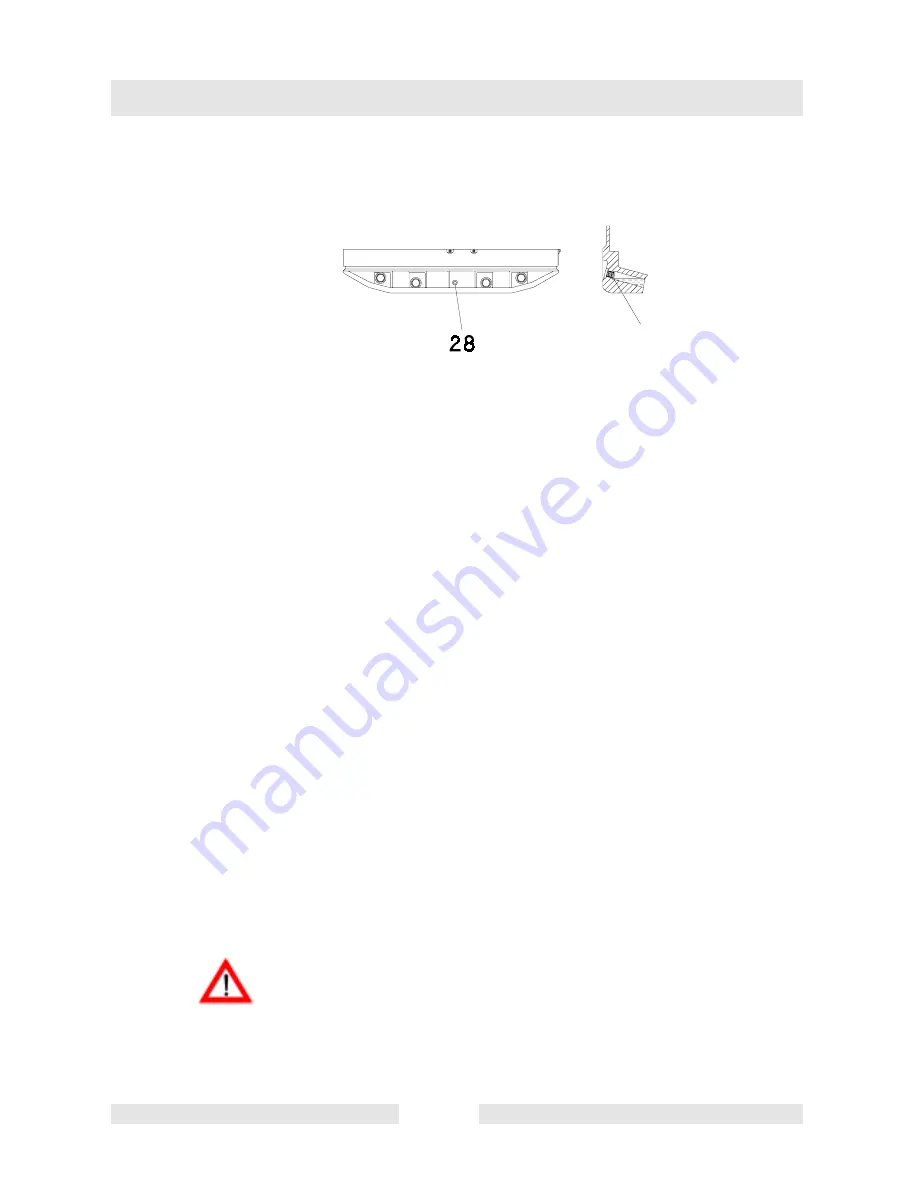
Maintenance
T01051GB
28
7.5
Exciter
Check oil level:
1. Position vibration plate horizontally.
2. Open filler bore (28).
3. The oil level must reach the start of the thread of the filler bore.
4. Fill with oil through filler bore if necessary (see Technical Data). Use
a suitable funnel.
5. Close filler bore. (Tightening torque100 Nm)
Changing the oil:
1. Remove extension plates if necessary.
2. Open filler bore.
3. Tilt vibration plate and keep it tilted until the oil has run out.
4. Place vibration plate in horizontal position.
5. Fill oil through filler bore (see Technical Data).
6. Close filler bore (28).
7. Mount extension plates if necessary.
(Tightening torque100 Nm)
Do not pour in too much oil!
Take notice: Please pay attention to the corresponding environmental
rules and regulations when disposing of used engine oil. We
recommend you carry the oil in a closed container to a central
collecting point for used oils. Do not pour used engine oil into the
garbage nor into the sewer system, drains or even on the ground.
Lower end of thread
Summary of Contents for DPU 7060SC
Page 1: ...www wackergroup com Operator s Manual Vibratory Plate DPU 7060SC 0203971en 004 11 2006...
Page 2: ......
Page 38: ......
Page 41: ......
Page 42: ......