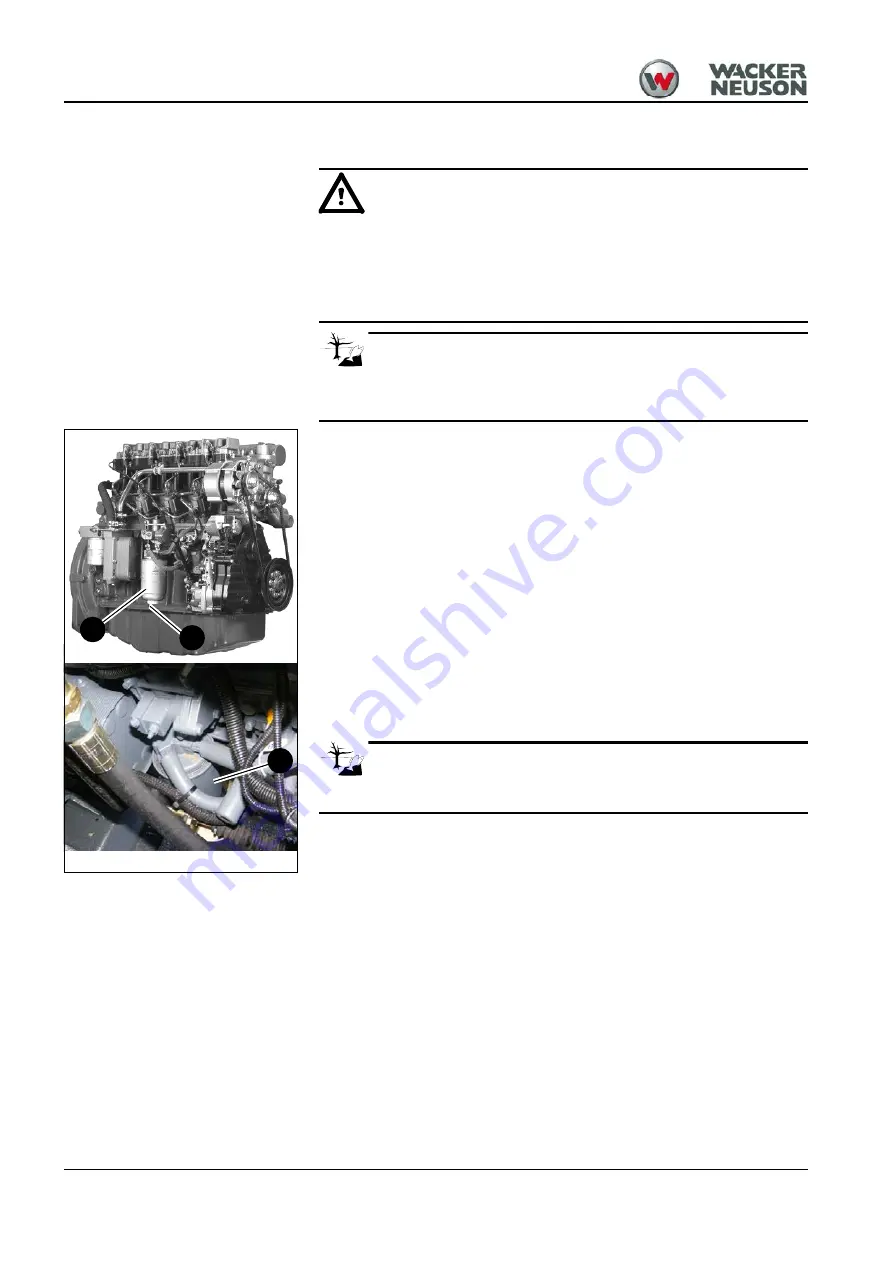
5-8
BA 5001-6001 US – Edition 1.2 * 6001b510.fm
Maintenance
Replacing the fuel filter (Deutz diesel engine)
WARNING
Fire and burn hazard. Draining fuel may ignite if it comes into contact with hot
engine parts or the exhaust system. Hot fuel may cause burns.
☞
Always wear protective equipment and safety glasses when working with
fuel.
☞
Never replace the fuel filter if the engine is hot.
Environment
Use a suitable container to collect the fuel as it drains and dispose of it in an
environmentally friendly manner!
Removing the fuel filter
Proceed as follows:
☞
Place a suitable container underneath the filter.
☞
Unscrew screw
A.
➥
The fuel runs out of the filter housing.
☞
Empty the filter housing completely.
☞
Remove filter housing
B
.
☞
Replace the fuel filter.
Installing the fuel filter
Proceed as follows:
☞
Mount and tighten all elements in the reverse order with a new filter element.
☞
Bleed the fuel system
– see
Bleeding the fuel system on page 5-7.
☞
Make a test run—and check for tightness!
Environment
Dispose of replaced fuel filters in an environmentally friendly manner!
Fig. 75: Fuel filter (Deutz diesel engine)
B
A
B
Summary of Contents for Dumper 5001
Page 8: ...I 6 BA 5001 6001 US Edition 1 2 Ba6001us1_1SIX fm Index...
Page 15: ...BA 5001 6001 US Edition 1 2 6001b110 fm 1 7 Introduction 1 7 Swivel dump bucket 5001 6001...
Page 16: ...1 8 BA 5001 6001 US Edition 1 2 6001b110 fm Introduction 1 8 Front dump bucket 6001...
Page 32: ...2 12 BA 5001 6001 US Edition 1 2 6001b210 fm Safety Information...
Page 118: ...5 40 BA 5001 6001 DE Edition 1 2 6001b560 fm Maintenance...