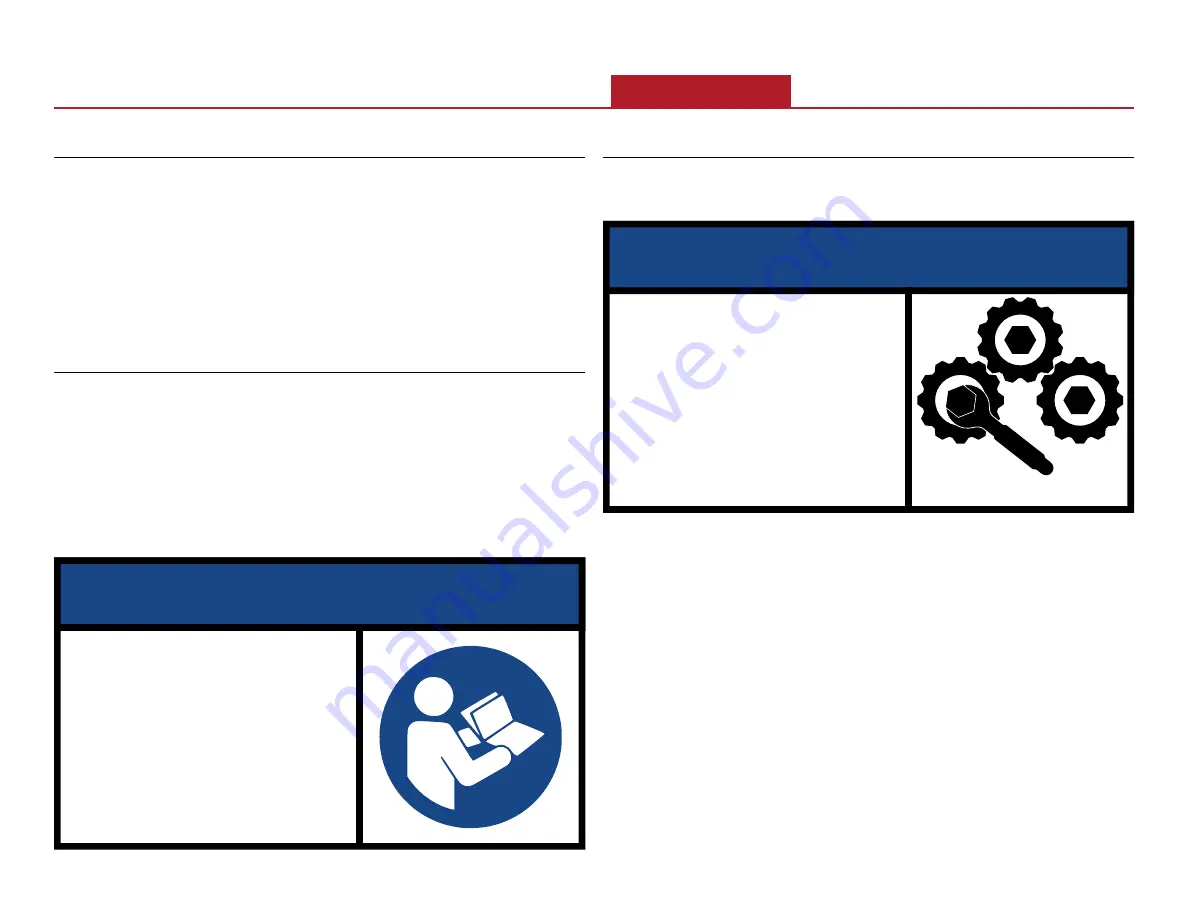
89
|
217
Product Overview
Operation
Installation Overview
This equipment is intended to be installed by a person or persons with the basic
knowledge of installing similar equipment. Contact Waterous with questions
about installing the equipment. The installation may require the following tasks
and abilities:
•
Locating, drilling, and cutting
features into the apparatus.
•
Welding
•
Installing the hoses and fittings.
•
Routing and securing the hoses.
•
Routing and securing the wiring.
•
Calibrating the output.
•
Calibration and final testing.
Preparing for the Installation
Use the following guidelines before, during, and after the installation.
•
Read and understand all the installation instructions before installing the
equipment.
•
Prepare a suitable, well-lit area, and gather all the necessary tools before you
begin the installation.
•
Make sure that you remove any shipping plugs or caps before installing the
component.
•
Make sure that you bring all fluids to operating levels before using the
equipment.
NOTICE
Before Operation
• Read and understand all
the instructions provided.
• Check all fluid levels
and replenish if necessary.
• Remove all shipping plugs
and install the operation
plugs or caps.
Modifying the Equipment
This equipment is intended to operate as designed. Do not remove, modify, or
change the components in the system. Doing so will void the warranty. Contact
Waterous for more information.
NOTICE
Modifying the equipment
can damage components
and void your warranty.
•
Do not modify the system
or any of its components.
•
Modification
Do not modify the system or any components. Doing so will void your
warranty.