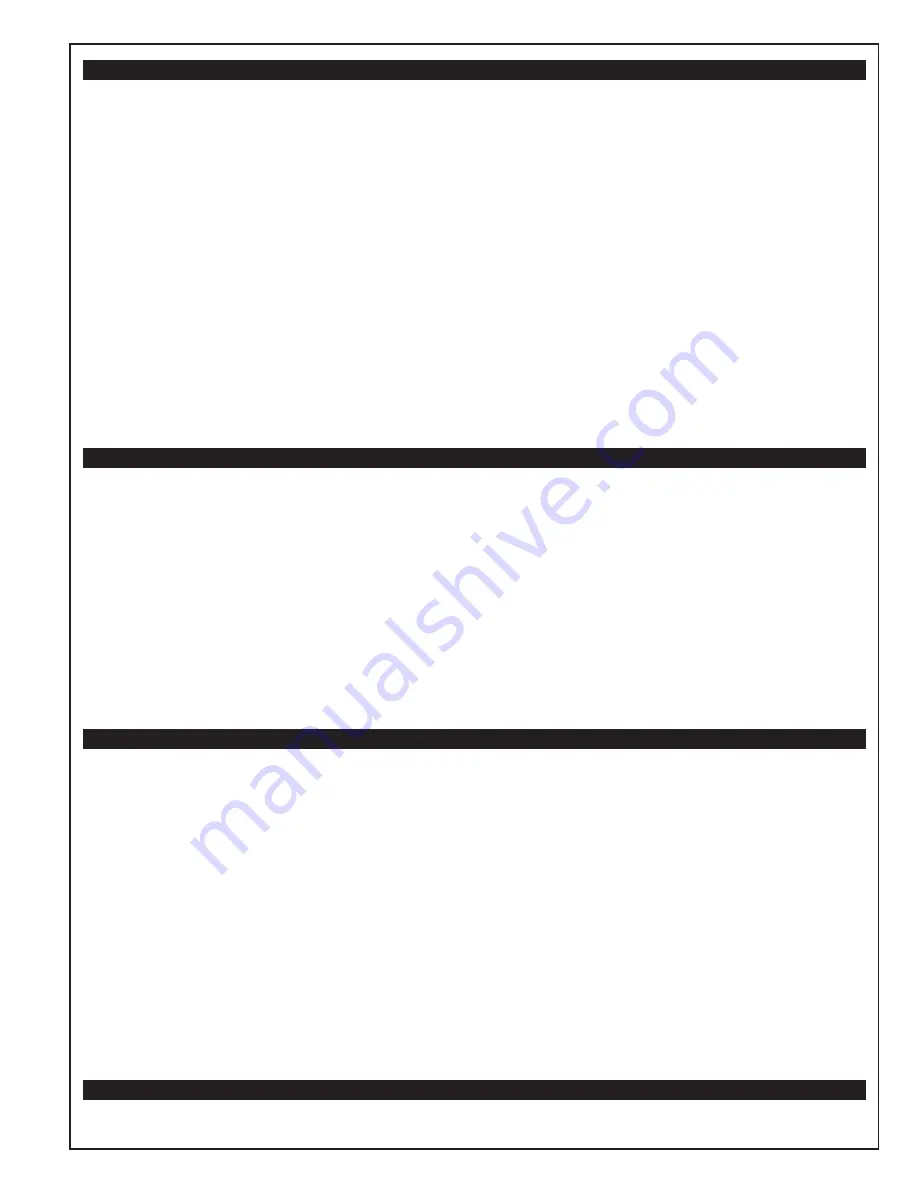
PLUMBING INSTALLATION
NOTE:
Refer to FIgure 10 for installation dimensions and drainline connections.
1.
Plumb unit using valves and fittings as shown typically in Figure 7.
NOTE:
Syphon breaker, available as option item, is approved in most areas. Check local code to be sure it conforms in your area.
2
. When overhead spray rinse is used, split the incoming 3/4” cold water into two 1/2” lines and connect one to the 1/2” “T” at the bottom of the
unit and the other to the globe valve on the cold water side of the spray rinse. Connect one 1/2” hot water line to the globe valve on the hot
water side of the spray rinse.
3
. On models 3000, 5000, and 10000 connect 3” drain to the hush connector.
Drain line must have a minimum of bends
. The unit is
equipped with a drain outlet designed for a connection to a conventional 3” trap. For model 2000 drain line and trap will be 2”.
IMPORTANT!
Before installing the Waste King
®
disposer, the connecting waste line must be
cleaned out
all the way to the connecting sewer
main. DO NOT CONNECT INTO GREASY TRAP.
