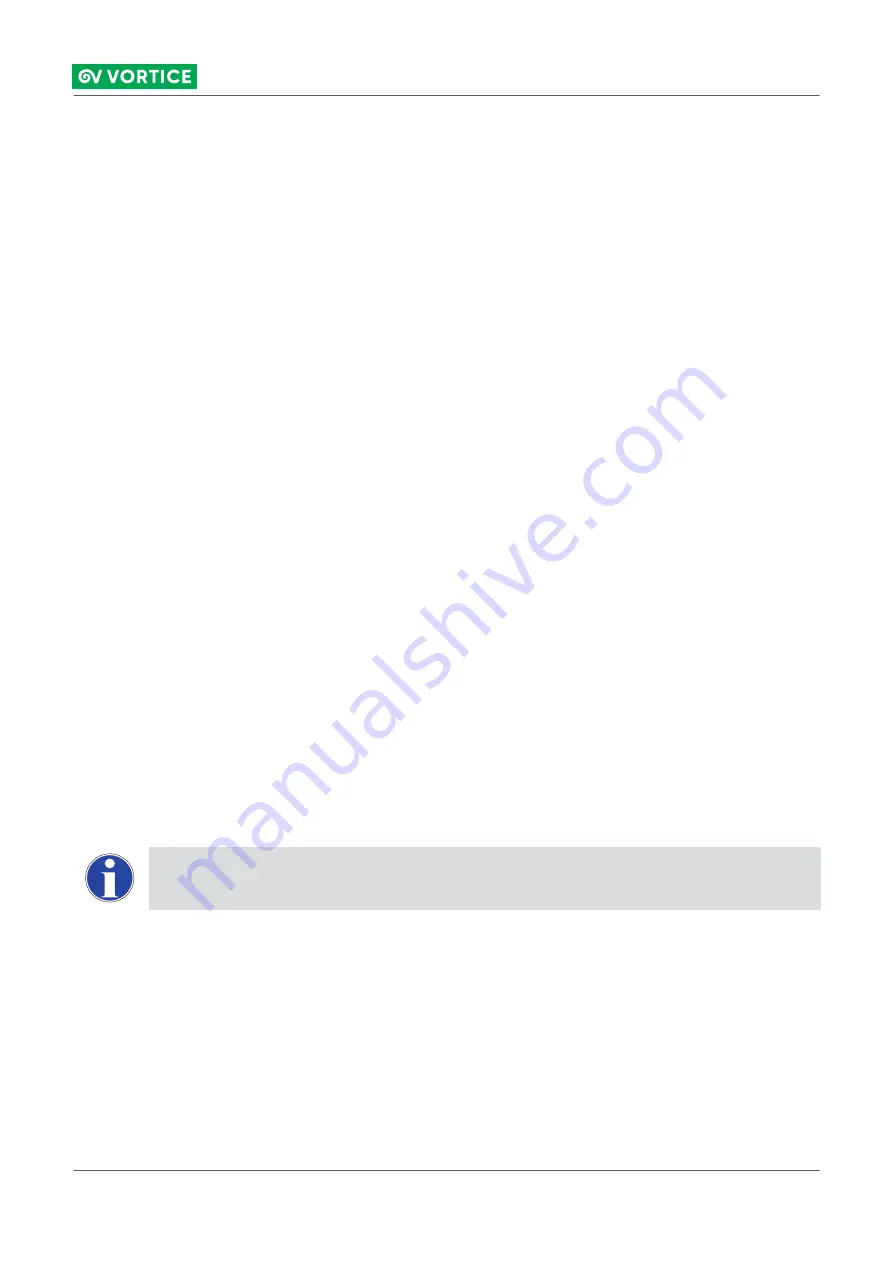
12
INSTALLATION OPERATIONS AND MAINTENANCE MANUAL - VORT NRG MEGA-R SERIES
2. TECHNICAL CHARACTERISTICS
2.1 Introduction
Any occupied room requires the correct supply of fresh air and, at the same time, the control of the internal thermo-
hygrometric conditions, through the recovery of energy from the air extracted from the room, by means of static counter-
flow heat recoveries, the level of well-being of the occupants is guaranteed, both in summer and winter.
For buildings that require air changes and are not equipped with dedicated air conditioning systems, the installation of such
units allows the supply of primary air at controlled temperature without substantially changing the internal conditions in the
occupied spaces. These units also make it possible to guarantee support for the air conditioning system in the intermediate
seasons using free-cooling or free-heating modes. These units, if installed on existing buildings, guarantee the energy
requalification of the system through the management of the air change without additional charges; in the case of new
installations, instead, the air change is completely carried out allowing to reduce the size of the main air conditioning system.
In the intermediate seasons the building will benefit from free or partially-generated cooling from these units, which during
the partial load phases allow the main system to operate with higher efficiency.
The units are available in 10 sizes, with nominal air flow rates from 1000 to 21500 m
3
/h.
The units in have been designed for false ceiling installation, while those in
V1
,
V2
,
V3
,
V4
configurations are suitable for floor
installation. All configurations are available in the
H1
and
H2
configuration with the relative
ECO
,
PLUS
,
TOP
version.
2.2 Structure
The structure of the units can be realized in two versions:
VERSION 1:
Profiles 50 x 50 mm in self-supporting extruded anodized aluminium, with mechanical strength requirements in accordance with
EN 1886: D1 (M). 50 mm thick double-walled sandwich type paneling with exterior in pre-painted RAL 9010 galvanized sheet steel
and interior in hot-dip galvanized sheet steel with interposed insulation made of polyurethane foam with a density of 40 kg/m
3
.
This structure has a seal class L1 while the thermal transmittance and the thermal bridge characteristic is class T3/TB4 according
to EN1886.
VERSION 2:
Thermal break profiles 60 x 60 mm in self-supporting extruded anodized aluminium, with mechanical strength requirements in
accordance with EN 1886: D1 (M). 63 mm thermal break sandwich-type double-walled sandwich type panels with exterior in
pre-painted RAL 9010 galvanized sheet steel and interior in hot-dip galvanized sheet steel with interposed insulation made of
polyurethane foam with a density of 40 kg/m
3
. This structure has a seal class L1 while the thermal transmittance and the thermal
bridge characteristic is class T2/TB2 according to EN1886.
Safety microswitches are applied to the inspection doors to allow internal access to the various compartments of the unit only when
the unit is completely switched off. The main access and inspection panels consist of inspection doors with perimeter hinges made
of non-corrosive polyamide and handles.
The units are supplied as standard in a MONOBLOCK configuration, in case of multi-section units, they are
available in special execution. Please contact the Company for further details.
2.3 Heat recovery
The units are equipped with an air-to-air rotary heat recovery unit, consisting by a cylindrical rotor containing thousands
of channels and characterised by an extremely elevate surface development, a supporting frame, and an eletric motor
drive system. The heat exchange surface, very high in relation to the volume, allows very high thermal performances
when compared to other types of heat recovery systems, reaching efficiencies even above 80%. In rotary wheel heat
recovery units the heat exchange takes place by accumulating the heat in the rotor; as a matter of fact while the
cylinder rotates slowly, the exhaust air volume crosses half of the casing and gives its heat to the rotor matrix, which
accumulates it. The fresh air, crossing the other half, absorbs the accumulated heat. The parts absorbing and releasing
the heat are continuosly inverted, as the rotation proceeds, and the process may continue indefinitely. The heat
exchanger participates to the
Eurovent Certification
program and it is sized according to the
ECO Design
specification.