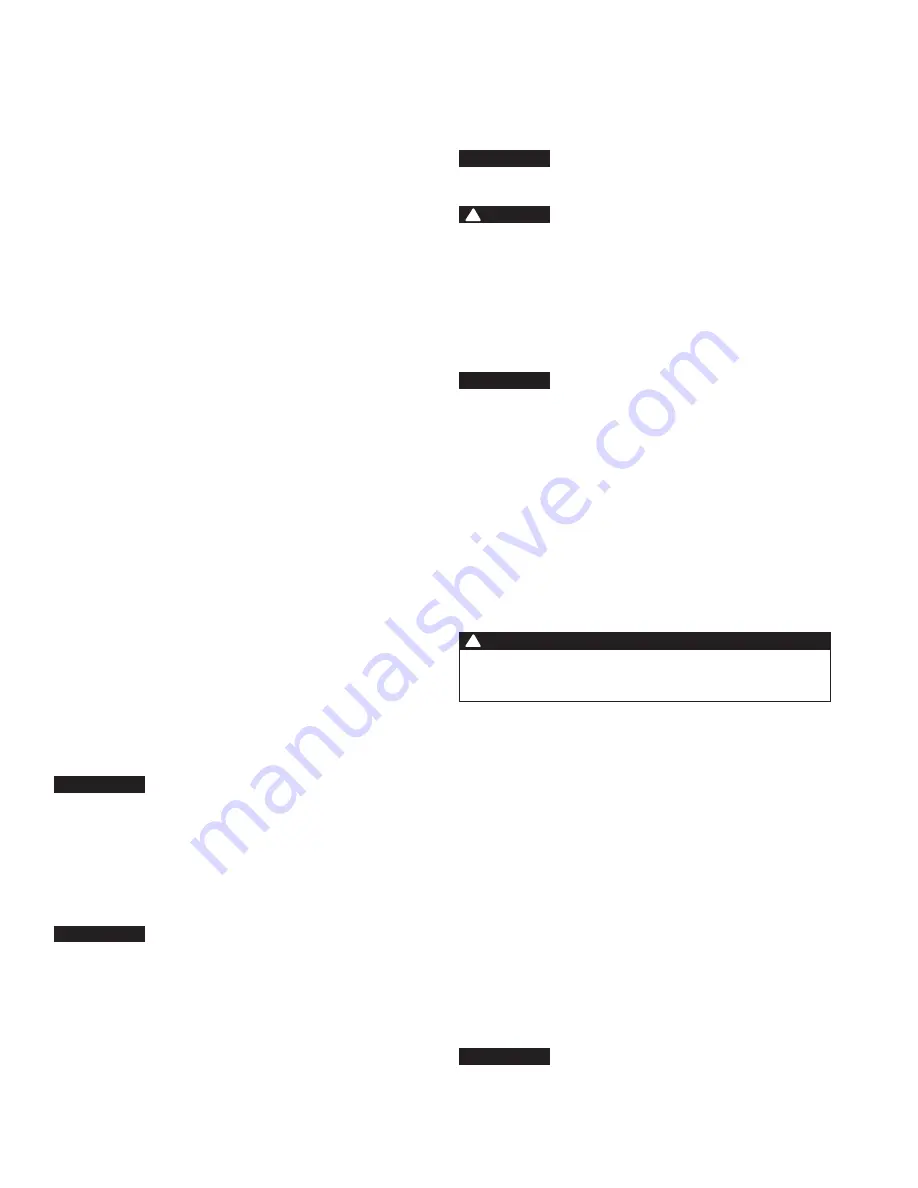
6 PWSR Series Softeners
Pre-Installation Considerations
(continued)
G. Pre Installation and Loading of Media
Systems that are 13” in diameter and larger are not loaded with
media . These systems must be loaded with media before placing
into service . To load a system follow the below steps .
1 . Cap the top open end of the distributor tube with tape and
plastic sheeting to keep foreign debris from entering the
distributor tube . This cap must be secure and not come off
during media loading .
2 . Place the distributor tube, screen end down, into the mineral
tank and center it in the bottom . The top of the distributor tube
should be flush with the top of the tank .
3 . Make sure the plastic and tape cap is secure to the top of the
distributor tube, place a funnel on the top of the tank and load
first the gravel (if different sizes of gravel are used load the
largest gravel first, then the smaller gravel) then the resin media
into the tank . The cap must not come off of the distributor tube
during the loading of the media .
4 . Remove the plastic cap from the distributor tube .