The trap may be connected to a 3” branch waste line running directly into the stack. For model 2000, branch waste line can be 2”. A mini-
mum slope of 1/4” per foot of run of waste line is recommended. Limit the horizontal drain line to a 15 foot run free of turns; then, using a
long 45° “Y”, connect to a 3” or 4” horizontal line or stack. Recessed thread fittings must be used throughout and all pipe ends should be
carefully reamed. A minimum number of elbows, tees, etc., reduce the possibility of plumbing stoppages. Water is injected to underside of
table chamber through a control that allows approximately 4 gallons per minute flow. Do not restrict or alter this control as it is necessary to
properly clean the inside of the unit.
IMPORTANT
: If unusual sewer conditions exist (too many bends or too long to main), if the water pressure is low for application resulting in low
water flow rate, or if high percentage of leafy and/or paper material is included in food waste, serious consideration should be given to the use of
a time delay and water injector into the sewer to overcome stoppages. Under such conditions a larger size cold water line should be used along
with larger solenoid valves and syphon breakers. (Parts and data available from factory.)
*Minimum Water Flow RATE Used with Model:
2000 and 3000 – 10 gallons per minute.
5000 and 10000 – 14 gallons per minute.
TESTING
IMPORTANT! Do not test or run disposer without minimum water flow (see Plumbing Installation) as this
will damage the seal and void the warranty.
1
. Test assembly for leaks:
a. Where cone sink joins table
b. Where disposer joins cone sink
c. At all piping connections
d. Where swirl spray fittings connect
2
. After plumbing and electrical connections are made, turn on disposer to be sure all parts are in working order and that the disposer turntable
rotates clockwise when viewed from above. Open valve in vacuum breaker line and, using globe valves in plumbing assembly (Refer to
Figure 6), adjust so that water swirls around just below the rim of the cone sink. Leave valves open in these positions.
NOTE:
When the convertible swirl spray is used to remove food waste from dishes, adjust the flow to provide a convenient combination of
anti-splash and high flow volume characteristics (top of flume approximately 3” above cone sink). These combinations provide a flow of
approximately 8 gallons of water per minute.
3
. Replace cover, retest for leaks and turn unit off.
4
. Unit is now ready for operation.
OPERATING INSTRUCTIONS
IMPORTANT! Do not test or run disposer without minimum water flow (see Plumbing Installation) as this
will damage the seal and void the warranty.
1
. Push “start” button. Be sure unit is running and water is flowing before any waste is fed into the disposer. Do not pack food waste into unit.
Do not dump garbage can loads directly into unit. Feed waste in gradually.
2
. DO NOT ALLOW GLASS, METAL OR CROCKERY TO ENTER. IF THIS OCCURS, STOP THE UNIT AND REMOVE SUCH MATERIAL.
3
. IF THE MOTOR STOPS, push stop button. Remove any waste material which caused stoppage. Check the turntable to see that it will turn
freely. Wait three minutes, push red reset button firmly (LOCATED ON JUNCTION BOX OF MOTOR). Then push “start” button.
4
. If the motor hums and the turntable does not rotate freely, there is usually a jamming obstruction, such as metal. STOP UNIT. With a suitable
bar or stick, pry against one of the impellers and rotate the turntable in a counterclockwise direction. When the turntable is free, REMOVE
THE BAR AND THE OBSTRUCTION MATERIAL BEFORE RESTARTING UNIT. CAUTION – LOSS OF ONE PHASE IN THREE PHASE
UNITS (if one fuse blows while running) WILL CAUSE MOTOR TO LABOR AND HEAT. PROLONGED OPERATION WILL DAMAGE THE
MOTOR.
5
. If the motor remains silent after resetting the overload protector (as instructed in item 3 above) and the turntable rotates freely, check the
electric fuses and complete electrical circuit.
6
. ALWAYS ALLOW THE DISPOSER AND THE WATER TO RUN FOR THREE MINUTES AFTER EACH OPERATION to keep the unit clean
and to flush all food waste out of the drain lines. THIS IS IMPORTANT!
CAUTION
: ALWAYS TURN THE DISPOSER OFF AND LET IT COME TO A STANDSTILL BEFORE PUTTING YOUR HAND INTO THE HOP-
PER OR NEAR THE GRINDING CHAMBER.
DO NOT
LOOK FOR CAUSE UNTIL STARTING CONTROL IS TURNED
OFF
.
ELECTRICAL INSTALLATION
1.
Use waterproof conduit and make all electrical connections according to local codes.
2
. Wire three phase units using manual switches as shown in wiring diagram, Figure 12.