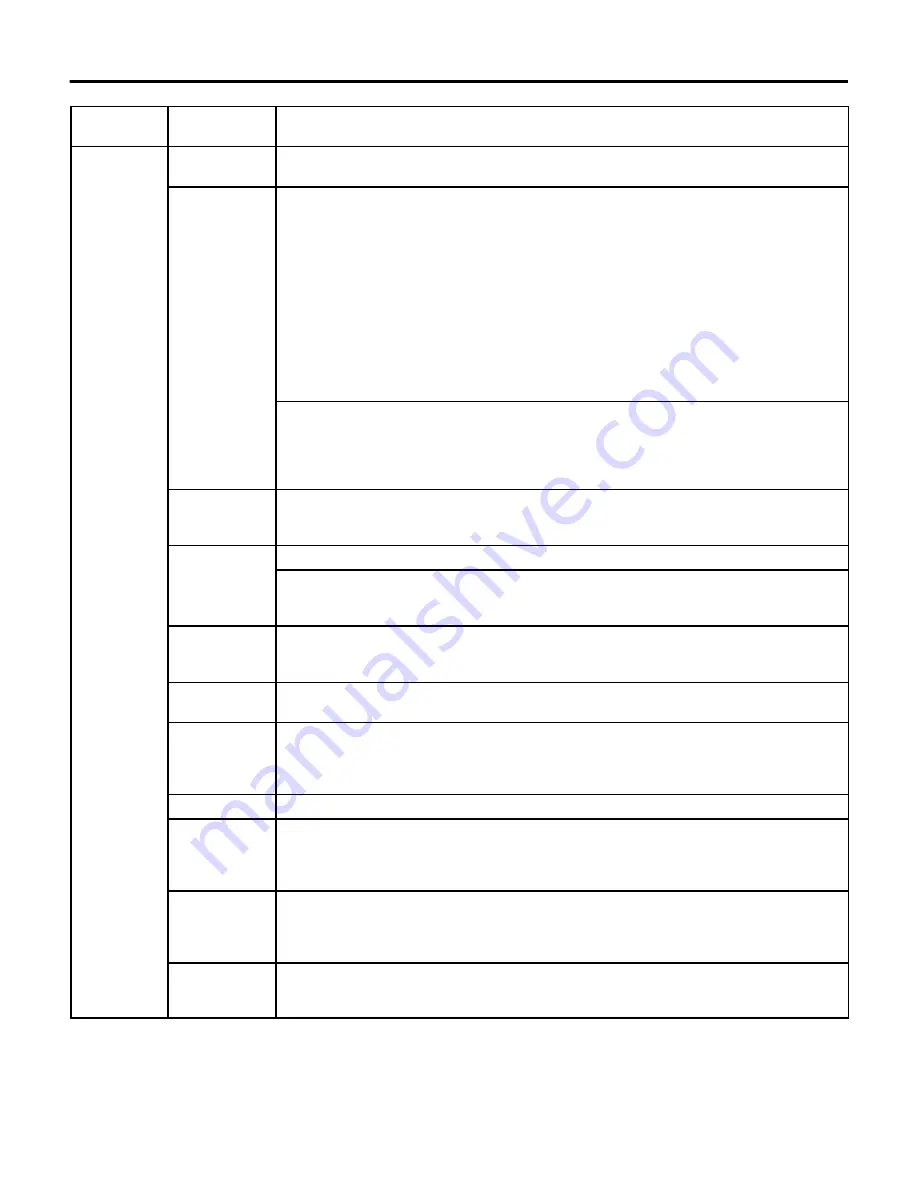
TROUBLESHOOTING
Page 19 of 20
CONDITION
POSSIBLE
CAUSE
SUGGESTED REMEDY
Pump fails to
prime or
loses prime
Priming line
petcock closed
Open the priming line petcock at the suction inlet of the pump body when priming.
Air leaks
Clean and tighten all intake connections. Make sure intake hoses and gaskets are in
good condition. Use the following procedure to locate air leaks:
1.
Connect intake hose to pump and attach intake cap to end of hose.
2.
Close all pump openings.
3.
Start engine and advance throttle to “FAST” position.
4.
Pull the priming lever to “PRIME” position until intake pressure gauge
indicaates 22 in. Hg (If primer fails to draw specified vacuum, it may be
defective, or leaks are too large for primer to handle).
5.
Return the priming lever to the “RUN” position and shut off engine. If vacuum
drops more than 10 in. Hg in 5 minutes, serious air leaks are indicated. With
engine stopped, air leaks are frequently audible. If engine leaks cannot be
heard, apply engine oil to suspected points (intake hose connections, piping
joints, mechanical seal) and watch for break in film or oil being drawn into pump.
Completely fill water tank (if so equipped). Connect intake hose to hydrant or auxiliary
pump. Open one discharge valve and run in water until pump is completely filled and air
is expelled. Close discharge valve, apply pressure to system and watch for leaks or
overflowing water tank. A pressure of 100 psi (8.6 bar) is sufficient. DO NOT EXCEED
RECOMMENDED PRESSURE.
Air trapped in
pump and
piping
When pumping from a water tank, priming the pump may be necessary under some
conditions because of air trapped in pump and piping.
Dirt on intake
strainer
Remove all leaves, dirt and other foreign material from intake strainer.
When drafting from shallow water source with mud, sand or gravel bottom, protect intake
strainer by suspending it from a log or other floating object to keep it off the bottom.
Anchor float to prevent it from drifting into shallow water.
Defective
primer
After prolonged service, the engine muffler, spark arrestor or exhaust primer may be
come plugged with carbon deposits or rust. Disassemble and clean or replace compon
ents as required.
Engine speed
too low
Advance throttle to “FAST” position.
Bypass line
open
If a bypass line is installed between the pump discharge and water tank to prevent pump
from overheating with all discharge valves closed, look for check valve in the line. If the
valve is stuck open, clean it, replace it or temporarily block off line until a new valve can
be obtained.
Lift too high
Reduce the vertical distance between the water source and the pump intake.
End of intake
hose not sub
merged deep
enough.
Although intake hose might be submerged enough for priming, pumping large volumes
of water may produce whirlpools, which will allow air to be drawn into intake hose.
Whenever possible, place end of intake hose at least two feet (.6 m) below water source.
High point in
intake line
If possible, avoid placing any part of intake hose higher than pump inlet. If high point
cannot be prevented, close discharge valve as soon as pressure drops, and prime
again. This procedure will usually eliminate air pockets in line, but it may have to be
repeated several times.
Primer not
operated long
enough
The maximum time for priming should not exceed 45 seconds for lifts up to 10 feet (3m).