DO NOT
PULL UP ON THE DISTRIBUTOR TUBE
when removing the
cap . The distributor tube top must remain flush with the top of
the tank .
5 . Clean any media from the threads and top of the mineral tank .
6 . Lubricate the O-rings on the bottom of the control valve
(distributor pilot O-ring and top of tank O-ring) . Use non-
petroleum based silicone lubricant only .
7 . Place the control valve on top of the tank . When doing this
step, seat the top of the distributor tube inside the centered
O-ring sealed port on the bottom of the valve first then press
the valve down until the tank threads come in contact with the
valve threads . This ensures that the distributor tube is properly
seated into the bottom of the control valve . Thread the valve
on to the tank clockwise . Be careful not to cross thread the
valve or over tighten it . A hand tight snug fit is appropriate for
the control valve torque . A wrench is not necessary . Do not use
thread sealant or PTFE tape on the valve base threads .
8 . The system is now ready for installation . Follow the Installation
Section in the Installation, Operation and Maintenance Manual .
Installation Instructions
.
1 . Turn off water heater(s) .
2 . Turn off the main water supply to the home and open an inside
faucet (cold and hot) to relieve any pressure within the plumbing
system .
Select Location
1 . Place the system in the desired installation location . Make sure
that the location is level and sturdy enough to support the weight
of the system once it is in operation .
2 . You will need to locate the water softener at least 10 feet away
from the hot water heater so that hot water does not backup
and damage the softener .
3 . You will need a drain close by for disposal of regenerated waste-
water .
4 . If installing the softener in an outside locations, make sure to
protect softener from the elements, such as freezing tempera-
tures, rain, sunlight and contamination
Install a By-Pass
Always install a bypass, either a 3-way valve system or the standard
bypass for the valve you have . This will allow you to shut off the
water supply to the softener, but still have water in the house if the
softener is in need of repair .
WARNING
!
Do not exceed water pressure of 120 psi (8.2 bar). Do not
exceed 110°F (43.3°C). Do not subject unit to freezing
conditions.
Installation Preview
Conduct a visual check of all equipment for any damage that may
have occurred during shipment .
If there is obvious damage to any equipment, it should be noted
on the carrier’s Bill Of Lading . Open and inspect the contents of all
closed crates, cartons, etc . and inspect for concealed damage . The
manufacturer is not liable for any dam-age during transit .
Position the equipment in its proper location, setting on a flat
surface . Level equipment as required . Equipment out of plumb can
exhibit poor flow characteristics, which will affect the performance of
the system .
Units are shipped with media (resin & gravel), distributions tube, and
control valve installed . Double-check the valve installation on the
tank . Tighten if necessary .
Unit should be positioned with the valve control facing forward .
Check the main line water pressure . The softener is designed for a
minimum of 20 psi and a maximum of 125 psi working pressure . If
the line pressure exceeds this limit, a pressure-reducing valve should
be installed .
Maximum allowable water temperature is 40°F (4°C) – 110°F (38°C) .
A 120vac 60 cycle electrical source must be available for operation
of the controller .
Connect raw water supply line to the inlet valve connection . Connect
treated water outlet to service line . It is suggested that the pipe size
be equal or one size larger than the valve connection .
Softener to be located at least 10 feet away from hot water heater to
protect against hot water back-up .
When piping with copper, solder all piping as sub-assemblies before
installing . Internal damage can result from the high heat of the torch .
It is recommended that manual isolating valves be installed on the
inlet and outlet piping along with a system bypass valve . This will
isolate the unit when service is required . Run drain line to a sump,
drain trench, or other open drain . Open drains are required for taking
samples and allowing a visual check . Avoid overhead pipe runs to
drain facility, as undue backpressure will affect the operation of injec-
tors .
All piping is to meet your local and state code .
AVOID CROSS
CONNECTIONS!
Position brine tank approximately 6” from the softener tank on a
smooth surface .
Connect the brine air check assembly in the salt/brine tank to the
brine suction (eductor) connection . If brine tank is located more than
6 feet from softener tank, use one size larger tubing . Tubing 5/8”
should be installed from the brine tank over-flow to drain . This is a
gravity drain designed to divert brine to the drain in the event of a
malfunction, which would cause overflow of the brine tank .
Be sure inlet/outlet isolating valves are closed and bypass valve is
open .
Installation Preview (continued)
NOTICE
NOTICE
NOTICE
NOTICE
WARNING
!
NOTICE
Summary of Contents for PWSR Series
Page 27: ...NOTES ...