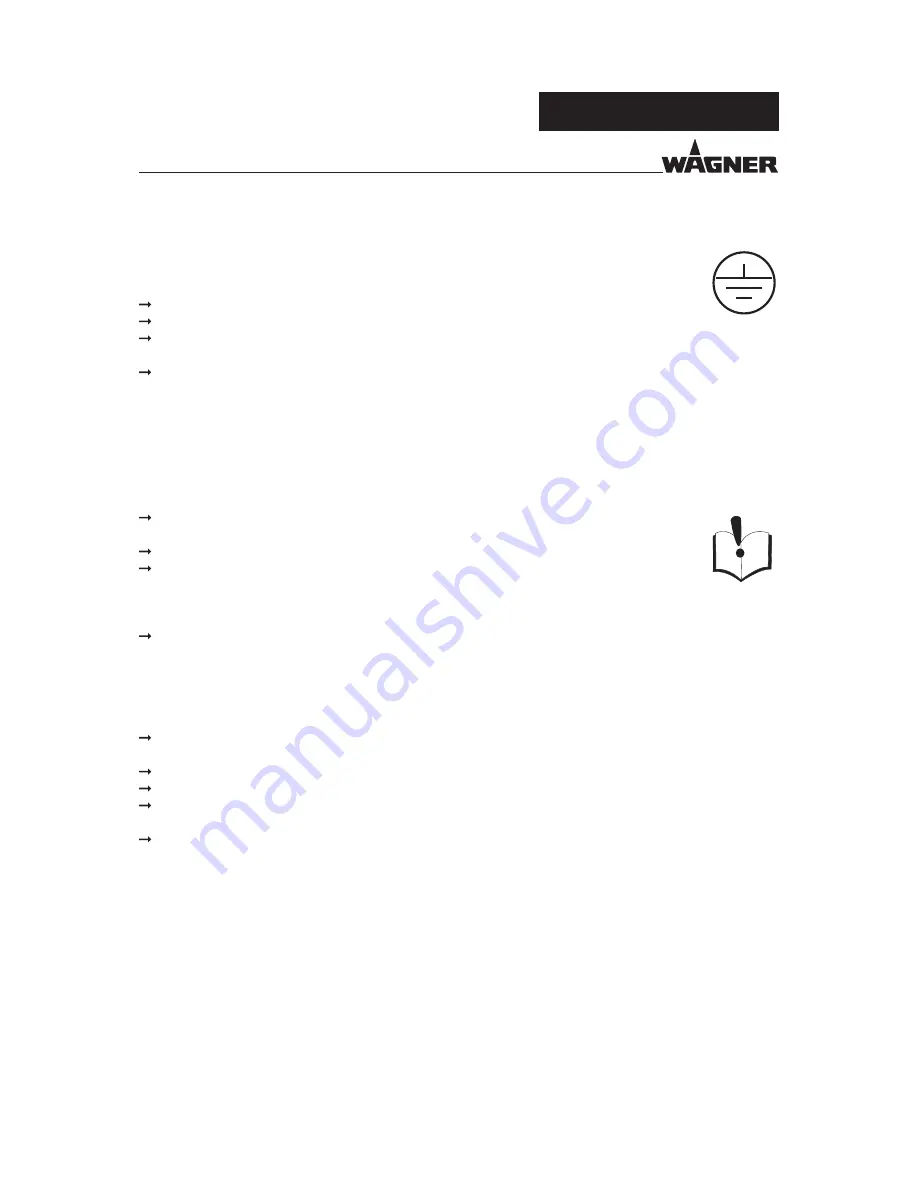
16
GM 4700AC
OPERATING MANUAL
VERSION 06/2014
ORDER NUMBER DOC2311730
4.2.3
PRODUCT HOSES
4.2.2
GROUNDING THE DEVICE
In order to avoid electrostatic charging of the device, the device must be grounded.
Friction, fl owing liquids, and air or electrostatic coating processes create charges. Flames
or sparks can form during discharge.
Ensure that the device is grounded for every spraying operation.
Ground the work pieces to be coated.
Ensure that all persons inside the working area are grounded, e.g. that they are wearing
static dissipative shoes.
Wear static dissipative gloves when spraying. The grounding takes place via the spray
gun handle.
Ensure that the hose material is chemically resistant to the sprayed products and the
used fl ushing agents.
Ensure that the product hose is suitable for the pressure generated.
Ensure that the following information can be seen on the high-pressure hose:
-
Manufacturer
- Permissible operating pressure
- Date of manufacture
Make sure that the hoses are laid only in suitable places. Hoses should not be laid in the
following places under any circumstances:
- In high-traffic areas
- At sharp edges
- On moving parts
- On hot surfaces
Ensure that the hoses are never run over by vehicles (e.g. fork lifts), or that the hoses are
never put under pressure from the outside in any other way.
Ensure that the hoses are never kinked. Observe maximum bending radii.
Make sure that the hoses are never used to pull or move the device.
The electrical resistance of the product hose, measured at both valves, must be less
than 1 megohm.
Suction hoses may not be subjected to pressure.
Several liquids have a high expansion coeffi
cient. In some cases, their volume can rise with
consequent damage to tubes, fi ttings, etc. and cause fl uid leakage.
When the pump sucks liquid from a closed tank, ensure that air or a suitable gas can
enter the tank. Thus a negative pressure is avoided. The vacuum could implode the tank
(squeeze) and can cause it to break. The tank would leak and the liquid would fl ow out.
The pressure created by the pump is a multiplication of the inlet air pressure.
Summary of Contents for GM 4700AC
Page 2: ......
Page 55: ...55 GM 4700AC 55 GM 4700AC OPERATING MANUAL VERSION 06 2014 ORDER NUMBER DOC2311730...
Page 79: ......