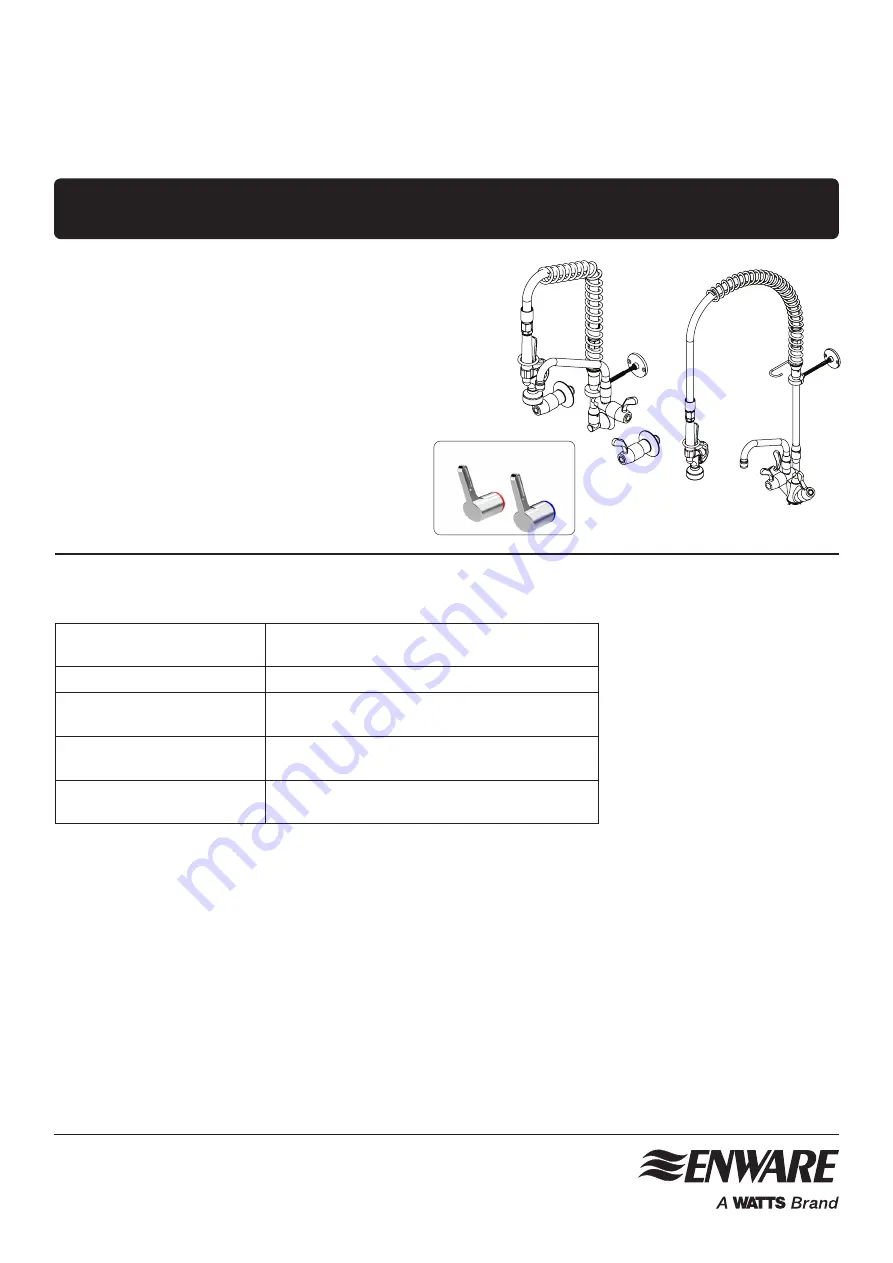
technical data
Enware products are to be installed in accordance with the Plumbing Code of Australia (PCA) and AS/NZS3500.
Installations not complying with PCA and AS/NZS 3500 may void the product and performance warranty provisions.
Reference should also be made to the Australasian Health Facility Guidelines (AHFG), ABCB and Local Government
regulations when considering the choice of, and the installation of these products.
This product must be installed and commissioned by a qualified plumber.
For use with potable water only.
NOTE: Enware Australia advises:
1. Due to ongoing Research and Development, specifications may change without notice.
2. Component specifications may change on some export models.
Working Pressure Range
Min 50 kPa
Max 500 kPa
Maximum Static Pressure
1200 kPa
Maximum Working
Temperature
95°C (Jumper Valve)
85°C (Spring loaded valve / Pre-Rinse spray gun)
Inlet Connection
1/2” BSP
5/8” BSP (In-wall recessed SBA)
Flow Rate
4 L/min (Pre-rinse spray gun)
8 L/min (Pot filler)
FHS001
FHS002
FHS011
FHS021
FHS031
FHS041
FHS121
FHS131
FHS141
FHS141C
FWS001
FWS011
FWS021
FWS031
FWS031ADJ
FWS101
Installation and Maintenance Instructions
Food Service Pre-Rinse Assemblies
I00063_09 Oct 2023
1300 369 273 | [email protected] | enware.com.au
With New Leva Handles
FWS121
FWS121C
FWS121W
FWS131
FWS131ADJ
FS704