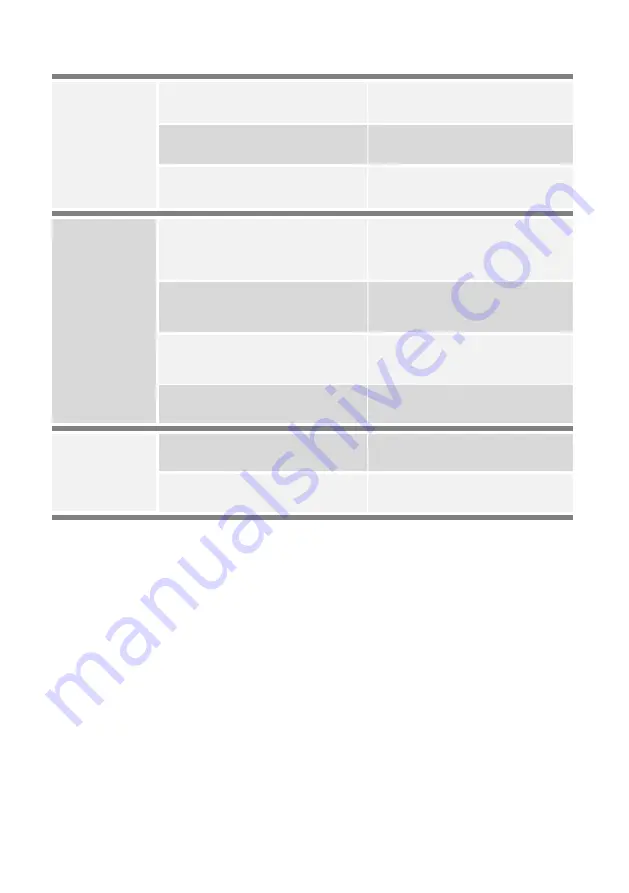
62
MAINTENANCE
TRANSLATION
REDUCTION
GEARS DO NOT
FUNCTION
PIPES, CONNECTIONS,
FITTINGS DAMAGED
DAMAGED PUMPS
TRANSMISSION
DISENGAGEMENT SCREW
LOOSENED
INSPECT AND REPLACE THE
COMPO-NENT CONCERNED IF
NECESSARY
INSPECT AND CALL AN
AUTHORISED WORKSHOP
CHECK AND EVENTUALLY
TIGHTEN CORRECTLY
ONE REDUCTION
GEAR DOES NOT
FUNCTION
HYDRAULIC MOTOR DAMAGED
FEED VALVE DAMAGED
PIPES, CONNECTORS DAMAGED
TRANSMISSION
DISENGAGEMENT SCREW
LOOSENED
INSPECT AND REPLACE IF
NECESSARY (CALL AN
AUTHORISED WORKSHOP)
INSPECT AND REPLACE IF
NECESSARY (CALL AN
AUTHORISED WORKSHOP)
INSPECT AND REPLACE THE
COMPO-NENT CONCERNED IF
NECESSARY
CHECK AND EVENTUALLY
TIGHTEN CORRECTLY
PUMP FAULTY OR BROKEN
MOTOR REDUCER
FAULTY OR BROKEN
INSPECT (CALL AN
AUTHORISED WORKSHOP)
INSPECT (CALL AN
AUTHORISED WORKSHOP)
VARIOUS SPEED
OF THE BRACE OF
WHEELS