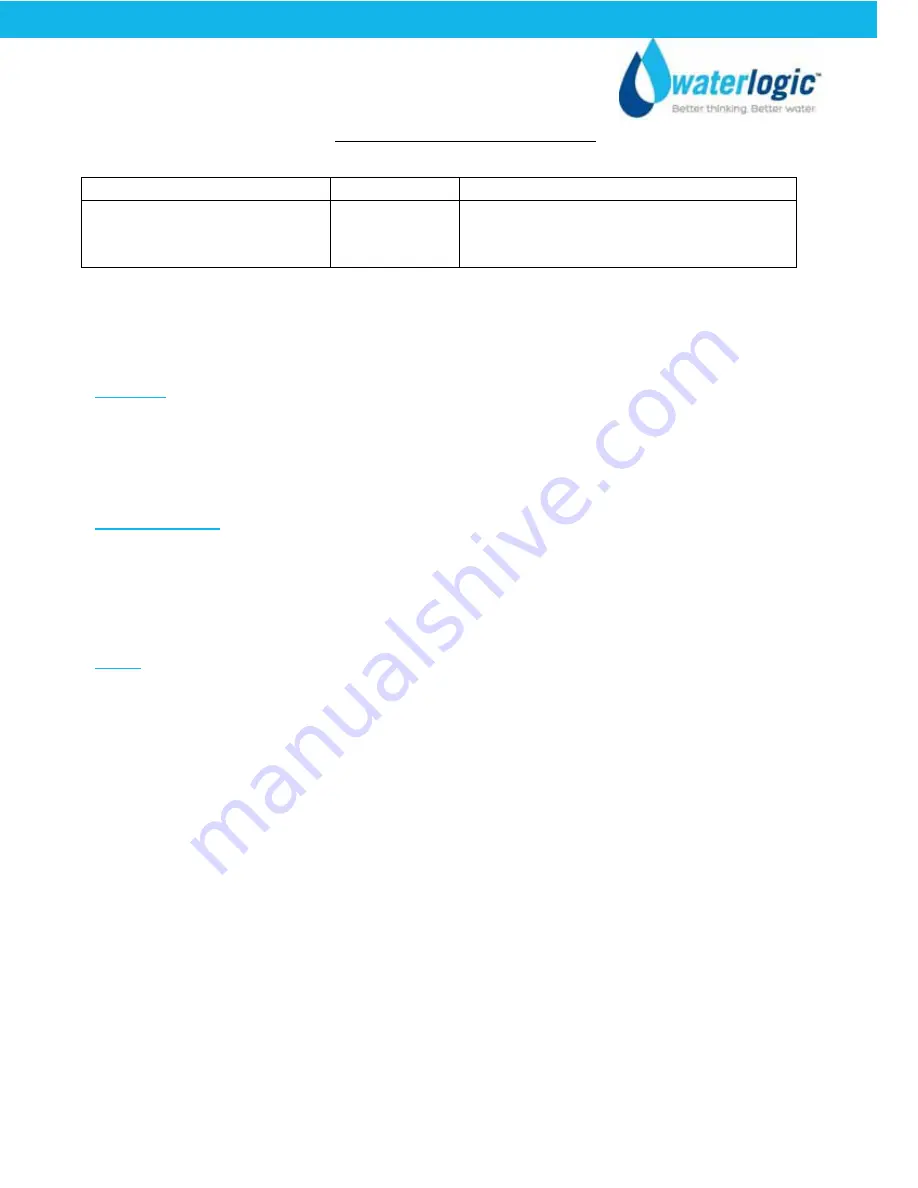
WL100
Operating,
Installation,
and
Service
Manual
Page
24
Revision:
5
‐
20
‐
2016
REPLACEMENT
COMPONENTS
Component
Part
No.
Frequency
of
Replacement
Hot
Tank
Factory
Set
Point
85°C
(185°F)
HT
‐
3041
Replace
every
3
‐
5
years
depending
on
usage.
WLCP
Part
No.
12
‐
5615
Replacement
parts
can
be
obtained
from
Waterlogic
or
an
Authorized
Waterlogic
Dealer
.
See
Parts
Layouts,
Drawings,
and
Lists
for
additional
repair
parts.
Sanitizing
Sanitization
must
be
performed
at
least
once
a
year
to
eliminate
any
potential
microbiological
contaminates.
See
Sanitizing
Instructions
in
the
Pre
‐
Installation
section
of
this
manual.
Hot
Tank
Service
Hot
Tanks
(with
controls)
must
be
replaced
at
least
every
3
‐
5
years
depending
on
usage.
Descaling
hot
tank
may
be
required
on
a
regular
basis
depending
upon
filtration
and
local
water
conditions.
See
Hot
Tank
Descaling
Instructions
Section
of
this
manual.
NOTE
:
At
the
end
of
this
product’s
life
,
ensure
that
it
is
disposed
of
in
an
environmentally
friendly
manner
which
is
fully
compliant
with
all
Federal/State/Local
Requirements
and
Guidelines.