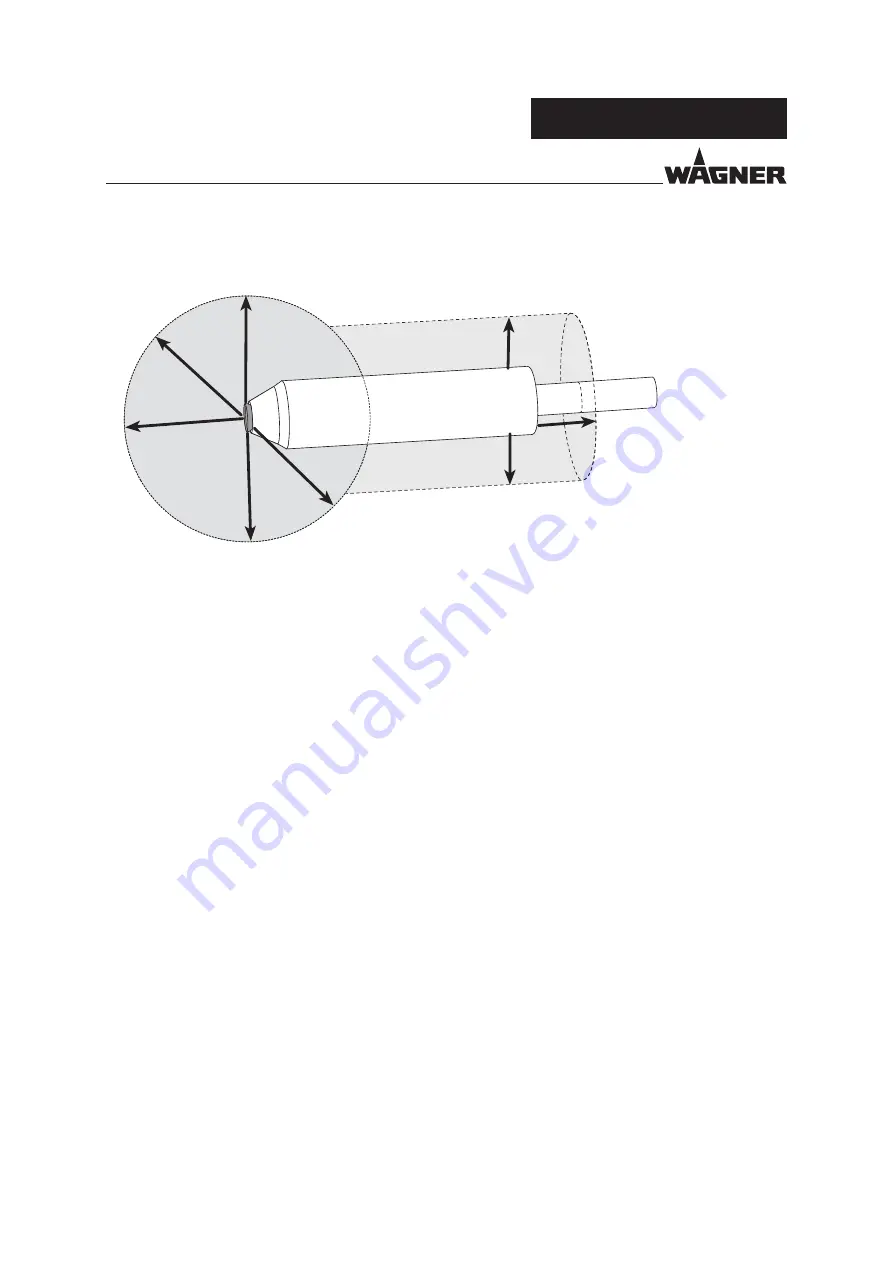
12
Evobell 3500
B_01195
200 mm;
8 inches
100 mm;
4 inches
OPERATING MANUAL
EDITION 05/2010
PART NO. DOC387841
Danger zone:
The distance between the workpieces and the parts of the spray system under high volt-
age must be large enough to prevent a sparkover during normal operation. A minimum
distance of 200 mm; 8 inches is recommended in the area of the atomizer bell and a mini-
mum distance of 100 mm; 4 inches in the area of the cylindrical cover. If required by the
application or if demanded by the design, these distances can also be smaller. In this case
it is necessary to check that sparkovers do not occur.