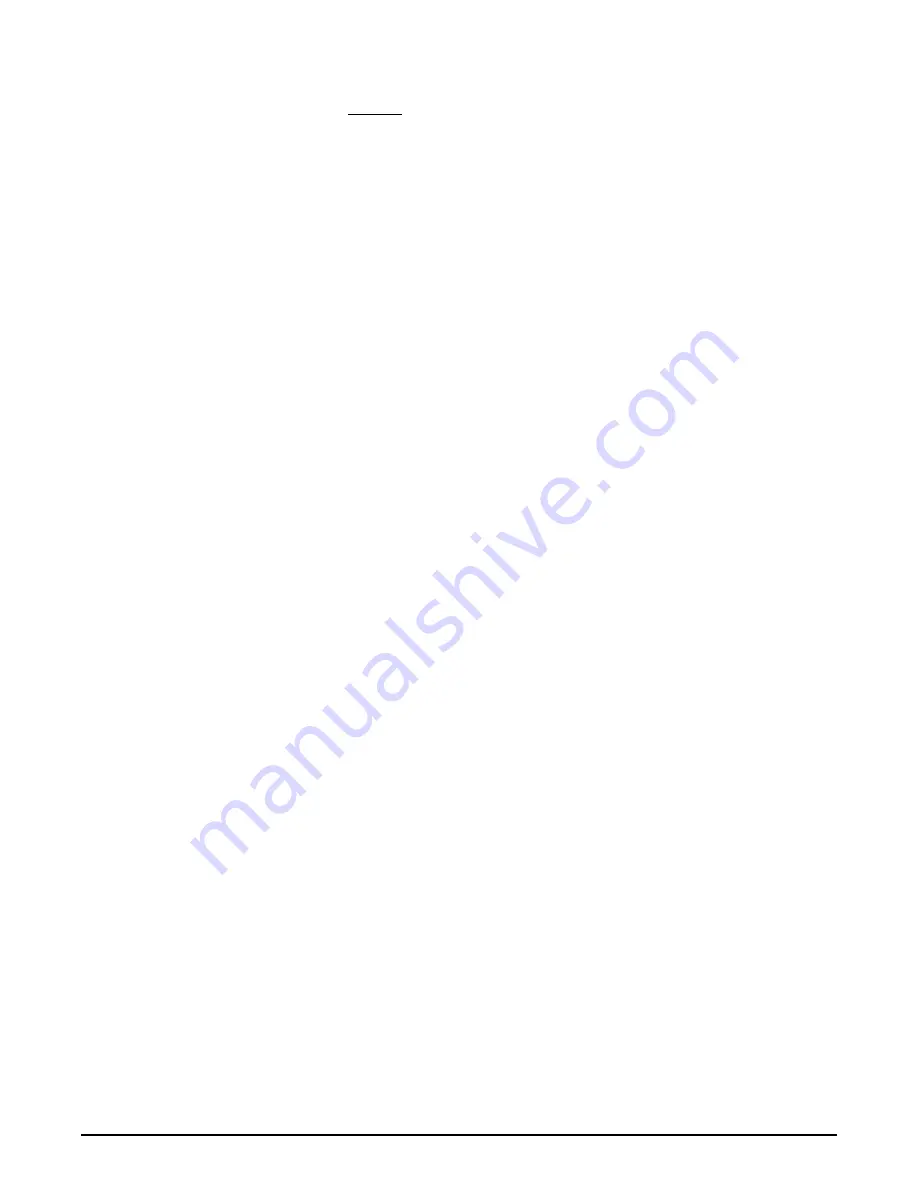
msb2dl3sm-REV0317
Model MSB2 Page 3
To re-install the sleeve and spool set, lightly lubricate the o-rings on the sleeve
with an o-ring assembly lubricant or lightweight oil (such as 10 wt. air line lubricant).
Re-install one end cap, gasket and bumper on the valve body. Using the arbor press
or bench vise that was used in disassembly, carefully press the sleeve back into the
valve body, without shearing the o-rings. You may have to clean the surfaces of the
valve body where the end caps mount. Material may remain from the old gasket. Old
material not cleaned from this area may cause air leakage after reassembly. Take care
that the bumper stays in place allowing the sleeve to press in all the way. Reinstall the
spool, opposite end cap, gasket and bumper on the valve body. After inspecting and
cleaning the gasket surfaces on the valve body and intermediate, reinstall the valve
body on the pump using new gaskets. Tighten the four hex head capscrews evenly
and in an alternating cross pattern.
AIR EXHAUST
If a diaphragm fails, the pumped liquid or fumes can enter the air end of the pump,
and be exhausted into the atmosphere. When pumping hazardous or toxic materials,
pipe the exhaust to an appropriate area for safe disposition.
This pump can be submerged if materials of construction are compatible with the
liquid. The air exhaust must be piped above the liquid level. Piping used for the air
exhaust must not be smaller than 1" (2.54 cm). Reducing the pipe size will restrict
air flow and reduce pump performance .When the product source is at a higher level
than the pump (flooded suction), pipe the exhaust higher than the product source to
prevent siphoning spills. (See page 7)
Freezing or icing-up of the air exhaust can occur under certain temperature and
humidity conditions. Use of an air dryer unit should eliminate most icing problems.
BETWEEN USES
When used for materials that tend to settle out or transform to solid form, the pump
should be completely flushed after each use, to prevent damage. Product remaining
in the pump between uses could dry out or settle out. This could cause problems
with valves and diaphragms at re-start. In freezing temperatures, the pump must be
drained between uses in all cases.
CHECK VALVE SERVICING
Need for inspection or service is usually indicated bt poor priming, unstable cycling,
reduced performance or the pump's cycling, but not pumping.
Inspect the surfaces of both check valves and seats for wear or damage that could
prevent proper sealing. If pump is to prime properly, valves must seat air tight.
DIAPHRAGM SERVICING
Remove the eight bolts (four each side) securing the manifold assemblies to the
outer chambers. Remove the eight bolts securing the outer chamber to the inner
chamber. Remove the diaphragm assembly (outer plate, diaphragm, inner plate) by
turning the assembly counterclockwise using a 16/16" (2.38 cm) wrench on the outer
plate lugs. To disassemble the diaphragm assemblies, secure in a vise and turn the
outer plate counterclockwise using the 16/16" wrench.
Procedures for reassembling the diaphragms are the reverse of the above. The dia-
phragms must be installed with their natural bulge to the outside, toward the outer
diaphragm plate. Install the inner plate with the flat face against the diaphragm.
After all components are in position in a vise and hand tight, tighten with a wrench to
approximately 40 ft. Ibs. (54.23 Newton meters) torque. After both diaphragm assem-
blies have been assembled, thread one assembly into the shaft (hold the shaft near
the middle in a vise with soft jaws, to protect the finish). Install this sub assembly into
the pump and secure by placing the outer chamber on the end with the diaphragm.
This holds the assembly in place while the opposite side is installed. Torque the last
diaphragm assembly to 30 ft. Ibs. (40.67 Newton meters). This final torquing will
lock the diaphragm assemblies together. Place the rernaining outer chamber on the
open end and loosely tighten the bolts. Replace the manifold assemblies to square
the flanges before final tightening of the remaining bolts. the diaphragm assemblies
together. Place the rernaining outer chamber on the open end and loosely tighten the
bolts. Replace the manifold assemblies to square the flanges before final tightening
of the remaining bolts.