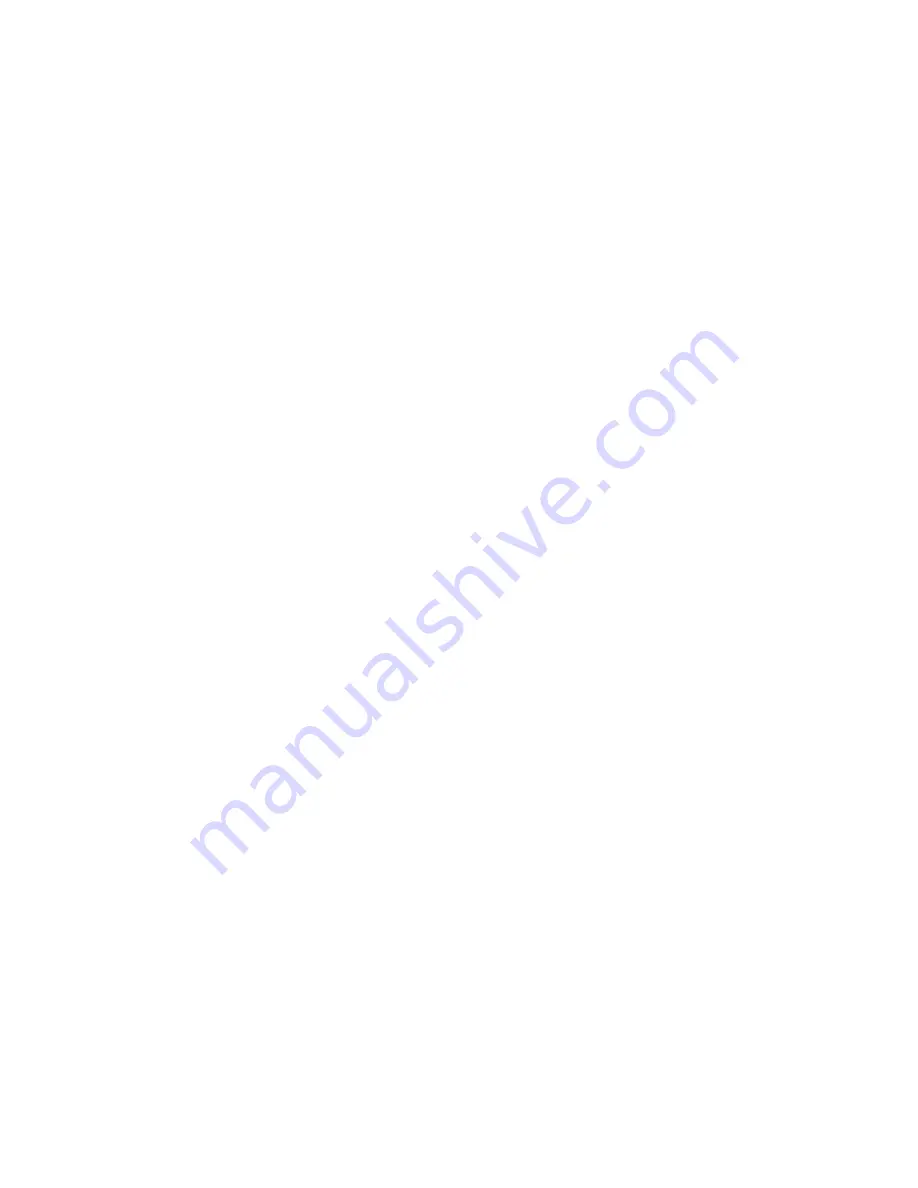
78
porating backup pump controls and optional time based activation. If the pH rises above 8.50 when pump R1 has
an active Flow Verify alarm or is in HOA Off mode, pump R2 immediately energizes. R3 energizes when the pH
goes above 9.00. Although no third pump is available to activate if the pH continues to rise above 9.50, this control
system is more fault tolerant than the currently available options.
Switch Based
When using switch based activation mode, each Lag output has an Activate With Channels setting that is used
to specify one or more digital input or relay output channels that activates an additional output. Switch based
activation mode incorporates time based activation and can also be configured to trigger an additional output (if
available) after a specified delay time. This menu selection is available only when the Lead output is using Manual
control mode.
Example 1: A lift station includes a tank with a high level switch (D1) and a high-high level switch (D2). Three
pumps are configured as a Lead Lag group (R1←R2←R3). The Lead output (R1) is set for Manual control mode
with an Activate With Channels selection of D1 (high level switch), R1 will be energized if D1 closes. The first Lag
output (R2) has an Activate With Channels selection of D2 (high-high level switch). The last Lag output (R3) has
no Activate With Channels selected. All pumps are in HOA Auto mode. The delay time is disabled (set for 0:00
minutes). Wear leveling is disabled. When the high level switch closes, the R1 pump is activated. If the high-high
level switch closes, the R2 pump is also activated. When D2 opens, R2 is turned off. When D1 opens, R1 is turned
off. In this configuration, the R3 pump serves only as a backup in case one of the pumps is down for maintenance
(in HOA Off mode).
Example 2: The same lift station, two-level switches, three-pump configuration (R1←R2←R3) as in Example 1
except the delay time is set for 1 hour. When the high level switch closes, the R1 pump is activated. If the high-high
level switch closes, the R2 pump is also activated. If the tank level remains above the high-high level switch for
another 1 hour, the R3 pump is activated. When D2 opens, R3 is turned off. When D1 opens, both R2 and R1 are
turned off. In this configuration, the R3 pump serves not only as a backup in case one of the pumps is down for
maintenance, but also provides additional capacity should it be needed.
Advanced Functionality
The examples listed above detail the control behavior if wear leveling or output activation modes are enabled. The
features are implemented independently. Wear Leveling modes are used to determine which output(s) are activated.
Output Activation modes determine how many output(s) are activated at one time. More advanced output control
strategies can be implemented when these features are used in combination.
Example: In a two-pump scenario, the Lead output (R1) is set for On/Off control of pH with a setpoint of 8.50,
deadband of 0.20 and a “force lower” control direction. The Lag output (R2) has a setpoint of 9.00 and a dead-
band of 0.20. Time unbalanced (60/40) wear leveling is selected with a cycle time of 15 minutes. When the pH goes
above 8.50, the on-times for each pump are evaluated. If R1 has been on less than 80% of the total time for the two
pumps, it is energized. Otherwise, R2 has been on for less than 20% of the total time, so it is energized. If the pH
remains above the deadband and does not exceed the second setpoint (8.30 < pH < 9.00), the pump selection is
re-evaluated every 15 minutes and, if warranted, the pump in operation is switched. If the pH proceeds to exceed
9.00, both pumps are energized and wear leveling is no longer a consideration. When the pH fails to below 8.80,
the pump on-times are again evaluated and the appropriate pump is turned off.
Note that while this control is quite powerful, it might cause confusion with users because the setpoints entered
for a specific pump within the Lead Lag group may not coincide with the setpoints used to activate that particular
pump during operation. The information shown on the Details pages for each pump should be sufficient to mini
-
mize this ambiguity.
Control Mode Conflicts
Some control modes are incompatible with Lag output functionality because of an interactive relationship between
the output and one or more linked inputs:
• Intermittent Sampling – This control mode places a linked sensor into a Hold state during most of its operational
cycle
• Probe Wash – This control mode places one or two linked sensors into a Hold state when a wash cycle is in
progress and for a specified Hold period afterward