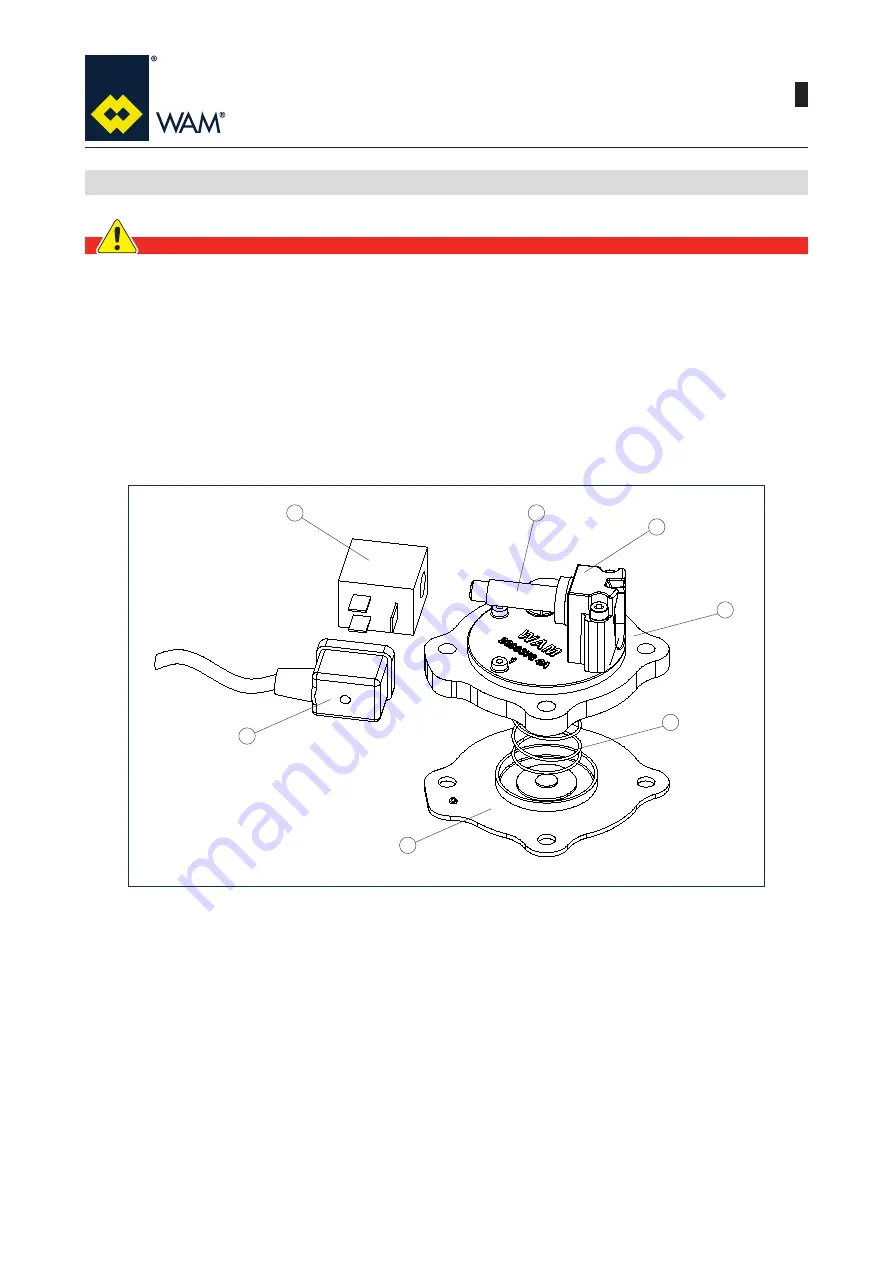
8.0 REPLACEMENT OF PARTS
WAMFLO
®
FN200X
2
FIL.WAMFLO_FN200.EX.M.A7.0522.EN Issue: A7
05.22
59
8.5 Replacing the solenoid valve
Danger - Warning
Set the filter in safety condition (see "Glossary and Terminology").
1)
Remove the coil (
6
) and the connector (
7
) after having removed the relative ring nuts;
2)
Remove the hex screws and washers which secure the valve cover
(3)
;
3)
Replace the diaphragm (
1
) and the spring (
2
);
4)
Ensure the diaphragm (
1
) is positioned above the vent hole;
5)
Insert the spring (
2
);
6)
Fit the new cover (if provided) by checking that the spring is over the shoulder of the disc diaphragm and the
cover is positioned over the vent hole.
1
•
7
•
2
•
3
•
4
•
5
•
6
•