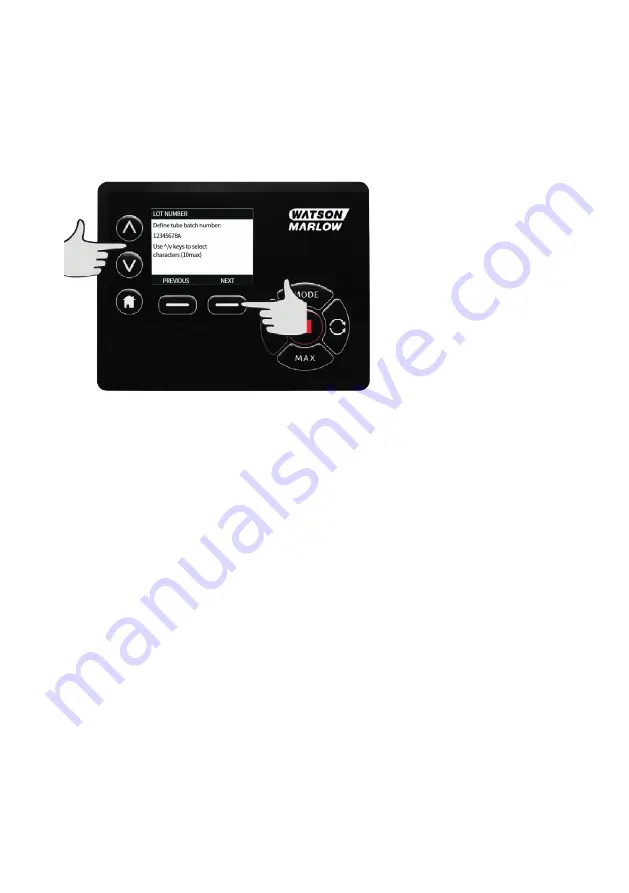
The PUMPHEAD MODEL screen allows the tube Lot Number to be recorded for future reference. Use the
∧
/
∨
keys to move the selection bar over
Tube lot number
and press
SELECT
.
Use the
∧
/
∨
keys to scroll through the available characters for each digit. The available characters are 0-9,
A-Z, and SPACE.
Press
NEXT
to move onto the next character, or
PREVIOUS
to move back to the last character.
Press
FINISH
to save the entry and return to the general settings menu.
Restore defaults
To restore the factory default settings select
Restore defaults
from the general settings menu.
There are two confirmation screens to ensure that this function is not carried out in error.
m-630dun-en-08.2
101
Summary of Contents for 630 Du
Page 81: ...m 630dun en 08 2 81 ...