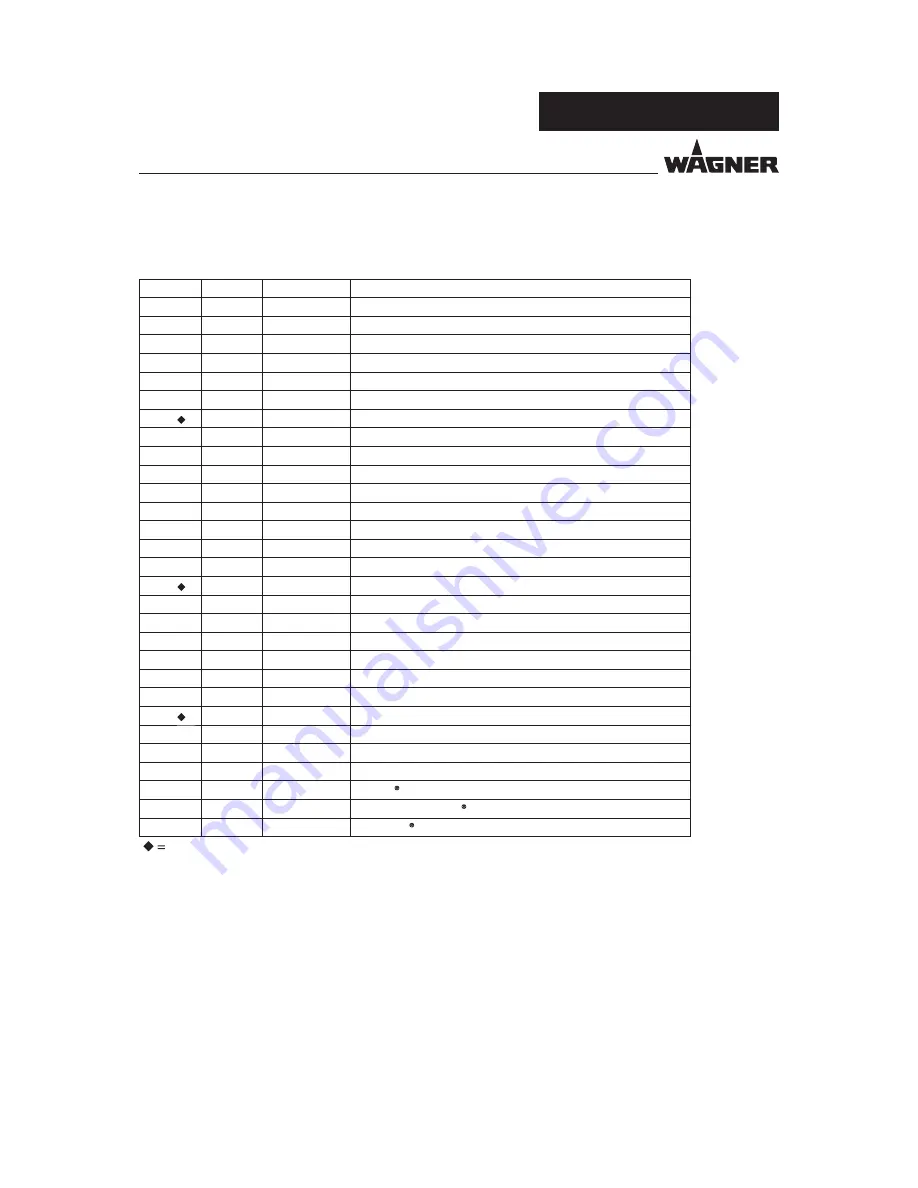
92
PROTEC 2K
OPERATING MANUAL
VERSION 02/2016
ORDER NUMBER DOC2352824
Spare parts list for mixing
Pos
K
Stk
Order No.
Designation
1
1
--
Mixing, complete
2
1
2350342
Handle, blue
3
4
2325554
Fillister head screw, M6x12
4
2
2352612
Locating screw
5
2
9999500
Helical spring, air
6
1
2349800
Switching bracket, complete
7
2
2357790
Circulation, complete
9
2
384323
Plug
10
2
104376
Screw plug
11
2
2331174
Fitting, DF-MM-G1/4-G1/4-530 bar-SSt
12
1
9907127
Fitting-PF-M-G3/8-530bar-SSt
13
1
2330775
Fitting, DF-MM-G3/8-G3/8-530 bar-SSt
14
1
3204619
Fitting, EF-MM-G3/8-R3/8-530bar-SSt
15
1
2349830
Handle, red
16
1
2331371
Fitting, SF-FM-G3/8-G3/8-530 bar-SSt
17
2
2350087
Ball valve PN 530 G3/8 DN10
18
2
2349776
Side holder, 45 degree
19
2
2349832
Spring washer
20
2
9907206
Hexagon screw without shaft
21
1
2357789
Mixing block, complete (for details see Chapter 13.6.1)
22
2
2332966
Fitting, DF-MM-M22x1.5-G3/8-530 bar-SSt
23
1
384098
Mixing tube, complete 10-32E ST/KS (including pos. 24)
24
1.33
9999446
Mixing element
25
1
2352556
Spacer plate
26
1
9998683
Hose clamp
27
1
2332620
Fitting RF-FM-G3/8-3/8NPSM-530 bar-SSt
30
1
9992831
Loctite 542
31
1
9992511
Lock screw Loctite 243
32
1
9992616
Molykote DX grease
Wearing parts
13.6
MIXING
Summary of Contents for PROTEC 2K
Page 2: ......
Page 21: ...21 PROTEC 2K OPERATING MANUAL VERSION 02 2016 ORDER NUMBER DOC2352824...
Page 38: ...38 PROTEC 2K OPERATING MANUAL VERSION 02 2016 ORDER NUMBER DOC2352824...
Page 110: ...110 PROTEC 2K OPERATING MANUAL VERSION 02 2016 ORDER NUMBER DOC2352824...
Page 120: ...120 PROTEC 2K OPERATING MANUAL VERSION 02 2016 ORDER NUMBER DOC2352824...
Page 131: ......